Special Report: Control retrofits bring new life, cost savings to extruders
When should a processor consider an upgrade to the controls on an extruder? The answer depends on several factors, including production of excessive scrap, unexpected downtime or obsolescence of critical electronic components.
Companies that perform extruder control retrofits recommend performing a machine audit to determine the condition of the existing control, and that the scope of a retrofit job should be defined before any work proceeds. Whoever performs a controls retrofit should have a solid understanding of controls technology as well as the extrusion process. In cases where it makes sense, a controls retrofit can significantly boost performance at a lower cost than buying a new machine. The good news is that there are good options for upgrading extruder controls.
Scott Barlow, president of Integrated Control Technologies (ICT), Coppell, Texas, which makes aftermarket extruder controls, said that an extruder control upgrade can be expensive, and one of the challenges for the processor is determining whether the upgrade will provide enough benefits to move ahead.
In November 2015, ICT introduced Revisor, a screen-oriented extruder control designed to replace buttons and knobs on an extruder. It is configurable, so the user can specify barrel and die zones, drives and operating pressures. Barlow said that the Revisor can reduce the cost of retrofitting an extruder control by half, when compared to ripping out and replacing controls and drives in a traditional retrofit job.
ICT now has taken Revisor one step further, by introducing application tiles — software modules that allow the user to specify far more components on an extrusion line. So far, the company has developed application tiles for three product categories: blown film, pipe and profile, and coated wire and cable. Barlow said ICT is talking with an aftermarket supplier of blown-film bubble-control equipment, with the aim of working together to marry the two types of products.
He also noted that ICT now is working on a project to supply customized application tiles for a large extrusion company, which will then be distributed to lines throughout the plant. The project is an example of how ICT can tweak the application tiles to conform to a plant's unique process. Because the plant can perform the work in-house, it can significantly reduce the cost of a retrofit.
In addition, ICT has developed a Revisor LT, a smaller version of the Revisor that can be used for smaller extruders. Barlow said the standard Revisor is priced at about $20,000 and the Revisor LT is priced at about half that. He notes that not every extruder is a good candidate for the Revisor retrofit. For one thing, the cabinet housing the wires and electrical components should be in relatively good condition. In those cases, or where the customer doesn't have an issue with replacing the old cabinet with a new one, the Revisor is a viable way to keep retrofit costs down and doesn't require special expertise to install.
Barlow said the Revisor, which is part of the company's Tempcon product line, represents a new business model. "We believe that this is the future of the industry. We think there is going to be more of a trend of what people will expect to see: user-configurable [systems] where they can be a novice and set it up," he said. It still is important to understand the extrusion process. The Revisor ships in three days, he said.
Processors considering an extruder control retrofit may also consider evaluating their drives and motors for a potential upgrade, which significantly impacts the efficiency of the extruder. "DC is very inefficient," he said. "Typically, we have seen that AC is 10 to 15 percent more efficient when operating an extruder." He estimates that 60 to 70 percent of the extruders in service that are 10 years old or older are DC. Drives and motors typically have a two- to three-year payback period, he said.
Barlow said ICT stocks AC drives and motors with power ratings of up to 500 horsepower and ships them within 24 hours and can have them up and running within 24 hours of a notified failure. Of the decision to upgrade the extruder machine upgrade or the drives and motors, Barlow said it depends on the plant's goals. "If they are after efficiency, they go for the drives. If they are after dependability and process control, they do the controls."
SIDESTEPPING OBSOLESCENCE
Obsolescence is a key factor when it comes to requests for controls upgrades from customers, said Mike Puhalla, director of engineering and technology at Milacron LLC, Cincinnati, which performs control retrofits only on its own extruders.
"There are still controls out there that are a decade old or more and they still run, but the challenge we have in the world of electronics is that things eventually become obsolete and need to be updated," he said. He added that it's for the better, because it results in an extruder control that is more robust and reliable.
Davis-Standard LLC, Pawcatuck, Conn., performs control retrofits on its own extruders as well as extruders from other suppliers. Depending on the age of the system, the company might recommend upgrading computer hardware, the computer plus the software, or, in cases where the drives and PLCs are obsolete, a complete system retrofit, said John Clemens, the company's director of extruder controls.
He said a complete upgrade is a cleaner installation, and tends to involve less downtime than retrofit jobs involving replacing selected components that have to be fit into a cabinet. The other advantage of a complete upgrade is that the unit comes to the customer completely tested and configured. The type of controller that is installed depends on the scope of the job and the customer's needs, he said.
