Two European suppliers of equipment to produce parts made from liquid silicone rubber (LSR) rolled out developments during the K show that focus on convenience and flexibility.
NEW SOURCE FOR TURNKEY LSR LINES
Nexus Automation GmbH, Eberstalzell, Austria, now offers turnkey manufacturing cells for processing LSR, including automation, tooling, controls, injection molding machines and dosing/metering equipment.
Nexus, a 10-year-old supplier of systems for injection molding thermoplastic elastomers (TPEs), designs many of the components it uses to assemble manufacturing cells for processing LSR and rubber, managing director Dietmar Waizenauer said. The LSR system can be configured for two- or three-component molding. The all-electric system is suitable for clean-room use.
The company's LSR systems offer precise dosing and the flexibility to install, adjust or remove fully integrated robotics, visual inspection systems and packaging equipment. They also produce little waste. Nexus has sold one system to a molder based in Europe.
Nexus has an arrangement with Fanuc Corp., Oshino, Japan, to incorporate its Roboshot alpha-SiA line of fully electric injection molding presses into its LSR systems. The Roboshot line comes standard with all axes electrically driven by four servomotors and CNC controls. Nexus LSR manufacturing cells are available with Roboshot machines with clamping forces from 15 tons to 385 tons.
Fanuc's CNC platform for the Robotshot machine is used to control all equipment in the molding cell. The control software was designed with input from Nexus.
Nexus integrates several of its own technologies into the system, including a precision injection unit, the tooling (available with two to 64 cavities and featuring a needle valve-gate system), its Servomix EcoPlus brand of volumetric mixing and dosing equipment, and its TrueFlow HP mix-regulation equipment. Nexus also offers its new Timeshot cold-runner regulation technology with the system, which helps to produce gate-free and flashless parts that do not require rework.
Nexus designed the mixing head, which features a static mixer that allows for quick material changes. Nexus also designs and supplies a belt conveyor for removal of finished products, and a packaging system.
A Fanuc six-axis robot can be incorporated into the system for loading/unloading operations or if insert molding or other value-added operations are needed, said Waizenauer. A vision system for part quality can be installed as well.
The Servomix EcoPlus dosing technology uses servo-driven delivery pumps to ensure pulsation-free, consistent material flow from the drums. The A and B components for LSR are each supplied in their own 5-gallon pail or 55-gallon drum; a mechanical device that secures each container prevents the materials from being inadvertently mixed up. The dosing equipment is offered in two models, the Servomix E20 EcoPlus for 5-gallon containers and the E200 EcoPlus model for 55-gallon containers.
The Servomix dosing unit features automatic drum venting with air detection. Automatic air venting minimizes operator intervention, Waizenauer said. Air present in the drum is vented in a controlled manner without stopping the system. The system also detects and purges any air trapped in the material that rises to the surface after a drum change, to ensure air-free material conveying and avoid lost production time. The drums are automatically vented during a drum change. (Nexus also incorporates an active ventilation function into the LSR tools it builds.)
The new pump technology incorporated into the Servomix, coupled with the servodrive unit and the controller, stabilizes the dosing process and ensures a consistent and precise mixing ratio of the two components, irrespective of high dosing volumes or small shot sizes.
When no material is required, the servomotor driving the feed pump transitions into standby mode, saving energy. System pressure is restored quickly when material is required. The Servomix system uses 70 percent less energy compared to competing systems, because it is idle when material is not required. It draws the A and B components from each drum simultaneously, emptying more than 99 percent of the material from the drums. Nexus guarantees that remaining material in the drums prior to changeover will be less than 0.8 percent of the container volume.
Optional equipment for use with Servomix includes the TrueFlow Nano unit for precise dosing of additives such as color. TrueFlow Nano eliminates complicated mechanical settings of the color valve. Instead, the operator enters the desired ratio of additive on a display screen and the system doses the additive volumetrically to the material. Operational data from TrueFlow Nano are combined with process data records. The system can be configured to deliver the additive feed using a pressure container, a paddle mixer or a plug-and-play, high-pressure delivery system. The mixing of the A and B components and additives is accurate to 0.005 percent, the company said. The system can handle shot weights as small as 0.08 gram.
