Some extruder suppliers are gearing up to meet increasing demand for wood-plastic composites (WPC) in the U.S. They are working on new screw designs as plastic lumber manufacturers increase the wood-fiber content in their products and also incorporate new polymer coatings.
Davis-Standard LLC
Davis-Standard LLC, Pawcatuck, Conn., has a bullish view. Over the past year, the company reports not only an increase in quote requests from the WPC lumber industry, but an increase in extruder sales as well.
"I have quotes in to several of them," said Tom Malec, Davis-Standard regional sales manager. "They're all very busy."
The WPC lumber industry went through considerable consolidation following the 2008 economic downturn, which resulted in extrusion lines being idled. Over the last decade, plastic lumber manufacturers have been able to meet demand with equipment on hand. As the economy improves, however, demand from construction companies is growing.
"The activity has been quite good," Malec said. "From our end, [WPC] suppliers said they have been busy for the past couple of years. They have been able to handle capacity, but it has gotten to be more and more."
That has resulted in a few additional sales and even more inquiries about purchasing equipment. "There was a shakeout in the industry, and now the people still around are thriving," Malec said.
Sean Stephan, regional manager at Davis-Standard, agreed the WPC lumber market is showing improvement.
"We have several customers that are working on introducing new products, and we do expect new orders for equipment to continue," he said.
While extrusion equipment technology remains largely unchanged over the past several years, one constantly evolving area is screw design.
"Consumers are demanding [WPC lumber] products with improved performance and less cost," Stephan said. "Consumers want a product that is stiffer, easier to install and will not fade or degrade over time. This pushes the manufacturers to find solutions. It also forces the equipment suppliers to improve and refine the equipment. The most significant changes have been in the screw design and wear characteristics. As new additives and material combinations are introduced, new screw technology is required. Heavily filled material combinations require screws that are extremely wear-resistant."
Extruder manufacturers vary their screw designs based on factors such as the amount of virgin versus recycled plastic, and the amount of wood filler. Malec said that improvements Davis-Standard has made include using harder coatings for the screw flights and more durable barrel linings.
Milacron LLC
Milacron LLC, Cincinnati, reports that extruder sales to WPC lumber manufacturers are stronger overseas than in the U.S.
"The activity in this market is minor for 2016," said Michael Ellis, a company spokesman. "Producers have been able to meet any increased demands through productivity improvements and [bringing] more capacity online that had been idled. A few spot expansions have occurred overseas, primarily in Europe."
Mike Puhalla, director of engineering and technology for Milacron's extrusion technologies, said the number of WPC lumber manufacturers in the U.S. has remained steady since massive consolidation in the late 2000s. "Truly, over the last decade here in the United States, there have not been any brand-new greenfield plant installations for wood composites," he said.
However, Milacron still sees opportunities in the U.S. because of the changing characteristics of WPC lumber. Like Davis-Standard and others in the industry, Milacron said that manufacturing boards with more fiber content requires changes in screw geometry. WPC manufacturers are also putting additional polymer coatings on top of the boards to improve their performance. To do that, manufacturers often must use two extruders.
"You have your main extruder that is going to make the board you see, as well as a secondary extruder that is moving this capstock coextruded polymer over the top of the board that enhances its UV protection against sunlight," Puhalla said.
Those demands create opportunities for Milacron to sell new extruders or make changes to existing equipment, which involves changing the screw geometry as well as the metal coatings on extruder screws.
"Not so much in the United States but overseas, we're seeing [increased usage of] products like Surlyn, a high-impact polymer," Puhalla said. "It has a tendency to be somewhat corrosive, so you need to look at the metallurgies on your screws and make sure you give the proper screw geometry so you can handle that kind of polymer."
Screws are normally made out of carbon steel, and in a normal application, manufacturers put chrome on it. However, with some polymers, stainless steel might be more appropriate than chrome, he said.
Although the market shakeout in 2008 resulted in idled extruders, it also created aftermarket opportunities, Puhalla said.
"The extruder itself is fine, but they need a screw geometry now for that extruder, and we would fit that into their machine," Puhalla said. "We see opportunities where we service not only our extruders but competitors' extruders. We can sell them our aftermarket technology onto a competitive brand of extruder. We see that as a lucrative way to expose a customer to our technology."
eFactor3 LLC
Pineville, N.C.-based eFactor3 LLC, the North American distributor for MAS Maschinen und Anlagenbau Schulz GmbH, Pucking, Austria, also sees growth opportunities in the WPC industry. "It is not limited just to the lumber business," said Hartmut Bendfeldt, eFactor3 president. "It is in areas of materials that are compounded with fibers and fillers."
