Special Report: Machine controls gain ground in performance, connectivity
Suppliers of machine controls are upgrading their products with cloud-based data collection and analysis capabilities as well as improved hardware and software. Enhancements give users more access to comprehensive information about machine diagnostics, cycle times, power consumption and other factors that can help them run more efficiently at all levels of their operations.
HARDWARE AND SOFTWAREDEVELOPMENTS FROM SIEMENS
Siemens Industry Inc.'s Digital Factory Division, Norcross, Ga., added a new digital PLC to the Simatic S7-1500 family, and has added data-handling functions to upgrade another unit in the line for increased functionality, said Mathias Radziwill, business development manager, plastics.
The new S7-1500 T controller combines automation and drive-related tasks in a single device.
"If you had a thermoforming machine, for ex-ample, that unit typically would include a controller dedicated to synchronizing the movements of the two platens, while a second installed controller would be used to ensure the automation, including safety requirements, visualization and other tasks of the machine. With the new S7-1500 T, users now have to program a single device rather than two controllers, and need only connect one controller to the machine, which makes it easier and less time-consuming to set up and use," Radziwill said.
Siemens also added more data-handling functionality to the existing S7-1500 controller. The controller now includes a server that allows users to connect any kind of third-party device to it for monitoring and control, with results viewed via a web browser.
A new trace view function acts as a troubleshooting tool that allows the controller to quickly pinpoint machine operating issues. Completed traces can be viewed as graphs directly on the the central processing unit (CPU).
"If, for example, the unit is installed on an extruder and the user finds that the barrel heaters are not working as expected, they can use the new function as an easy way to check remotely the temperature trace for each heater zone," Radziwill said. Users view the captured data from the heaters through the web browser function of the controller to find the zone that is working improperly.
Users also can back up data held within the RAM of the controller. They can store the data onto a memory card right from the display of the controller, without having to transfer or download the information to a PC first, Radziwill said.
The Simatic ET 200SP open controller, introduced last year and featuring a PC-based CPU, has been upgraded with a digital visual interface (DVI) graphical port that allows a monitor to be connected to it. The company now also has incorporated visualization software used to design injection molding graphics into the Simatic ET 200SP's CPU. Siemens will show sample design screens at its K show booth this month. Radziwill said the unit has a USB port that allows users to connect a memory card for data storage.
Siemens also developed MindSphere, its new industrial cloud-based platform for process, production and plant data collection and analysis that can be applied by a molder or machine builder. It is designed to cull information from any piece of equipment.
The platform, now being launched in the U.S., provides applications for online monitoring of machines and manufacturing cells. That includes data storage and secure processing of data, which can lead to minimized downtime and optimized performance. The data make predicting maintenance schedules and determining hourly rates for machines easier, said Stephan Ihmels, business development manager for the cloud-applied, data-services group within the Digital Factory Division.
"We provide the open interface, digital platform and infrastructure, allowing users to build their own specific business service models using applications from Siemens but also allowing them to build their own specific applications based on MindSphere and thus Siemens will develop an open ecosystem. MindSphere captures user- defined data from their industrial assets, including process machinery, Siemens control devices or third-party equipment," Ihmels said.
Users can connect their equipment to the MindSphere digital platform through the OPC-UA industrial communication protocol using MindConnect Nano, a connector box for simple, secure communication. They can also use a software development kit or integrate their equipment using Siemens' Simatic line of controllers.
Users can apply MindApps — application programs created specifically for MindSphere — for predictive maintenance, energy data management or resource optimization. Siemens, third-party developers, customers and machine builders can develop and offer specific applications to work with MindSphere.
MindSphere lets users customize the level of intermachine connectivity, as well as the machines that are connected. It's offered as a subscription service, so users pay based on the type and level of functions they need. "One user may collect just a few data points for MindSphere, configuring the system to select the data every minute. Another molder would pay more to connect hundreds of data points and monitor a wider range of selected parameters every second," Ihmels said. A North American molder is currently testing MindSphere, and Siemens is in discussion with several other North American processors.
MACO-SYS NOW OFFERSTHE MACO LINE OF PRODUCTS
Eurotherm by Schneider Electric, Ashburn, Va., has sold its entire Maco business of control technologies designed specifically for plastics manufacturing to a new company, Maco-sys LLC, Machesney Park, Ill.
The new company, which started business Sept. 1, has enhanced its OptiPak II controller for use in applications other than injection molding, said Dave Spahr, president of Maco-sys and former director of engineering for all Maco products under Eurotherm. The Opti-Pak II controller was originally designed as a cost-competitive, dedicated PLC system for injection molding. It offers features similar in functionality to the flagship Maco Compact series, but with a finite number of input/output (I/O) channels and enough temperature-control loops to fit small- to medium-sized injection presses.
Maco-sys has integrated aspects of its Breeze IIc controller — used strictly for control of the wall thickness of bottle parisons — into its Opti-Pak line to create the Opti-Pak BM, designed for small blow molding machines, Spahr said. The new development extends the level of control for blow molding, and is designed to fill a space between the parison-only control and the premium Maco Compact series.
The Opti-Pak BM brings greater functionality and a more encompassing, system-type of machine control to small blow molding machines. The integrated product is an alternative to employing multiple discrete PLC and temperature controls. It improves operating speed and reliability and makes programming easier, Spahr said. (See related story here).
Maco-sys also is developing an Opti-Pak II version for small extruders that integrates functions from its EM-3c control system. The Opti-Pak II controller is offered in a fixed format while the EM-3c is flexible. The new version of the Opti-Pak II will allow users to activate or deactivate, install or remove functions from the system.
