Several American companies presented smart factory innovations at the K show.
Maguire Products Inc., Aston, Pa., showed a controller with beefed-up data-processing capabilities for its gravimetric blenders, "substantially enhancing communications with other devices in an Industry 4.0 setting and offering centralized control of both blending and loading," the company said in a press release.
The new 4088 controller is seven times faster than the firm's 1212 controller and has eight times the memory. The controller receives data reports from the load cells — which are used to weigh batch ingredients — 45 times more frequently, resulting in greater accuracy. "While the batch accuracy of the Maguire blender will continue to be rated at the exceedingly small range of plus or minus 0.1 percent, the vastly enhanced operation of the new 4088 controller will increase the volume, speed and reliability of data transfer," said Frank Kavanagh, VP of sales. "This means that valuable information on the makeup and consumption of the raw materials being metered into the molding or extrusion process can be readily shared with third-party devices via any standard communication protocol, making it possible to integrate Maguire blenders with today's most advanced technologies."
Milacron LLC, Batavia, Ohio, exhibited its SmartMold module, which it described as "the result of a multiyear development to make injection molding machine cells truly 'smart.' " It reports data via the internet or a local area network (LAN). CTO Bruce Catoen said the system provides improved equipment communication and metrics that result in higher quality parts. SmartMold also allows scheduling of regular and preventive maintenance. Milacron demonstrated it on its MPET 300 machine producing PET preforms with a co-injected barrier layer. The machine featured a Mold-Masters Summit valve-gate display system and Mold-Masters' new M-AX six servo-axis controller.
High-Technology Corp., Hackensack, N.J., introduced the first continuous screen changer in 1969. VP Alina Alroy said during an interview at the K show that the company now offers a "smart" automated filtration function that is a fully integrated element in the extrusion process. The controls provide continuous feedback on operating conditions. They allow for automatic setting and calibration of key parameters — including screen travel, timers, pressure, temperature and operational limits — based on the polymer melt temperature and available coolant temperature and flow rate via touch-screen selection.
RJG Inc., Traverse City, Mich., demonstrated The Hub, a remote machine monitoring system that allows injection molders to monitor the entire plant floor from a single remote access point on a web browser. This system will allow customers to access the data being produced by RJG's eDART process monitoring and control system. Plant and operations managers can know what presses have gone down, the jobs that are running and how many bad parts might have been produced and why.
"Plant managers no longer need to spend their time and energy continuously walking the plant floor," said Dale Westerman, president of RJG. "They are able to instantly know how all of their machines are performing and quickly prioritize specific processes that need attention."
This product will be available from RJG on a limited release in the first quarter and its official release is yet to be determined.
Doug Smock, senior correspondent
Contact:
High-Technology Corp., 201-488-0010, www.screenchanger.com
Maguire Products Inc., 610-459-4300, www.maguire.com
Milacron LLC, 513-536-2000, www.milacron.com
RJG Inc., 231-947-3111, www.rjginc.com
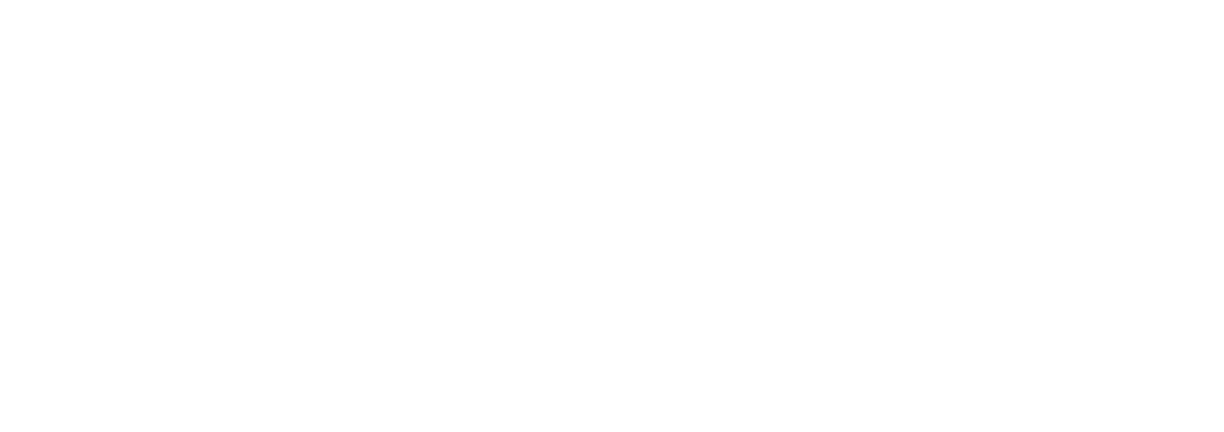