Special Report: Central cooling systems adopt advanced technologies
The incorporation of advanced control technology to improve efficiency, as well as a rethinking of the definition of system modularity and flexibility, mark developments from three suppliers of central cooling systems that aim for increased capability.
AQUATECH'S EASYCOOL+ IS SELF-ADJUSTING
At the K show, Aquatech Srl, Santa Maria di Sala, Italy, launched a new line of central chillers that automatically match the amount of cooling capacity to a plant's requirements.
The Easycool+ line was created specifically for the plastics industry, and features components and functions that provide self-diagnostics during startup, flexibility during operation and energy savings compared with conventional "fixed" central chiller systems, said Giorgio Santella, chief marketing officer for Piovan SpA. Piovan is Aqua-tech's parent company, also based in Santa Maria di Sala. Aquatech's products are offered in the U.S. through sister company Universal Dynamics Inc., Woodbridge, Va.
The Easycool+ line consists of 34 models with cooling capacities from 15 tons to 150 tons. The chillers are designed to deliver greater efficiency and automatic control at a cost that is competitive with conventional central cooling systems.
The chillers have a favorable energy efficiency ratio (EER) due to their ability to adjust cooling capacity, pressure, temperature and more. EER indicates how many kilowatts (kW) of electricity are required to produce a kW of cooling capacity.
With Easycool+, at 100 percent heat load the unit will require 1 kW to produce 3.5 kW of cooling capacity (an EER of 3.5), which is about 0.5 to 1 ton of cooling capacity, Santella said. The EER improves when the chiller is used with partial heat loads, Santella said.
In comparison, a conventional fixed cooling system at 100 percent heat load has an EER between 2 and 2.5, Santella said. Conventional chilling systems can have a lower EER, due, in part, to components that add to the heat load, and also because their design does not allow for the management of partial loads.
Easycool+ chillers have several features that allow them to automatically adjust when cooling requirements change. This includes a unique configuration of two Copeland multiscroll compressors of different sizes. Using different sizes of compressors allows the chiller to precisely tailor compressor operation to cooling demand.
The small compressor is turned on automatically when less than 35 percent of cooling capacity is required, the large compressor is used for 35 to 60 percent of capacity, and both compressors operate to achieve 61 to 100 percent of capacity, Santella said.
"Aquatech is the first company to introduce what's called 'uneven compressor assembly,' where a larger and smaller compressor work together. This is beneficial for energy utilization. Conventional central chilling systems operate at their maximum cooling capacity all the time and are not designed to handle variable heat loads," Santella said.
Heat loads in a plastics plant vary when a machine is taken off-line, or when a new mold — with different heating and cooling characteristics — is installed.
The air-cooled Easycool+ incorporates fans from ebm-papst Inc., programmable controls and electronic expansion valves from Carel Industries and electromechanical devices from Siemens and ABB, Santella said. Aquatech offers Easycool+, which uses the refrigerant coolant R-410a, with a choice of two evaporator types: brazed plate or shell-and-tube.
Easycool+ also features Aquatech's new automated pressure control. It uses process-water pumps driven by electronic inverters to automatically and precisely maintain the pressure in the water supply line at the highest pressure required. The control also ensures even distribution to all processing machines in the system.
"Users can set the system water pressure to the molding machine with the more demanding thermal condition. This is important in terms of energy consumption and life of the components of the chiller system," Santella said.
In a plant with 50 molding machines, where one mold requires a cooling water pressure of 50 pounds per square inch (psi) and the remaining 49 molds require 30 psi, a conventional system would be adjusted to deliver 60 psi of water pressure. "A conventional system will continue to operate at 60 psi even after the mold requiring 50 psi water pressure is taken off-line, while Easycool+ would immediately adjust water pressure to the lower pressure," Santella said.
Easycool+ is designed to maintain a selected temperature differential between the water delivery and return circuits. Each mold has a specific cooling flow velocity that is ideal for optimal heat exchange, Santella said. Typically, the temperature differential for a central cooling system is set based on the tool with the narrowest temperature differential.
"A conventional, fixed central cooling system serving an operating mold with a two-degree temperature differential would continue to operate the chiller to hit that narrow temperature delta even if that mold were removed and the remaining molds in operation had a 10-degree temperature differential," Santella said.
