Uniloy, Milacron's blow molding brand based in Tecumseh, Mich., introduced the first model of its new M-Series, the third generation of its all-electric shuttle blow molding machines, at the K show. The entire series will be rolled out over the next 18 months, said David Skala, president of Uniloy Milacron.
The new series is interesting on several fronts.
First, it represents the fruits of a major soul-searching effort in which the company hired a market research firm to study customer needs. "Customers felt that Uniloy was a highly respected brand, but they were confused about our product lineup and raised some issues we needed to address," said Colin Taylor, VP of global sales at Uniloy.
One problem was that engineering groups based in Italy and Germany tended to create custom models for each customer and often did not coordinate their efforts. The result was a plethora of products. There were 84 shuttle models, for example, many that included a distinction without a meaningful difference — which led to issues in terms of technical and parts support.
That type of customization did not fit into the standardization and optimization strategy implemented 2 years ago by Milacron CEO Tom Goeke. The program aims to improve manufacturing efficiencies and is expected to yield approximately $35 million in savings per year by next year.
Skala brought Massimo Davoli on board to recommend a solution.
A mechanical engineering graduate of the University of Bologna in Italy, Davoli became a global product manager at Uniloy in 2014 as well as doubling as GM in Europe last year.
"It was clear we had to create one family of shuttle machines because there were so many overlapping models," Davoli said. "We had hydraulic and electric models engineered in Germany and hydraulic and electric models engineered in Italy."
He told the engineering groups to collaborate around three key goals:
• Improve the speed compared to currently available models;
• Improve reliability and extend each machine's usable life; and
• Standardize components to the greatest extent possible, including potentially using products already developed elsewhere in Milacron.
For example, using the tablet-like machine control developed by CTO Bruce Catoen's group was a no-brainer. It was like going from an early-generation microprocessor to an iPad.
Users can choose from six clamping forces, six shuttle types and three calibration forces. That still allows a multitude of combinations, but all the components are standard — a huge advantage for technical service and parts support. And conforming to a trend in blow molding — particularly in Europe and Asia — the machine is all-electric. Demand for all-electric machines is lower in the U.S., where energy costs less, but even in the U.S. the trend to all-electrics is gaining momentum.
The new model has a dry cycle time of 2.8 seconds, compared to 3.5 seconds in the previous model of the same size.
A M20.75 ED model machine produced 32-ounce bottles in Milacron's booth at the K show. The 1.7-ounce part made in on a five-cavity tool at the show ran in a 13-second cycle time.
The new machine model is ideal for producing bottles, containers and technical parts from 3.4 fluid ounces up to 5.3 gallons. That range goes from tiny cosmetic containers to large industrial packaging. Skala said the machine can run virtually all commercial resins.
Milacron is manufacturing the new machine at its new factory in PoliÄka, Czech Republic, where injection molding machines also will be made. Later, the machine also will be made in Milacron's plants in Cincinnati, India and China.
Historical sales and manufacturing inefficiencies at Milacron reflect the way the company grew through acquisitions. Extrusion blow molding is a good example.
Uniloy began as a division of Hoover Ball & Bearing, where it patented a hollow-handle plastic bottle design for dairy products. Over the years, several other groups were added, including Barr Polymer Systems, Rainville injection blow molding machinery, two shuttle machinery manufacturers — Comec of Italy and B&W of Germany — Moretti Industrial Machines and Plastics USA.
Most recently, Milacron acquired Uniloy in 1998. In the past few years, Milacron has combined the manufacture and assembly of its blow molding machines from locations in Italy, Germany and Czech Republic into a $16 million facility in PoliÄka — bringing state-of-the-art manufacturing, design and process technologies.
The push for a unified global approach at Uniloy began three years ago when Skala was brought in to run the group. In the first wave, the sales team was reorganized. In the new setup, they were no longer organized by manufacturing group. Instead, they represented the entire product line for an assigned geographic area.
"The team features solid industry professionals with a commitment to making sure that the customer is sold the right technology for the application," Skala said.
In terms of future developments, Skala looks to take advantage of co-injection and high-speed HDPE applications, given the technologies available at Milacron.
Doug Smock, senior correspondent
Contact:
Milacron Uniloy, 517-424-8900, www.milacron.com
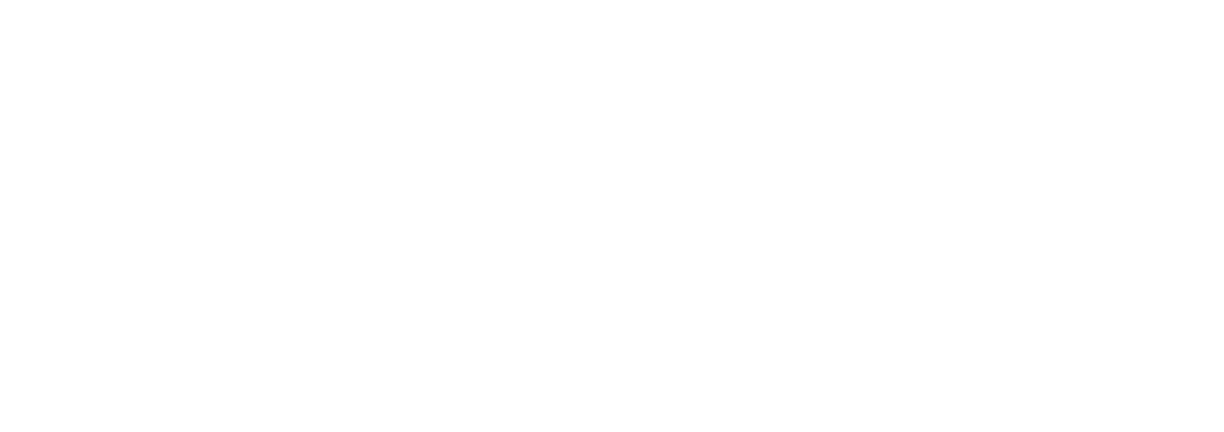