Downstream equipment suppliers push technology to meet WPC needs
Customers are beginning to demand even better-performing WPC lumber products that exhibit characteristics such as greater sturdiness, durability and weather-resistance. Downstream equipment suppliers are responding with technologies that can more efficiently move, cool, measure and cut these boards.
"Everything we sell for plastic lumber is bigger and beefier because of the increased process requirements of the products being produced," said Robert Yore, downstream extrusion product manager for Conair Group, Cranberry Township, Pa.
Conair Group
Conair continually develops new products to meet the needs of its clients that manufacture these profiles, Yore said.
"Every lumber producer has their own approach to making a good product, so about 80 percent of the equipment we supply is customized to meet the specific application requirements," he said. "Instead of using heated embossing rolls, for example, some companies prefer to run them through heat tunnels, which we supply, to soften the surface before embossing them with a wood grain or other texture," he said.
As an example of newly developed equipment, Conair pointed to a custom line of equipment the company built late last year for a client. The client extrudes these boards using a twin-screw extruder and a die that splits the melt into two streams, which required an extra-wide cooling tank and downstream equipment for the side-by-side product streams. The customer had specific requirements for the positioning of the side-by-side equipment.
After exiting the die, the two planks pass through a calibration table and into a Model PCT123020D spray-cooling tank, which uses a high-pressure blast of tiny water droplets to cool them.
After they exit the tank, the boards are taken up by the model CP10100D cleated puller. The cylinders overhead provide downward pressure to grip the part while applying more than 10,000 pounds of pulling force to draw the extruded material down the line. All the downstream pieces of equipment, including the puller beams, operate independently to allow the units to compensate for any inconsistencies between the flow rates of the two product streams.
Next, the boards enter the Model TS524UPD traveling table saw, where twin 18-inch circular saw blades ascend from beneath the table to cut the planks as the table moves along at the same speed as the lumber.
Novatec Inc.
Novatec Inc., Baltimore, has released an upgrade for the control of its NS-6 Up-Cut Servo Traveling Extrusion Saw control.
The saw now comes equipped with a standard servomotor. Previously, this feature had been sold in the industry as an expensive option and was purchased only by those requiring tight tolerances. This standardization is offered at a dramatically lower cost while providing improved accuracy of the saw, according to the company.
"The old-style pneumatic saws typically could be expected to hold plus or minus a quarter of an inch tolerance," said Rich Vester, Novatec's downstream extrusion product sales manager. "Today's servo table saws are inherently more accurate. Novatec guarantees plus or minus 1/32 of an inch or better. … The waste savings can be huge."
Also, in the latest release of the saw, Novatec included an upgraded Siemens PLC, along with a color touch-screen HMI.
"The features of this control allow us to give the customer full latitude of access within the machine to everything except the baseline program itself," Vester said. "The customer can input the right security code number, and access the setup pages, giving them the ability to tweak the machine settings as needed for their process."
Using the touch screen, operators can set the cut length, determine the number of pieces cut, or select a saved program or recipe. Also, with the push of a button, an operator can cut part of a board to salvage some of it if a quality-control issue arises. This setting can reduce material and labor waste.
The Siemens system also uses SD memory cards to allow for the easy backup and transfer of program information.
ESI-Extrusion Services Inc.
ESI-Extrusion Services Inc.'s most recent upgrade to its embossers is the addition of servo-positioning technology, which the Akron, Ohio, company said resulted in positive feedback. It is now looking at adding a laser-monitoring system to further improve pattern consistency.
Increasingly, WPC lumber manufacturers want the machine operator to be able to adjust the position of the roll, including the gap and pitch, for boards that are not perfectly flat. ESI has worked with customers to achieve this, granting manufacturers — and machine operators — more control over the quality of the product they produce. ESI has worked with customers to develop user-friendly, recipe-driven embossing systems that allow for operational flexibility and repeatable results.
Servomotors allow more precise control of the process, including linear positioning between the upper and lower rolls, resulting in more consistent and repeatable embossing patterns.
As an option, ESI-Extrusion Services is considering offering laser sensors that monitor board thickness and automatically correct roll gap or pitch. The product still is in the concept stage.
CDS Inc.
Extrusion equipment provider CDS Inc., Lachine, Quebec, this year introduced a new calibration table that reduces the energy consumption of cooling and vacuum systems. It also includes fully integrated air-conditioning units for electrical panels.
"It's a calibration table with energy-efficient capabilities," said Antonio Pecora, VP of sales Pecora said. The new system consumes about half the power of its predecessor.
The calibration table includes a touch screen that displays energy use and alarm and diagnostic features.
The innovation comes amid a favorable market for CDS.
"The last year has been very good for us," Pecora said. "We have seen an uptick in our business. Our sales figures have increased coming off the recession."
Also, late last year, CDS updated its belted puller series to offer a new feature: a reactive, self-pivoting and self-adjusting top-beam conveyor arm.
During the startup of the extrusion process, WPC lumber can be uneven, making it difficult to pull through the extrusion line without complications such as slippage, crushing and machinery damage.
The self-adjusting top-beam conveyor arm allows the puller to automatically adjust for any variations in product thickness at startup, Pecora said.
Bruce Geiselman, correspondent
Contact:
Conair Group, 724-584-5500, www.conairgroup.com
Novatec Inc., 410-789-4811, www.novatec.com
ESI-Extrusion Services Inc., 330-434-1861, www.esi-extrusion.com
CDS Inc., 514-633-5933, www.cdsmachines.com
Bruce Geiselman
Senior Staff Reporter Bruce Geiselman covers extrusion, blow molding, additive manufacturing, automation and end markets including automotive and packaging. He also writes features, including In Other Words and Problem Solved, for Plastics Machinery & Manufacturing, Plastics Recycling and The Journal of Blow Molding. He has extensive experience in daily and magazine journalism.
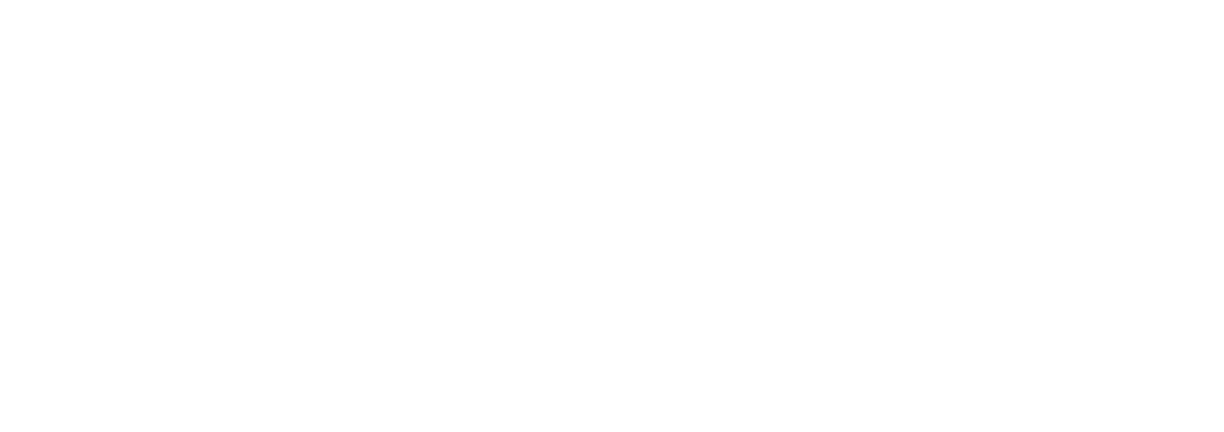