"Water flow is never stable and changes depending on the heat load. The higher the heat load, the higher the volume of water needed to circulate in the cooling pipes," Santella said.
Aquatech also developed plug-and-play technology as part of its advanced control software to automate a number of diagnostic checks. "When a molder changes a tool, some water from the chilling system may remain in the mold and becomes lost to the system, while the new mold being installed may be empty of water and has to be filled. Conditions in the molding shop like cooling level in the tool or the cooling system represent a critical aspect to the process," Santella said.
Air left in the cooling circuit of a newly installed mold can cause problems with water circulation and part quality.
At startup, molders using conventional systems must:
• ensure there is no air in the mold,
• confirm that all the cooling circuits are filled, and
• be sure that water circulation is adequate.
"Users simply replace the mold, connect it to the molding unit, and Easycool+ will automatically conduct a diagnostic and handle the various startup tasks. The plug-and-play technology of Easycool+ will determine if water is required for the system and how much, and will refill the circuits. For a user with multiple machines conducting mold changeovers multiple times a day, this feature saves set-up time and ensures a good setup," Santella said.
The control software monitors operating parameters and can identify system abnormalities, even from a remote location.
FRIGEL UPDATES CONTROL AND ADDS NEW MODELS
Frigel North America Inc., East Dundee, Ill., has both expanded and improved its Heavygel line of air-cooled central chillers. Using advanced control technology, the new models improve productivity by providing more operational data for process-cooling equipment.
The Heavygel line has two basic model types, the 3HL and 3HM. Frigel has expanded the line so that a total of 34 versions are offered, up from 12, said Al Fosco, global marketing manager.
The chillers are designed to deliver 26 to 393 tons of cooling capacity and are available for operation in ambient temperatures ranging from 5 to 131 degrees Fahrenheit.
The Heavygel models provide optimal cooling without the need for a water source for the condenser. The 3HL chillers, which come in standard and high-temperature versions, have dual cooling circuits and feature Bitzer screw compressors that allow for an infinite control of cooling capacity. Molders can purchase the chillers with or without pumps, tanks or a central water handling system.
The 3HM chillers use hermetic scroll compressors. They have two options for evaporators: a stainless steel brazed plate, or a shell-and-tube evaporator with drain and vent valves. 3HM chillers can have single or dual cooling circuits, with up to four compressors. They also can be designed as a packaged system with integrated pumps and tanks.
Frigel has offered the Heavygel 3HM units in standard versions with capacities from 17 to 60 tons and operation from 23 to 64 degrees Fahrenheit working in ambient temperatures from
5 to 109 degrees Fahrenheit. The company also offers high-temperature models for ambient temperatures from 41 degrees to 131 degrees Fahrenheit and cooling capacities from 17 to 85 tons. Fosco said an emphasis on correctly sizing the condensers and fans makes it possible to offer an air-cooled model for use in ambient temperatures of up to 130 degrees Fahrenheit. He said most air-cooled central chillers are designed for 95-degree ambient air.
In addition, Frigel has added the 3PR Intelligent Control System, its new proprietary control technology, to the Heavygel line, as well as to its Microgel line of machine-side chiller/temperature control units and its Aquagel line of pumping reservoir and filtration components. The 3PR control helps to increase the overall accuracy of the system to plus or minus 0.5 degree Fahrenheit, Fosco said.
3PR, which was first installed on Frigel's Ecodry closed-loop adiabatic central cooling system line in 2015, allows users to view, control and optimize all aspects of their equipment based on real-time data. It automatically adjusts the cooling system to ensure optimum performance based on a range of parameters.
"The 3PR provides real-time schematics, full diagnostic tools and multiple selectable languages. All mechanical, electronic and electric characteristics of the chiller can be viewed," Fosco said. All components in the chiller have either company-installed sensors or performance data that can be accessed by the control technology — such as fan motors with variable-frequency drives, Fosco said.
Frigel developed several new screens and upgraded others for use with the central chiller systems. "All refrigeration components, water components, water flow rates, refrigerant pressures, fan speeds, compressor loading capability are monitored. The control gives the user a complete idea of what is going on in the chiller," Fosco said.
