Thermoforming machinery manufacturer Thermoforming Systems LLC (TSL) of Union Gap, Wash., and its mold-making partner, Future Mold Corp., are expanding to meet increased demand.
Future Mold, Farwell, Mich., is adding 7,000 square feet to its 36,000-square-foot headquarters to make room for a TSL Low Flex 3.0 thermoforming system. It will be available as a prototyping machine, to be used by its thermoforming customers as they test molds and develop products. The Low Flex 3.0 will be part of a complete production line, including a roll stand, trim press and grinder. Future Mold plans to complete the expansion by mid-2017.
TSL is expanding its own facility by about 20,000 square feet, with a completion goal of March 1. The move will give TSL 50 percent more production capability to meet growing demand for its equipment, said Roger Moore, TSL senior VP of sales. Installing the prototyping machine at Future Mold will help the company to expand beyond the Pacific Northwest, closer to potential customers in the Midwest.
The technological key to the Low Flex 3.0 that will be installed at Future Mold's facility is its ability to incorporate many elements of large-scale production on a small scale, Moore said.
"The whole key to this machine is that it has all the same features … as we use in our big production lines that we have at the top 20 thermoformers," Moore said. "Right now, there's no other prototype machine out there that I know of that can replicate the processes that these big machines have. So the whole idea of having a small machine with all the same features that we have on our big machines is so you can develop a process or develop a new tool, and have valid data that you can take and then plug right into a full-production machine."
Moore said the Low Flex 3.0 can also be used as a small-production machine, but the company is marketing it as a prototyping machine within the North American market. TSL is targeting its machines at the top 20 thermoformers in the U.S., which produce nearly 7 billion pounds a year of food packaging.
"There's not a lab machine or an R&D machine that's out there right now that can produce that part with the same features that the guys are with the production machine," Moore said. PP cups for McDonald's or Starbucks can be as deep as 9 inches, and creating production-level features requires machine options such as servo-driven plug assists.
The Low Flex thermoformers come in five models, with forming areas ranging from 33.5 by 52 inches to 65 by 67 inches. They are suited for a range of plastics including HDPE, PET, PVC and ABS, and can run as roll-fed units or inline with an extruder. The prototype machine will run molds up to 33 inches wide, Moore said.
The new machine will provide options for Future Mold as well. "It will give us the opportunity to do development work, such as developing new products for customers," said Mike Otto, Future Mold VP. Future Mold makes molds exclusively for thermoforming and has more than 30 CNC machines. "So we have full control of what we're doing, from quality to the timing of it," Otto said.
The machine will be ready to produce when it's installed at Future Mold. "The machine will be up to speed," said Dave Cote, Future Mold sales engineer. "If the customer does a prototype here, it'll be very close to the production requirements."
The prototyping machine will help reduce the risk for thermoformers developing new products, said Jim Martin, a technical support specialist at Future Mold, who will be in charge of it. It also will make it easier to get the product to market, "because you don't have to go through all the hassle of the development work after the production tooling has already been built and delivered."
Cote said speeds have increased with thermoforming equipment, thanks to third-motion technology and oven control. This machine will allow customers to see if a particular material can be thermoformed, and how it will react.
Moore said Future Mold's expansion will provide greater exposure for the Low Flex 3.0 system and will serve as a technology showroom. Other TSL partners — such as Italy's Tria SpA, a grinder maker, and Homer, Mich.-based DJS Systems Inc., a packaging specialist — also will show off their technology and equipment in the showroom.
He said the TSL/Future Mold partnership is longstanding. The "relationship between TSL and Future Mold is noncontractual. We have worked together on literally hundreds of projects for more than 35 years," Moore said.
Allan Gerlat, correspondent
Contact:
Future Mold Corp., 989-588-9948, www.futuremoldcorp.com
Thermoforming Systems LLC, 509-454-4578, www.tslusa.biz/en
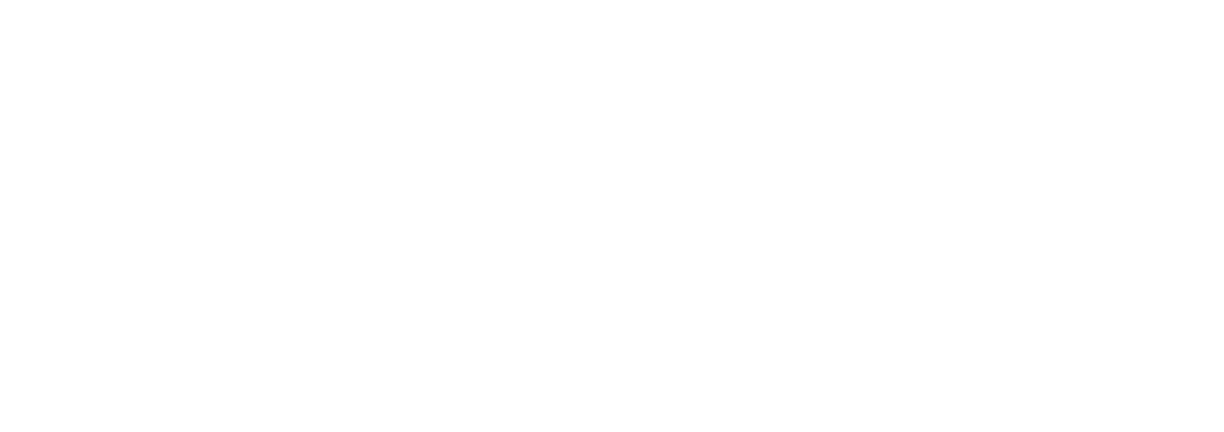