Faster cycles, increased precision and greater energy efficiency were major themes for suppliers of multidrive injection molding machines at the K show. Molders have a greater choice of servo-hydraulic and hybrid styles due to new equipment lines, sizes and capabilities. Many of the machine developments target high-speed packaging applications.
NETSTAL ADDS ADVANCED ELIOS MODEL
Netstal Maschinen AG, Näfels, Switzerland, unveiled its new Elios series injection press, developed specifically for applications involving lightweight technical components and the high-speed production of thin-walled packaging. Netstal, represented in the U.S. by KraussMaffei Corp., Florence, Ky., will offer the Elios line with clamping forces from 495 tons to 825 tons.
An Elios 7500-4200 with 825 tons of clamping force was unveiled at the K show. In addition, Netstal offers its Elios 6500 model, with 715 tons of clamping force. This year, it will roll out models that provide clamping forces of 495 tons and 605 tons, said Markus Dal Pian, VP of sales and marketing.
On the Elios machines, Netstal has incorporated a newly developed and patented five-point dual-toggle clamp that delivers precise platen movements and dry cycle times as short as 1.9 seconds.
A hybrid drive technology that combines a patented servo-electric drive and a double-toothed, hydromechanical rack actuates the toggle clamp. The clamp builds up force rapidly to deliver fast movements, said Adrian Angst, Netstal's head of research and development.
The centrally aligned toggle lever directs clamp forces to the center of the mold and distributes them uniformly, minimizing deformation of the mold plates. The clamp has an opening stroke of 1,000mm and tie-bar spacing of 1,050mm by 1,050mm.
The Elios machines electrically charge the screws. The line has two parallel-aligned synchronized hydraulic cylinders controlled with two dynamic servo valves, offering injection speeds of almost 87 inches per second. Molders can choose from 33 combinations of clamping unit, injection unit and screw diameter.
At the K show, an Elios 7500-4200 produced 2.8-gram PP domed lids in a 24+24 stack mold in a cycle time of 3.9 seconds.
NEW ENGEL DRIVE UPDATES E-SPEED LINE
Engel Austria GmbH, Schwertberg, improved the performance of its e-speed hybrid molding machines for thin-wall packaging applications by upgrading the hydraulic system.
The upgrades to the line, which was first shown at K 2013, include the replacement of its hydraulic accumulator assist with ecodrive servo-hydraulic technology, designed to improve energy efficiency. With ecodrive, the pump operates only when needed. The technology launched on other Engel machines in 2008, but is now standard on the e-speed line, which is offered in models with clamping forces of 550 tons and 720 tons.
In addition, Engel has improved the energy efficiency of the e-speed with a system that stores the braking energy of the platen movement and transfers it back to the servo motor as needed. This energy-storage concept allows molders to avoid peak loads while operating at high speeds, even with high clamping forces. The e-speed line can thus operate with a relatively low but constant connected load. The upgrades result in greater precision and energy efficiency.
Engel also achieved faster and more precise injection by optimizing other aspects of the hydraulic system for faster acceleration/deceleration, and by redesigning the layout of the nozzles to make them more accessible.
At Engel's K show booth, the upgraded e-speed was the center of a unique molding cell designed to produce thin-walled packaging with an in-mold label (IML) at high speeds. An Engel e-speed 500 model with a 90mm-diameter screw produced cartridge tubes for the construction industry featuring a long, hollow body and wall thickness of 1.2mm in a 16-cavity mold. Engel says the application marks the first time it has combined its high-speed packaging machine with IML automation in the production of very large thin-walled tubular cartridges. Beck Automation, Oberengstringen, Switzerland, created the IML automation.
HPM EXTENDS ITS PACKAGING SERIES WITH NEW MODEL
Guangdong Yizumi Precision Machinery Co. Ltd., Foshan, China, upgraded its PAC-K machines and added a new model to the line of high-speed packaging presses developed for molding fast-food containers. The company is represented in the U.S. by its subsidiary, HPM North America Corp., Marion, Ohio.
The PAC-K series offers higher performance than Yizumi's PAC line, which is designed for general thin-walled products, said Jack Yu, technical service manager at the company's global business development center. The PAC-K line has been enhanced with an upgraded electric motor and pump system, while the mechanical design of the toggle and the design of the platen have been optimized to accommodate larger molds, Yu said. The control system has been upgraded for increased responsiveness, and the model can perform at faster injection speeds.
The new PAC450K has a clamping force of 495 tons. Features of the new model include an opening stroke of 700mm, tie-bar spacing of 720mm by 720mm and maximum daylight of 1,450mm. The unit is offered with screw diameters of 55mm or 60 mm that can handle shot weights up to 486 grams or 579 grams, respectively.
Yizumi's PAC350K has a clamping force of 385 tons, while the PAC250K has a clamping force of 275 tons. At the K show, Guangdong used the PAC450K to produce a thin-walled container from PP with a 5-micron-thick label in an eight-cavity mold in 7.2 seconds.
BOY MULTIPLIES DRIVES TO BROADEN MACHINE OPERATIONS
Dr. Boy GmbH & Co. KG, Neustadt-Fernthal, Germany, introduced Multi-Drive, a patent-pending option for its line of injection machines designed to boost machine flexibility and capability by permitting the overlap or execution of multiple operating functions.
The Multi-Drive concept incorporates two servo-driven hydraulic motor pumps that can be programmed to operate independently or in parallel to each other. Depending on the application, the servo pumps can be adjusted for simultaneous movements and functions in an injection molding cycle, said Alfred Schiffer, managing partner at Dr. Boy.