In the case of a retrofit for a control from another OEM, Clemens said the difficulty of the job depends on whether the customer has the documentation of the older system. If not, Davis-Standard dispatches a technician into the customer's plant to reverse-engineer the system and build a control system that adheres to the design of the older control. In addition, the company audits the extruder line and advises the customer on what needs to be done to have the control comply with safety standards, he said. Davis-Standard recently began offering upgrade options at its location in Suzhou, China.
Al Bailey is East Coast controls manager for Lebanon, Ore.-based Entek, which performs control retrofits on both its own extruders and those of other suppliers. "Every OEM has advantages and disadvantages when it comes to controls," he said. "We quote every retrofit like it is a custom package. We examine the machine, look at the electrical components, find out what the customer wants to salvage and what they don't, and what type of upgrade they want." The company has its own staff of controls engineers who are qualified to customize the controls for its customers.
Bailey said that the company uses off-the-shelf components whenever possible when doing control upgrades, and opts for open communication protocols when performing retrofits. He added that finding support for control components can become harder as they get older and said the company has performed retrofits on older machines that use proprietary control packages that have become obsolete.
"We have ripped out the proprietary control system and put in an Allen-Bradley control system to get their machine up and running," he said. "I believe that Rockwell [which supplies Allen-Bradley components] has the longest lifespan when it comes to PLCs."
Milwaukee-based Rockwell Automation also makes an effort to work with extruder OEMs, which are typically its customers for new equipment sales, said Brian Fieseler, program manager for OEMs at Rockwell.
"We try to coordinate with their aftermarket," he said. "Much of the equipment that we help them to deploy on new equipment can be purposed over to an upgrade as well."
Still, Rockwell offers customers flexibility when it comes to making any upgrades. Often, the cost of new equipment is not that different from the cost of making an upgrade, he said. For example, Rockwell supplies drives for both AC and DC motors, providing the customer the option of either upgrading to the more efficient AC technology or staying with existing DC motors.
Mike Green, GM of Cincinnati Process Technologies (CPT), a company based in Cincinnati that provides upgrades to controls on plastic processing equipment including extruders, agrees that obsolescence is one factor in control retrofits.
But in his view, extruder control retrofits especially show their value on more sophisticated processing jobs.
"If you have a more complex process, you need the control; you have more downstream equipment and want to pull those downstream activities into a central location and coordinate and control those," he said. "That is really where more of the justification comes in for upgrading a process control on an extruder."
As an example, he said a recent project for CPT was upgrading the control on a multilayer coextrusion line for pipe. That project had an added level of complexity because it encompassed three extruders, each from a different OEM.
John DeGaspari, senior correspondent
Contact:
Cincinnati Process Technologies, 513-619-7415, www.cinprotech.com
Davis-Standard LLC, 860-599-1010, www.davis-standard.com
Entek, 541-259-1068, www.entek.com
Integrated Control Technologies, 972-906-7445, www.integratedcontroltech.com
Milacron LLC, 513-536-2000, www.milacron.com
Rockwell Automation Inc., 414-382-2000, www.rockwellautomation.com
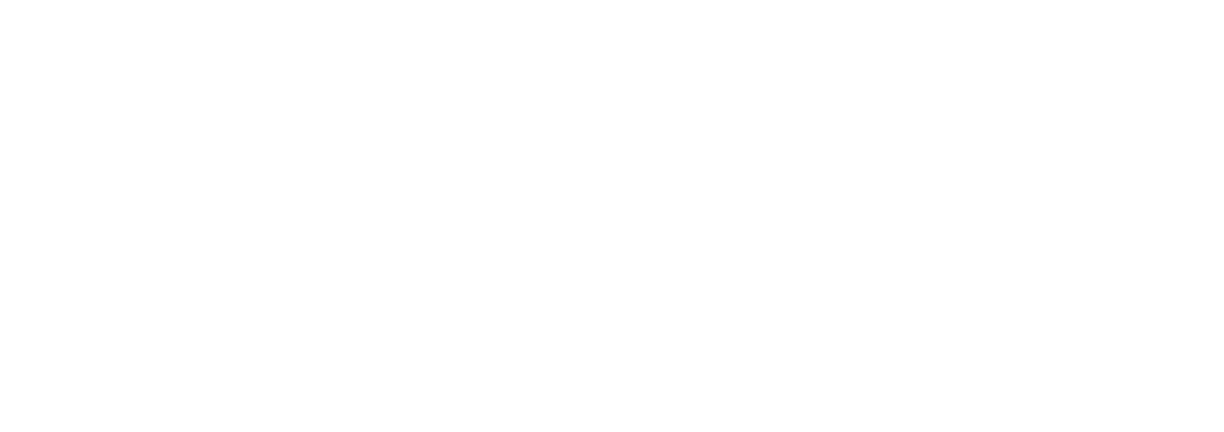