For example, the company has seen growth in other areas, like compounding plastic with natural fibers, including kenaf. These compounds are used in some automotive applications.
The company historically hasn't targeted the WPC market, but it is seeing new opportunities arise. "We are working on a couple of companies at the present moment," he said.
Bendfeldt said MAS extruders are particularly well-suited to the WPC market. "The MAS extruder has distinct advantages that allow a customer to skip a pre-compounding process," Bendfeldt said. "The MAS extruder is ideally suited for the composite lumber processing due to the conical co-rotating design. It allows the compounding of all needed ingredients and processing to a finished profile in just one step, eliminating the need of precompounding."
MAS extruders' new conical technology combines the benefits of conical extruders with those of parallel co-rotating twin-screw extruders. In comparison to conventional extruders, the conical design offers substantially higher filling volumes at the material intake, Bendfeldt said. This results in a higher screw filling level, which gives the greatest possible output with comparatively high pressure ratios and low melt temperatures.
Large screw shafts paired with strong back-pressure bearings result in a robust design with a long service life. The design efficiently compounds and processes wood and natural fiber plastic composites, according to the company.
Entek
Entek, a Lebanon, Ore., producer of twin-screw co-rotating extruders, recently introduced a new software program for customers to quickly and easily design screw and barrel layouts for specific applications, including plastic lumber. It gives customers a tool for visualizing their screw and barrel layouts, according to the company.
Built-in features for the new program include:
• Drag-and-drop functionality on all components that customers need to specify, including barrel sections, screws and metallurgy.
• Automatic calculation of remaining space on the screw shafts.
• Safeguards to prevent putting certain screw elements where they do not belong.
• Easier part ordering (complete part numbers are furnished within the program).
• The ability to export options to an Excel file once design is complete.
"This new program is something that will provide great value to our customers," said Linda Campbell, Entek's director of sales. "It will make their lives easier by giving them the ability to specify, and provide a drawing of, exactly what they need for their applications."
Bruce Geiselman, correspondent
Contact:
Davis-Standard LLC, 860-599-1010, www.davis-standard.com
Milacron LLC, 513-536-2000, www.milacron.com
eFactor3 LLC, 704-944-3232, www.efactor3.com
Entek, 541-259-1068, www.entek.com
Bruce Geiselman
Senior Staff Reporter Bruce Geiselman covers extrusion, blow molding, additive manufacturing, automation and end markets including automotive and packaging. He also writes features, including In Other Words and Problem Solved, for Plastics Machinery & Manufacturing, Plastics Recycling and The Journal of Blow Molding. He has extensive experience in daily and magazine journalism.
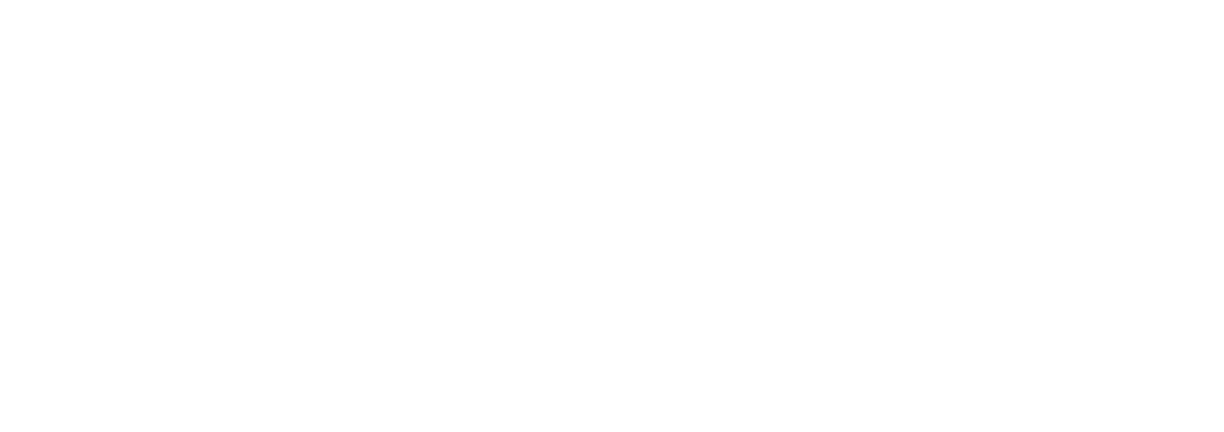