LSR DOSING SYSTEM BRINGS EASIER ACCESS AND MORE CONTROL
Elmet Elastomere Produktions und Dienstleistungs GmbH, Oftering, Austria, launched Top 5000 P, its latest two-component dosing system for LSR injection molding. It features a quick-change drum design, a user-friendly touch-screen control and new software programs designed to eliminate any possibility of operator errors, said Daniel Schölmberger, technical sales and marketing manager at Elmet North America Inc., Lansing, Mich.
The system can dose as many as five components, including two large-volume components and three additives, each comprising up to 10 percent of the recipe. It is suitable for shot weights of 0.1 gram to several kilograms, and can work with materials that have significant differences in viscosities.
Top 5000 P is designed so that users can remove and replace an empty container from the front or side of the unit. That accessibility reduces the time required for changing the drums, provides additional flexibility when positioning the dosing unit in the production area and eases access for cleaning, maintenance and repairs.
The new model also features a smart control system that prevents the metering operations from being affected by pressure fluctuations at the switchover point of the piston pumps. The control also has step-by-step instructions for changing the drums, to minimize potential mishandling of the containers.
In addition, the control has a function for additives such as colorant. It monitors whether the additions were made correctly to ensure consistent dosing. The main control records all relevant processing parameters, and machine data can now be viewed remotely. An event log gives information regarding machine operation and parameter changes.
The system features two independent control circuits. Circuit 1 ensures synchronous emptying of the A and B components. The second circuit controls the volume of material fed into the process and ensures constant mixing, even when small parts are being molded. A patented volume-control system ensures the homogeneity of the molded part. It also incorporates a special extension module to ensure that the pump switchover time occurs outside the dosing phase, to maintain pulse-free material conveying.
The system also incorporates a new automatic drum ventilation function that makes vessel changes and cleanup easier, reducing the amount of manual work involved in changing the drums.
Mikell Knights, senior staff reporter
Contact:
Elmet North America Inc., 866-628-6499, www.elmet.com
Nexus Automation GmbH, 43 50-1215-200, www.nexusautomation.at
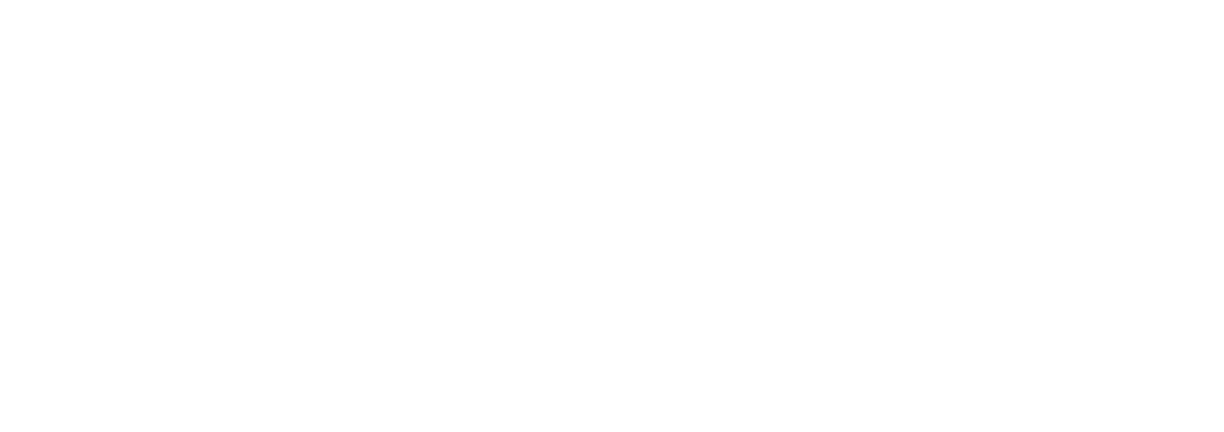