By Doug Smock
A new vacuum-assisted pelletizer from Bay Plastics Machinery Co., Bay City, Mich., significantly reduces fines, resulting in improved pellet yields, according to the company. The invention takes aim at overcoming two problems, said Dick Fetter, VP of technology at Bay Plastics. One is the tendency of pellets to stick in the cutting chamber because of static. Also, pellets get stuck in the rotor. Both result in "carryover." As pellets move through the cutting chamber a second time, they are re-cut, generating fines or odd-shaped pellets that can negatively affect uniform melting during processing. A customer running an expensive plastic was experiencing yields of only 50 percent because of pellet carryover in a pelletizer and asked Bay Plastics for help. "It was not unique, but it was a blatant case and it was a material that was very expensive," Fetter said. "To help them, we came up with a specially designed discharge chute that acts like a vacuum nozzle right below the cut point between the rotor and the bed knife. It's like taking a vacuum cleaner and sticking it right where the pellets are coming off the rotor." The system requires an inlet for air in the cutting chamber. In one variation, the machine may also include static elimination bars. "It depends on the plastic," Fetter said. "Polycarbonate, for example, generates a lot of static. We're still testing different plastics to develop data." One target market will be micro pellets, which experience extreme problems with the generation of fines. Pellet yield at the customer's facility with the carryover problems is now better than 99 percent with the new vacuum-assisted pelletizer, Fetter said. The new pelletizer is now available for sale. Patent Application 20160288132; published Oct. 6 In other patent news: Blow molding. Alpla Werke Alwin Lehner Gmbh & Co. KG of Hard, Austria, patented a process it said provides dimensional accuracy of a spout in a container produced with extrusion blow molding. An extruded plastic hose is inserted into a cavity of a blow mold and then inflated by a calibrating blow pin, according to the patent. The calibrating blow pin defines the neck of the plastic container. Patent 9,517,601; Dec. 13 Resin transfer molding. Toray Industries Inc., Tokyo, has developed a process designed to eliminate air traps by using a completely closed mold. Part of the technology includes use of suction to create a resin path through a preform. Patent Application 20160339648; Nov. 24 Valve pin control. A new technology from Synventive Molding Solutions Inc., Peabody, Mass., controls valve-pin movement based on cavity sensor feedback. The rate of flow through each individual nozzle is made uniform and matches flow profiles from a test injection cycle, according to the patent application. Patent Application 20160346980; Dec. 1 Co-injection. Milacron LLC, Cincinnati, disclosed a process for creating structural inner layers of molded containers that may be made without an adhesive. According to the patent, cohesion can be created between layers by the method in which plastic is injected, specifically through thickness variation. The volumetric flow ratio may be adjusted several times. Patent 9,511,526; Dec. 6 Patents and patent applications can be viewed at www.uspto.gov.Have you applied for or received a patent? Contact [email protected]
A new vacuum-assisted pelletizer from Bay Plastics Machinery Co., Bay City, Mich., significantly reduces fines, resulting in improved pellet yields, according to the company. The invention takes aim at overcoming two problems, said Dick Fetter, VP of technology at Bay Plastics. One is the tendency of pellets to stick in the cutting chamber because of static. Also, pellets get stuck in the rotor. Both result in "carryover." As pellets move through the cutting chamber a second time, they are re-cut, generating fines or odd-shaped pellets that can negatively affect uniform melting during processing. A customer running an expensive plastic was experiencing yields of only 50 percent because of pellet carryover in a pelletizer and asked Bay Plastics for help. "It was not unique, but it was a blatant case and it was a material that was very expensive," Fetter said. "To help them, we came up with a specially designed discharge chute that acts like a vacuum nozzle right below the cut point between the rotor and the bed knife. It's like taking a vacuum cleaner and sticking it right where the pellets are coming off the rotor." The system requires an inlet for air in the cutting chamber. In one variation, the machine may also include static elimination bars. "It depends on the plastic," Fetter said. "Polycarbonate, for example, generates a lot of static. We're still testing different plastics to develop data." One target market will be micro pellets, which experience extreme problems with the generation of fines. Pellet yield at the customer's facility with the carryover problems is now better than 99 percent with the new vacuum-assisted pelletizer, Fetter said. The new pelletizer is now available for sale. Patent Application 20160288132; published Oct. 6 In other patent news: Blow molding. Alpla Werke Alwin Lehner Gmbh & Co. KG of Hard, Austria, patented a process it said provides dimensional accuracy of a spout in a container produced with extrusion blow molding. An extruded plastic hose is inserted into a cavity of a blow mold and then inflated by a calibrating blow pin, according to the patent. The calibrating blow pin defines the neck of the plastic container. Patent 9,517,601; Dec. 13 Resin transfer molding. Toray Industries Inc., Tokyo, has developed a process designed to eliminate air traps by using a completely closed mold. Part of the technology includes use of suction to create a resin path through a preform. Patent Application 20160339648; Nov. 24 Valve pin control. A new technology from Synventive Molding Solutions Inc., Peabody, Mass., controls valve-pin movement based on cavity sensor feedback. The rate of flow through each individual nozzle is made uniform and matches flow profiles from a test injection cycle, according to the patent application. Patent Application 20160346980; Dec. 1 Co-injection. Milacron LLC, Cincinnati, disclosed a process for creating structural inner layers of molded containers that may be made without an adhesive. According to the patent, cohesion can be created between layers by the method in which plastic is injected, specifically through thickness variation. The volumetric flow ratio may be adjusted several times. Patent 9,511,526; Dec. 6 Patents and patent applications can be viewed at www.uspto.gov.Have you applied for or received a patent? Contact [email protected]
June 24, 2025
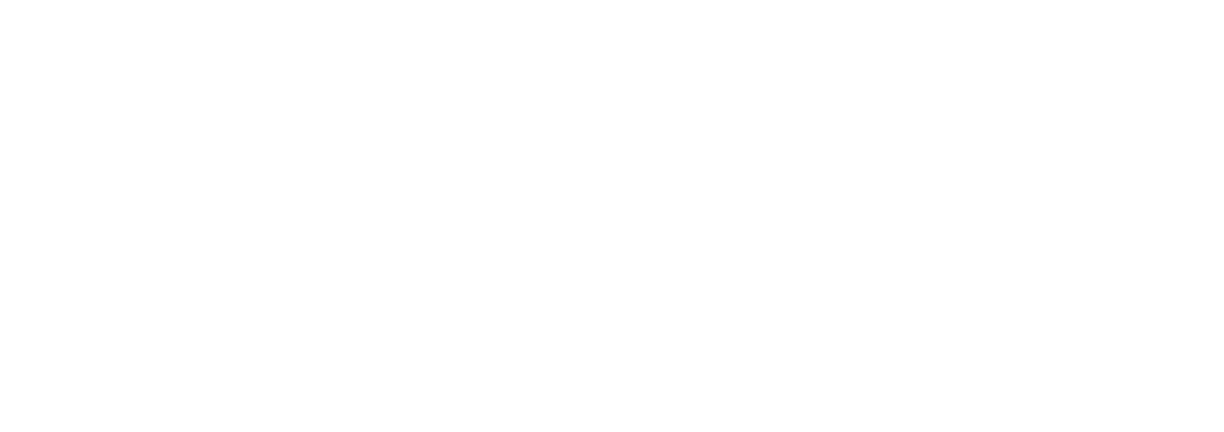