The 3PR software can determine what the actual cooling load is and whether the chiller has enough cooling capacity for the task at hand. With the control, users can check the status of a specific component, such as the condenser, evaporator or fan, if they see a change in a process parameter. Users can know immediately if the chiller is low on refrigerant, or what the process water flow rate across the evaporators is.
"This is a big deal. Oftentimes, when a cooling system is being designed, it is the customer that provides information about cooling and we would tweak the system to determine the actual cooling load. The system can accurately determine cooling capacity by viewing data on cooling flow and temperature differential," Fosco said. The 3PR control can tell the user when to check a chiller component, based on the number of operating hours. The control and software also generate a complete readout regarding energy consumption, so a user knows the actual energy consumed by the chiller at any given time.
Previously, Frigel had used a simple controller in the Heavygel line, giving the user basic process information such as water temperature, pressure drop, set points and codes for alarms. With 3PR, users can link the chiller to a plant management system using the Ethernet, or connect remotely to a Frigel service technician. The controller can be set up to suggest possible solutions based on the type of alarm.
The 3PR control features troubleshooting guides and the ability to log event and processing data. A history of every alarm, process deviation and operating parameter can be captured and analyzed. The control features a 7-inch full-color touch screen.
ECOCHILLERS ROLLS OUT SCALABLE CENTRAL CHILLER SERIES
EcoChillers Inc., Austin, Texas, earlier this year launched its new Inverter line of air-cooled central chillers, designed to deliver up to 12 percent greater efficiency compared to competing models, said Pedro Machain, process engineering manager.
The Inverter chillers are modular, allowing as many as 10 30-ton stand-alone units to be combined in a single frame for up to 300 tons of cooling capacity. This gives the user the flexibility to add or remove one or several of the individual 30-ton units as production needs change.
A system that delivers 300 tons of cooling capacity has a footprint that's considerably smaller than a conventional system with the same capacity, Machain said.
Users can group some of the Inverter chillers that are combined within a single frame and direct a group's cooling capacity to a specific task. It is possible to operate different groups at different temperatures using dedicated connections.
EcoChillers offers the Inverter in air-cooled or water-cooled versions. They are available with a scroll compressor, screw compressor or semi-hermetic compressor, which is the easiest to service, Machain said.
Mikell Knights, senior correspondent
Contact:
EcoChillers Inc., 956-284-0237, www.ecochillers.com
Frigel North America, 847-540-0160, www.frigel.com
Universal Dynamics Inc., 703-490-7000, www.unadyn.piovan.com
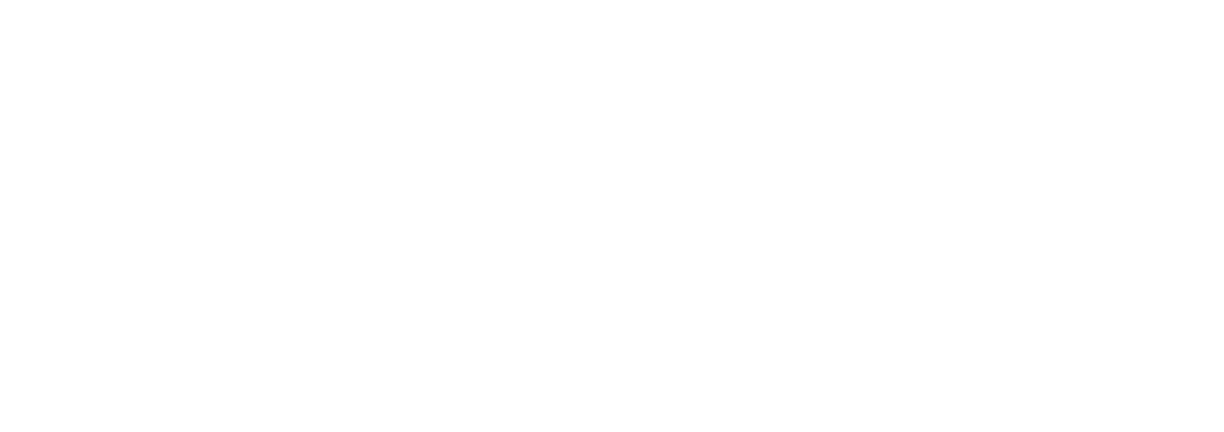