Molecor, Madrid, has introduced its latest machine, the M-OR-P 5012, which molecularly orients PVC during the manufacture of pipes with a nominal diameter (DN) of up to 1,200mm, about 48 inches.
The machine becomes the largest in Molecor's portfolio. In 2008, it introduced its M-OR-P 3180 System, which allows for the manufacture of pipes up to 800mm DN, about 30 inches, which at the time was the largest size available.
Molecor specializes in the development of molecular orientation technology for manufacturing PVC-O pipes for conveying water under pressure; it also has a pipe-making division. The new machine has an output of more than 1.5 tons per hour and is installed right after the extruder, working inline with it. Details were presented at the K show.
Molecor's equipment is designed to manufacture PVC-O pipe that is lighter than standard PVC, with better impact resistance and increased tensile strength. It can be used in fire-suppression systems, water mains and irrigation applications.
PVC is an amorphous polymer with randomly aligned molecules. However, by subjecting the material to tightly controlled pressures, temperatures and speeds, the machine can align the molecules as it stretches the pipe. The Molecor system orients the molecules using hot air. Compared to other systems, which use boiling water rather than air, Molecor's system is more energy-efficient and more cost-effective, according to the company.
The molecular orientation process enhances PVC's physical and mechanical properties, increasing flexibility and resistance to fatigue and impact, according to the company. The technology produces Class 500 PVC-O pipes, the highest classification under ISO standards.
Molecor's molecular orientation technology makes possible the creation of larger-diameter PVC pipes that the company believes gives it a competitive advantage.
"Our technology … is able to overcome these limitations of not being able to manufacture big pipes under high pressure," said Dolores Herran, business development manager.
The total length of the M-OR-P 5012 machine is 125 feet by 62 feet wide when used with equipment to create the company's Integrated Seal System, or ISS+, although it can be slimmer without the ISS+, at about 29 feet. With an extrusion line, the production line can be 230 feet long. ISS+ allows PVC-O pipes to be joined using sockets. Molecor socketing systems apply hoop and axial orientation to the socket to withstand stresses at any point. Because the socket is produced simultaneously with the pipe, there is no need for reheating and no variation of properties in comparison with the rest of the pipe. ISS+ equipment inserts a rubber gasket inside the pipe during manufacturing so that sections of pipe can be pushed together or plugged into one another.
Molecor will use the M-OR-P 5012 model to manufacture its own PVC-O pipe at its facilities in Spain, and it will offer equipment for sale to other pipe manufacturers. Companies purchasing the equipment must also pay a licensing fee and sign a licensing agreement.
The agreement protects Molecor's intellectual property rights, but it also includes training on the technology and the company's assistance in installing the equipment and ensuring it is operating correctly, according to the company.
Molecor has established joint ventures with pipe manufacturers in South Africa and Malaysia.
"Molecor activity is developed around two main axes: the development and manufacture of increasingly efficient systems (machinery) and the manufacture of oriented PVC (PVC-O) pipes," company spokeswoman Almudena Blázquez said in an email response to questions. "If other manufacturers desire to acquire our technology, we will be very pleased [to provide] them with it. Besides this, we help them in the whole process of implementation of the technology from the beginning of the project to the startup."
M-OR-P 5012 machines will be available for sale to U.S. manufacturers once all tests and validations are carried out, Blázquez said. The company assembles the equipment at a plant in Madrid, where it also conducts research and development.
Bruce Geiselman, correspondent
Contact:
Molecor, 34-911-337-090, www.molecor.com
Bruce Geiselman
Senior Staff Reporter Bruce Geiselman covers extrusion, blow molding, additive manufacturing, automation and end markets including automotive and packaging. He also writes features, including In Other Words and Problem Solved, for Plastics Machinery & Manufacturing, Plastics Recycling and The Journal of Blow Molding. He has extensive experience in daily and magazine journalism.
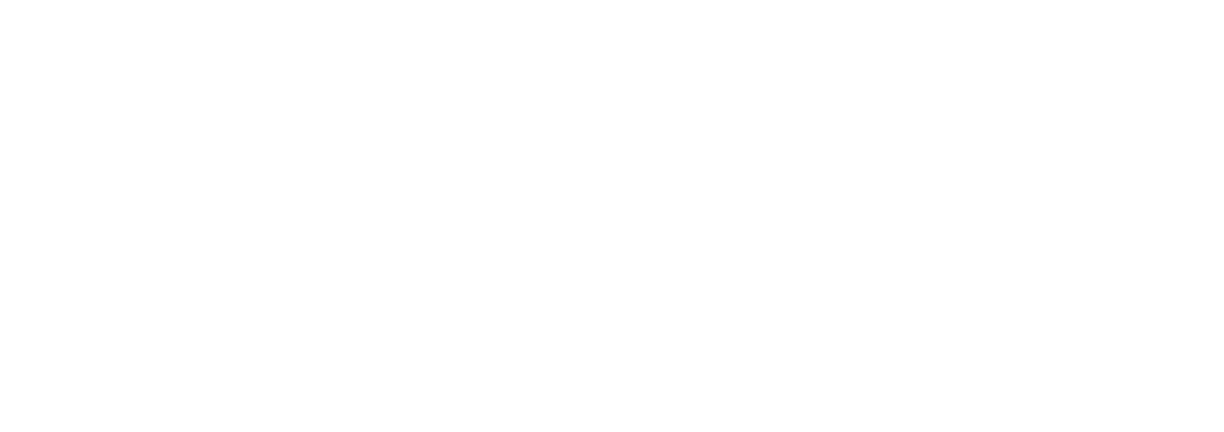