German manufacturers used the K show to vigorously promote Industry 4.0 as a way to improve productivity, process quality, data interchange and flexibility.
A walk through the 19 halls of the sprawling triennial show indicated that there are almost as many approaches as there were companies exhibiting "smart" technology.
Some companies emphasized the ability to identify maintenance requirements more quickly and even automatically deliver required spare parts to a customer's plant in time for the work. Others said Industry 4.0 is the ability to network not only equipment inside a plant, but with customers' factories around the world. Still others said it was the ability to increase customization of manufactured products.
Industry 4.0 was summed up this way by Christian Hopmann, who oversees the IKV Institute of Plastics Processing at the RWTH University of North Rhine Westphalia, Aachen: "There is a trend toward increased variability in manufacturing, and Industry 4.0 provides the flexibility that will allow this to happen on a broad scale while keeping the cost advantages of mass production. One result of improved efficiency of German companies could be the return of manufacturing that had moved to lower-cost countries."
Companies from the U.S., Japan, Italy and other countries also touted enhanced Industry 4.0 capabilities, not only for primary machinery, but for auxiliary and ancillary equipment.
But the Germans embraced the concept collectively — not only as a marketing strategy, but as a means to build a competitive technical advantage on a global scale. The concept of Industry 4.0 was launched by the German government 10 years ago and broadly defined as the next generation of the digitization of manufacturing.
The concept of applying digital capabilities to plastics manufacturing is not new, in Germany or elsewhere. For example, the late Denes Hunkar of Cincinnati-based Hunkar Laboratories invented closed-loop process control in 1970 and was a pioneer in computer-integrated manufacturing in the 1980s.
But it was clear at the K show that the German machinery manufacturers, acting through the leadership of their trade group, VDMA, and its managing director, Thorsten Kühmann, want to be pioneers in the next era of advancements.
In one VDMA-led demonstration at the show, equipment from seven manufacturers was integrated into a single control system based on the newly developed communications protocol, Euromap 77. The live demonstration at the show included technologies from:
• Arburg GmbH + Co. KG (Lossburg, Germany);
• Engel Austria GmbH (Schwertberg);
• KraussMaffei Technologies GmbH (Munich);
• Kurtz GmbH (Kreuzwertheim, Germany);
• Netstal-Machinery Ltd. (Näfels, Switzerland);
• Sumitomo Demag Plastics Machinery GmbH (Schwaig, Germany); and
• Wittmann Battenfeld GmbH (Kottingbrunn, Austria).
One VDMA official said it was "just a baby step," but it did show the willingness of machine builders to cooperate on a common platform.
Euromap 77 will allow incorporation of multicomponent and rotary-table machines. Future Euromap standards will target Open Platform Communications-Unified Architecture (OPC-UA) communications protocols for auxiliary and peripheral equipment. "Industry 4.0 will only work if companies work together on standards," Kühmann said. "And the standards must be accessible to everyone. We are just at the beginning of this." The Euromap 77 standard was published as a Release Candidate at www.euromap.org/euromap77.
The Euromap 77 standard is based on OPC-UA, which was developed by OPC Foundation, a Scottsdale, Ariz.-based organization that represents companies interested in collaborating on standards. The new OPC-UA protocol is the successor to OPC. Many new controls around the world will be based on OPC-UA 1.02, including those being introduced next year by Nissei ASB Machine Co. Ltd., Nagano, Japan.
"In tomorrow's smart factory, all machines, equipment and systems form a huge plant network; OPC-UA enables the seamless communication between the devices," said Michael Wittmann, GM of Wittmann Battenfeld. "Today's integrated production cells are based on point-to-point communication and therefore require numerous interfaces and protocols."
CONCEPT IN ACTION
The Industry 4.0 concept spanned processes and equipment types at the K show.
In extrusion, Windmöller & Hölscher (W&H) KG, Lengerich, Germany, showed rolls of film embedded with codes containing production data and information about mechanical properties and separating force. That type of traceability is critical to the medical industry and was a common topic in several companies' discussions of Industry 4.0. The film was produced on a newly introduced Filmex II cast film line.
