At the K show, three makers of injection molding machines unveiled innovative ways to integrate their machines with specialized tooling for medical and consumer packaging applications.
One process from Dr. Boy GmbH & Co. KG combines injection molding and blow molding in the same machine to produce precision, hollow parts without flash. A process from Engel Austria GmbH incorporates four-sided cube mold technology, in which injection molding of a preform takes place in one parting line and blow molding of a bottle takes place simultaneously in a second parting line. And Arburg GmbH developed a new line of injection molding machines exclusively for use with cube molds.
INJECTION AND BLOW MOLDING FROM BOY
Boy, Neustadt-Fernthal, Germany, demonstrated a new capability in which injection molding and blow molding processes take place within a single machine. An air-blowing modification on a Boy injection molding machine makes the press capable of molding small bottles for the cosmetics, pharmaceutical and food industries, said Alfred Schiffer, managing partner at Boy. The firm's U.S. headquarters is Boy Machines Inc., Exton, Pa.
One benefit is the ability to precisely manufacture complex contours at the bottle's neck, which is possible only to a limited extent in traditional blow molding, Schiffer said.
Boy demonstrated the new process on a Boy 60 E machine using a special four-plus-four mold from mold maker Schreck Kunststofftechnik GmbH, Burgwald, Germany, to produce small bottles for eye drops. Four 2.95-gram bottles made from PE were produced in a cycle time of 18 seconds. The bottles were packaged directly after demolding in an integrated clean room.
First, four preforms are injection molded onto the mold cores. The mold cores are connected to an index plate that extends the cores away from the mold base, rotates the cores from the top half of the mold to the bottom half, then retracts the cores into the mold. In this half of the mold, compressed air is delivered to inflate the preforms into a bottle. The indexing action of the mold cores is driven by the machine's Alpha 4 controller, using a hydraulic ejector.
This combination of injection and blow molding reduces material waste. According to Schiffer, the PE preforms are molded without a sprue and, unlike in conventional blow molding, bottles emerge finished after blowing. No material needs to be cut and removed. Waste is minimized by using a manifold system that was developed specifically for the injection/blow molding process by Heitec Heisskanaltechnik GmbH, Burgwald.
ENGEL SHOWS INJECTION BLOW MOLDING WITH CUBE TECHNOLOGY
Engel, Schwertberg, Austria, demonstrated how process integration can reduce packaging unit costs with the development of a new injection blow molding process using cube mold technology.
Injection blow molding makes it possible to achieve economical production of ready-to-use small containers in a single step, but the number of possible cavities has previously been limited, according to Engel. The company has developed an integrated injection and blow molding process for use with multicavity molds, using cube molds developed by system partner Foboha, Haslach, Germany. Foboha is a business of Barnes Group Inc., Bristol, Conn.
Engel produced 8-gram PP containers in an eight-cavity cube mold in an 8-second cycle on an Engel e-motion 740/220 T WP all-electric toggle-clamp model as a prototype. The containers were developed by packaging company Alpla Werke Alwin Lehner GmbH & Co. KG, Hard, Austria, for a customer in Asia that previously packaged a product in glass vessels. The injection and blow molded bottles reduce production costs and packaging weight while increasing consumer safety due to less breakage.
Injection molding and blow molding of the preforms occurs simultaneously on opposite sides of the four-sided rotating mold. Cube molds have four sides and two parting lines. This allows the molder to dedicate individual steps of the molding process to a certain parting line, allowing filling, cooling and part removal to take place simultaneously. The design of the cube mold allows the user to incorporate assembly, insertion and testing operations without increasing cycle times.
Engel's e-motion 740/220 T WP operated with the company's new iQ weight control and iQ clamp control software, which provide real-time machine control through continuous analysis of critical process parameters. Even small changes in ambient conditions or raw material are detected and compensated for in the injection stage, and clamping is more uniform.
The Engel press incorporated a compressed air delivery system from Bauer Compressors Inc., Norfolk, Va., for the blow molding station and an Engel easix six-axis robot, which precisely handles the removal of the finished containers from the tool for placement onto a conveyor belt. Part removal takes place outside of the parting line and does not increase cycle time. The multisided tooling concept allows for expanding the process to 96 cavities without compromising cycle times or molding accuracy.
Engel's CC300 control can be used to control gas pressure and all aspects of the process. The company's U.S. subsidiary, Engel Machinery Inc., is in York, Pa.
ARBURG ROLLS OUT MACHINE LINE FOR CUBE MOLDS
Arburg GmbH, Lossburg, Germany, introduced a new machine series for high-speed applications that use four-sided cube molds (See story here). Arburg's new Allrounder Cube machines are designed for use with Foboha cube molds, yet are potentially compatible with other suppliers as well. The Allrounder Cube series reduces cycle times by 10 percent with 25 percent less energy consumption, when compared to a hydraulic machine running a cube mold, Arburg said.
• Allrounder Cube machines come in two sizes: the Allrounder Cube 2900, with 319 tons of clamping force, tie-bar spacing of 32.3 inches and a mold installation space of 74.8 inches, and
• the Allrounder Cube 4600, which has 506 tons of clamping force, tie-bar spacing of 40.2 inches and a mold installation space of 94.5 inches.
Arburg Inc., the German firm's U.S. subsidiary, is headquartered in Rocky Hill, Conn.
Mikell Knights, senior staff reporter
Contact:
Arburg Inc., 860-667-6500, www.arburg.com
Boy Machines Inc., 610-363-9121, www.boymachines.com
Engel Machinery Inc., 717-764-6818, www.engelglobal.com
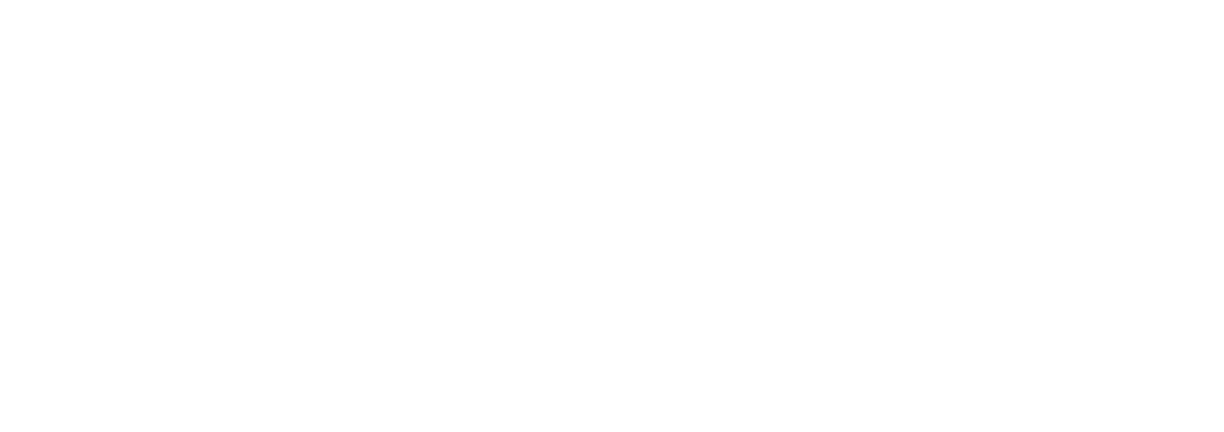