The Opti-Pak II systems for extrusion control have a scalable number of I/O channels, unlike the traditional Opti-Pak II system, which features 56 I/O points, said Spahr. "Users can get 24 I/O points if they need 12 zones of heat-cool control and can expand or scale back the I/O points," Spahr said. Users can network Opti-Pak II units to control multiple extruders.
KEB AMERICA ADDS A ROBUST ROUTER
Processors with complex production cells or precision products increasingly are demanding machine controls capable of high-speed communication, said Jonathan Bullick, sales manager for KEB America Inc., Shakopee, Minn.
"As production machines get faster and molding precision increases, control has to be more responsive. There is a trend for enhanced machine diagnostics, data logging, power consumption and communication, and the controllers need components that deliver higher performance or incorporate more functionality," Bullick said. New tools and software allow different types of machine controls to communicate with components at different levels of the manufacturing cell, plant or enterprise, said Bullick.
In the area of high-speed communications for machine control, KEB America recently launched its Ethernet-based C6 router, which can be connected to any third-party PLC. The single-cable or wireless connection eliminates the numerous wires that are required for discrete controls.
The router allows machine operators to remotely access machine parameters and programs, which facilitates machine setup and commissioning, and can eliminate the costs associated with a visit by a field technician when the machine isn't functioning properly, Bullick said.
KEB America added improved operating and diagnostic functions to the C6 router so that it monitors the machine and can react to changes. The programmable router can log data, retrieve/generate trending information and deliver critical alarms. The router connects to a master control or PLC, then the user can set up critical parameters to be monitored through the router. The settings are uploaded to the router, which collects the information at a time specified by the users, Bullick said.
KEB America also developed a new line of HMI discrete controls that feature a touch-screen panel with the gesture, swiping and tapping features common on smartphones. The industrial control connects easily through a bus or Ethernet connection yet has a number of security features that protect data, Bullick said.
At last month's International Manufacturing Technology Show in Chicago, KEB America introduced its new C6 Smart line of embedded machine controls, designed as a cost-saving alternative to an HMI that has all of the processing power onboard. The controller features EtherCAT communication for remote access to data and integrates a coupler device, so it is smaller than the previous C6 Compact II. It has an option for a digital visual interface (DVI) output that allows the user to create graphics on the controller itself prior to sending the data to a monitor, Bullick said.
BECKHOFF TARGETS OLDER MACHINESWITH NEW CONTROLLER
Beckhoff Automation LLC, Savage, Minn., has developed a controller that allows data from older processing equipment to be transmitted to a cloud-based server. The IoT controller, which will be commercially available early next year, is based on the company's CX platform of PC-based machine controls.
The controller serves as an interface to cloud-based data collection and analysis programs that can evaluate data trends then provide suggestions on how to improve production, said Thomas Kosthorst, business development manager, plastic processing machines. The IoT controller reads data from the machine, such as cycle time and energy consumption.
Beckhoff also is preparing a new software program for monitoring the condition of a machine. The new TwinCat Analytics software will be a tool processors can use to understand performance and potential maintenance issues. With access to a lengthy history of parameters stored on a remote server, they can determine the source of production problems.
"It can be used to measure the machine load, so users can determine if or where a weak point in their machine process exists. If molders discover their machines are working outside optimal operation conditions regarding consumption or machine load, that can prompt a change in the sizing of their motors for their next machine purchase," Kosthorst said. The software will be compatible with a range of Beckhoff machine controls.
With their data captured in the cloud, processors with multiple operating sites or manufacturing cells can digitize the know-how of skilled machine operators.
Mikell Knights, senior correspondent
Contact:
Beckhoff Automation LLC, 952-890-0000, www.beckhoffautomation.com
KEB America Inc., 924-224-1400, www.kebamerica.com
Maco-sys LLC, 815-341-2637, www.maco-sys.com
Siemens Industry Inc., 800-743-6367, www.usa.siemens.com
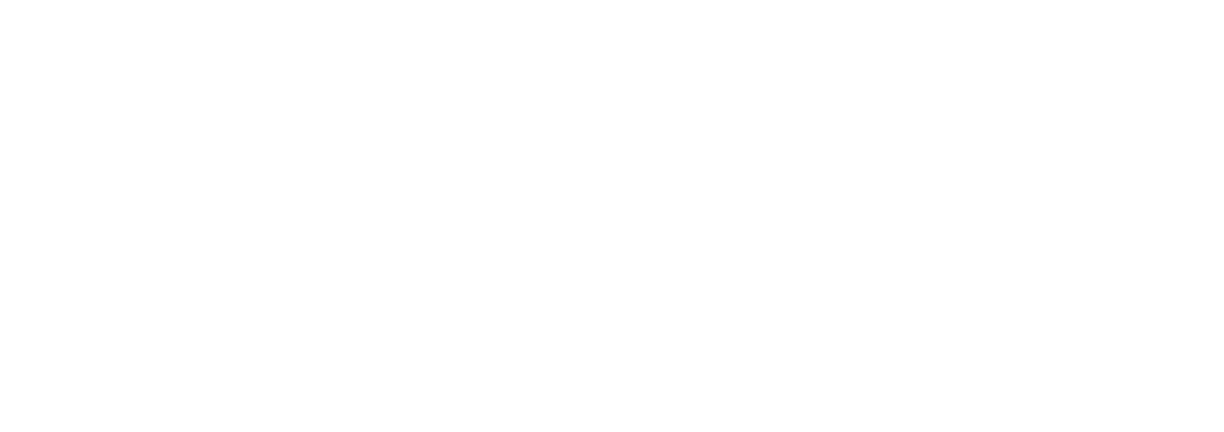