The interplay of both hydraulic drive units can replicate the functionality, precision and speed of an all-electric injection molding machine, yet also deliver the power of a hydraulic drive. Users can, for instance, operate the injection step in parallel with clamping force control, which would be difficult to do with a fully hydraulic unit. The Multi-Drive option also allows for the molding of a part requiring a long injection stroke and stamping.
At the show, Dr. Boy demonstrated the capability of the Multi-Drive option on a 110-ton Boy 100 E, which produced screw-on caps for water bottles in a 24-cavity mold. Schiffer said the Boy 100 E's large clearances allow it to accommodate large-volume molds.
CHEN HSONG MODEL OFFERS FAST INJECTION SPEEDS
Chen Hsong Group, Hong Kong, which is represented in the U.S. through a partnership with Gluco Inc., Jenison, Mich., launched Speed 168, its new servo hydraulic press for high-speed molding of thin-walled packages. The new high-speed toggle-clamp model is based on Chen Hsong's MK6 line of small to medium-sized injection machines, said H.L.A. Corbey, GM for Chen Hsong Europe BV, Ulft, Netherlands.
The unit is capable of injection speeds of up to about 12 inches per second and maximum opening and closing speeds of up to about 20 inches per second. The model is designed with a smaller A-type screw-and-barrel unit that lets a machine operate at a higher injection pressure while maintaining good plasticizing and mixing properties.
Other features include the incorporation of linear rails and dual-balanced injection carriage cylinders for friction-free, precise injection molding control. A precision servo drive system ties into the hydraulics on the press to deliver energy savings, as well as power when needed.
Chen Hsong optimized the design of the toggle clamp to match the rapid motion of the injection unit. In addition, the steel platens used on the machine have been optimized to ensure the lowest amount of platen deformation. Molders using the new press have an opportunity to reduce their clamp tonnage requirements without sacrificing part quality.
The unit uses a controller from Beckhoff Automation, Savage, Minn., to control all machine operations.
The new injection molding machine can achieve dry cycle times as fast as 1.5 seconds, Corbey said.
At the K show, the Speed 168, with a clamping force of 185 tons, produced a disposable PP cup in a two-cavity mold approximately every 3 seconds. In addition to thin-walled packaging, it can be used to produce precision electronic or medical parts.
HUSKY HYLECTRIC IMPROVED
Husky Injection Molding Systems Ltd., Bolton, Ontario, upgraded key features of its Hylectric 4.0 line of machines for increased connectivity and data collection, enhanced energy management and machine control, and improved operator experience.
The model line, offered in clamping sizes from 170 to 1,300 tons, combines an electric screw drive for plasticizing with the speed and pressure of hydraulic injection. The Hylectric 4.0 model features an updated electric drive and accumulators, which are designed to share the power from the hydraulic power pack among all of its axes. The updates have allowed a significant reduction in the size of the hydraulic power pack, Husky said.
The Hylectric 4.0 model uses Husky's Shotscope process monitoring and analysis software. The Shotscope-enabled unit enhances machine connectivity to the molding plant to help control and improve production processes, according to Husky.
The model enhances features and configurations seen in prior generations of the machine, such as its Reflex platens for optimal platen parallelism, use of a hydromechanical clamp design, a mold-protection system that extends tooling life, and Windows-based Polaris control.
Mikell Knights, senior correspondent
Contact:
Boy Machines Inc., 610-363-9121, www.boymachines.com
Engel Machinery Inc., 717-764-6818, www.engelglobal.com
Gluco Inc., 616-457-1212, www.gluco.com
HPM North America Corp., 740-382-5600, www.hpmmachinery.com
Husky Injection Molding Systems Ltd., 905-951-5000, www.husky.ca
KraussMaffei Corp., 859-283-0200, www.netstal.com
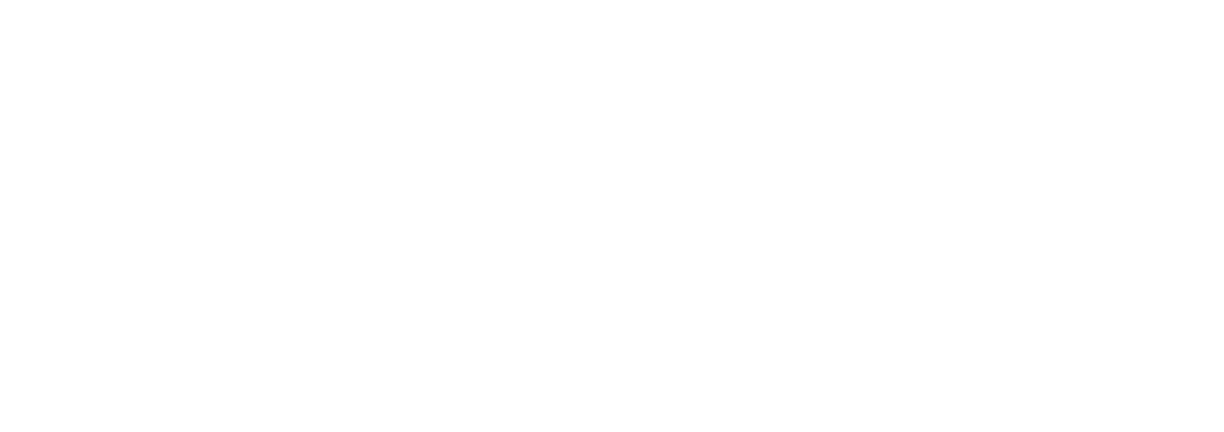