At the K show, Ettlinger Kunststoffmaschinen GmbH of Königsbrunn, Germany, announced it will introduce its unique, and often giant, injection molding machines to the U.S. market.
The company is best known in the U.S. for its melt filtration technology, including the ERF series designed for processing heavily contaminated plastics, and the ECO melt filter, which was developed for filtering PET and PE.
GM Volker Neuber discussed the company's plans with Plastics Machinery Magazine senior correspondent Doug Smock.
Could you give us some background on Ettlinger?
Neuber: Ettlinger was founded in 1983 by Roderich Ettlinger, a mechanical engineer, to meet a demand for customized injection molding machinery and specialty equipment for the plastics industry. In 2004, he launched a patented melt filter system. In 2010, I bought into the company and assumed responsibility for operations with Roderich's son, Thorsten. We established a North American subsidiary, headed by Mike Diletti, in the Atlanta area three years ago.
The company is best known in North America for the melt filtration business. Describe your approach and technology for injection molding machinery.
Neuber: Our machines are designed to mold large, heavy and thick-wall parts. Clamping forces go up to 3,000 tons, although we have also made machines with as little as 200 tons of clamping force. What's unique in our approach is the injection unit. For large shot volumes, conventional injection molding machines would need two or even three injection units to do what we can do. We can have a very small extruder to plasticize the material, leveraging the cooling time of the part and then transfer the material into a large shooting pot to take all the volume of the material needed to make the part. Our injection molding machines can handle virgin as well as recycled material or mixed plastics very efficiently. We have realized projects with parts weighing up to 250 pounds. About 60 percent of our injection molding machinery is standard and the rest is custom.
How energy efficient are your machines?
Neuber: Our injection molding machines have higher shot volumes than conventional systems, but use significantly less clamping force. A typical shot size is 6,763 ounces. As a result of our two-step approach using small extruders, the machines have smaller drives and consume as much as 60 percent less energy than competitive machinery. In addition to fully hydraulic machines, we can also supply hybrid models with an electric-drive plasticizing unit.
At your K show stand, there was no injection molding machine, but Ettlinger did have a large pipe fitting. Could you describe the fittings market for your equipment?
Neuber: Our machines mold polyethylene and polypropylene pipe fittings ranging from relatively thin-walled versions with small diameters to larger types with walls up to 2.4 inches thick and weighing more than 220 pounds. One unique aspect of our machines is that they have a large opening space with no tie bars in the way once the clamp is open, allowing optimal accessibility from the side. As a result, these big parts can be removed more easily, and for that matter, the mold can also be changed much easier and faster.
What are some examples of the customized machines?
Neuber: One is the machine for road safety bumps molded from soft, high-density PVC obtained from recycled cables. We can equip machines with a rotary table to keep production moving while these very thick-walled parts cool. Cycle times can be more than half an hour. Four different parts with differing weights can be molded at the same time.
We also make a customized machine for overmolding pipes used in underwater [ocean] applications. The weld zone is overmolded with plastic sheathing using our Ettlinger injection unit, which has a very compact design due to space limitations on the ship where the process takes place. In addition, the electrical and hydraulic power supply components must be encapsulated to protect the pipes from seawater and the salty atmosphere. The pipe diameters are up to 3.3 feet. The shot volume required to completely overmold the weld can be as much as 4,744 ounces.
What are other target markets?
Neuber: We target other parts with high shot weights, such as pallets made from 100 percent recycled plastic to very complex, returnable types made from virgin material — the type typically used by the chemical and beverage industries. We can mold even complex pallets with a low clamping force.
Meanwhile, larger manholes are being used in the water-management industry, meaning part sizes are growing. I'm talking about manholes almost 3.3 feet in diameter. Manhole systems may have a height of more than 20 feet and consist of an entrance cone, shaft ring and shaft bottom with port openings for the pipes. We have designed a special machine frame for holding and positioning core pullers, and that works very well for this kind of application.
What's the price range for your machines?
Neuber: They go from $250,000 to $2.5 million. The high end is a machine that makes manhole covers.
Why is now a good time to reintroduce your injection molding machines to the U.S.?
Neuber: We used to sell injection molding machines in the United States in the past, but our melt filtration business became so successful that we did not have the manufacturing capacity to also make injection molding machines to sell there. Recently, we have doubled our manufacturing capacity to accommodate building more machines each year.
Are you a fully integrated machine manufacturer?
Neuber: We do all the engineering and assembly at our plant in Königsbrunn but purchase up to 90 percent of the components. With the added capacity in engineering, technical personnel and assembly space, we will be well prepared to serve the American market. Ettlinger North America … will be the key contact for our U.S. customers. We have been building a successful business for our melt filters and will now start to do the same with our injection molding machines.
What's the biggest challenge you face?
Neuber: We are located in Bavaria near several major companies such as BMW and Siemens, and our
biggest problem is competing for engineering talent.
Is there any synergy between your injection molding manufacturing and your melt filtration business?
Neuber: We have one customer in Europe that is making parts from post-consumer plastics and they run an Ettlinger injection molding machine with an integrated melt filter between the extruder and the injection unit.
Doug Smock, senior correspondent
Contact:
Ettlinger North America LP, 770-703-8541, www.ettlinger.com
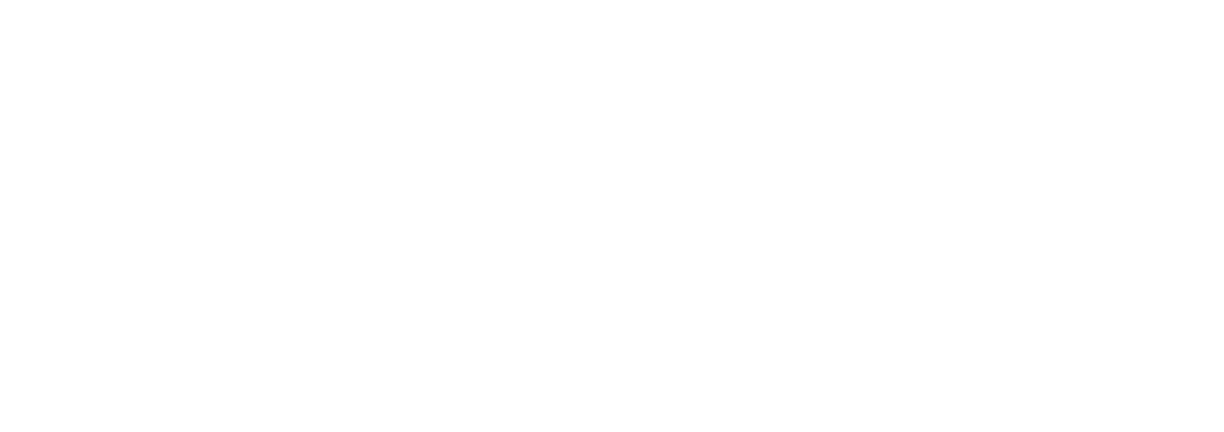