In a demonstration that was part of what W&H called Packaging 4.0, a five-layer Varex II blown film line ran an automation module for quick resin purging and changes.
Auxiliary equipment supplier Motan-Colortronic GmbH, Friedrichsdorf, Germany, demonstrated networked production systems in live simulations of Industry 4.0. Operation and status data were exchanged between Motan's resin-distribution systems and primary machinery; the data were then analyzed by the control, which initiated appropriate actions.
In one example, material-distribution and processing machines started in a coordinated way to optimize energy. According to the company, the current practice has been to use weekly timers to switch on the dryers and processing machines. Independent of each other, the systems turn on before production starts, which wastes energy.
In the Motan-Colortronic system, each processing machine and appropriate dryer are linked to each other, based on production requirements. In another example, drying temperatures and air flows were adjusted to avoid over-drying during downtimes. The demonstrations were conducted in the KraussMaffei booth.
Motan's CONTROLnet architecture is based on the OPC-UA interface, allowing communication with primary machinery independent of manufacturer or platform.
Auxiliary equipment supplier Piovan SpA, Santa Maria di Sala, Italy, introduced Winfactory 4.0, described as "a supervisory software for the smart factory." Also based on OPC-UA, it allows Piovan equipment to communicate with each other and with primary machinery using the same communications protocol. As with other Industry 4.0 controls, it does not need an interface to "translate" the data. The platform can be accessed by tablets and smart phones. The system includes energy meters that help identify ways to reduce energy use for a variety of equipment. Piovan is represented in the U.S. by subsidiary Universal Dynamics Inc., Woodbridge, Va.
Doug Smock, senior correspondent
Contact:
Arburg Inc., 860-667-6500, www.arburg.com
Beckhoff Automation LLC,952-890-0000, www.beckhoff.com
KraussMaffei Corp., 859-283-0200, www.kraussmaffeigroup.us
Kuka Robotics Corp., 866-873-5852, www.kuka-robotics.com
Motan Inc., 269-685-1050, www.motan-colortronic.com
Next Generation Recycling Machines Inc.678-720-9861, www.ngr.at
Universal Dynamics Inc., 703-490-7000, www.unadyn.com
VDMA,49-69-66030, www.vdma.org
Windmoeller & Hoelscher Corp., 401-333-2770, www.whcorp.com
Wittmann Battenfeld Inc., 860-496-9603, www.wittmann-group.com
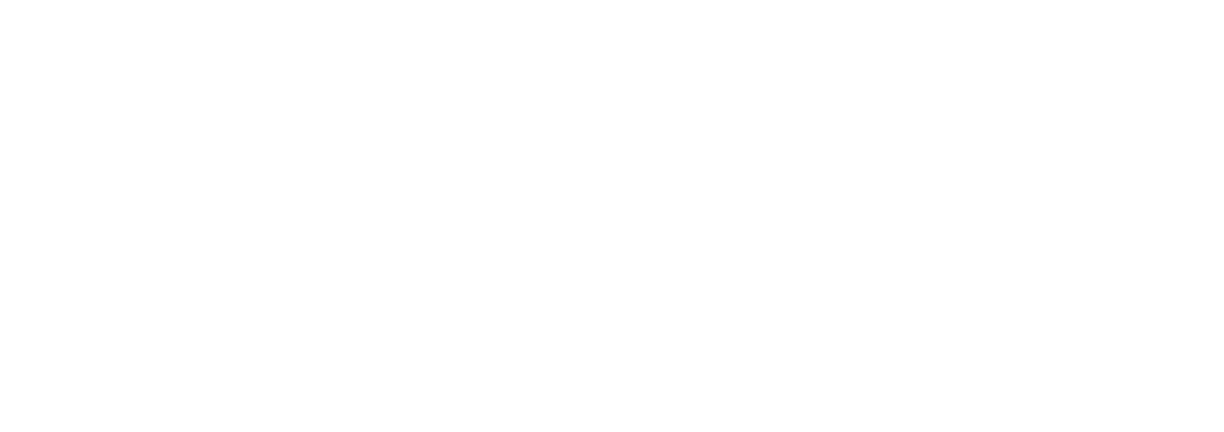