Special Report: Programmability, lower costs make robots ideal for complex tasks
Six-axis, articulated-arm robots are gaining interest from injection molders for operations that involve complex post-molding tasks. Until recently, many molders have considered six-axis robots out of reach because of higher costs or difficulty in programming, but that is changing, according to robot manufacturers.
Six-axis, articulated-arm robots will see more use for large injection molded parts, such as in the automotive, appliance and home furnishing industries, said Dean Elkins, senior GM of sales for the eastern U.S. for Yaskawa America Inc.'s Motoman Robotics Division, Miamisburg, Ohio. He noted that the robots are especially effective in extracting complex parts such as automotive instrument panels. "You can program the robot to peel the part, rather than just pull it off in a linear fashion," he said.
Prices, while still higher than for Cartesian industrial robots, have come down significantly. "The robots today are 30 percent less than they were in the mid-1990s," Elkins said. As the pricing barrier has gradually fallen away, more injection molders are considering six-axis, articulated-arm robots for complex tasks and applications that require flexibility.
SIMPLER CONTROLS, TIGHTER INTEGRATION
In the controls arena, Elkins said he sees more use of PLCs. Although PLCs often are used in linear robots for part extraction, the use of PLCs with six-axis robots is less common, he said. He noted that Yaskawa Motoman's PLC-based MLX200 controller has simplified programming. "If you are going to use a PLC controller, quite often the same people who are programming the injection molding machine can now program the robot," he said.
Several other robot manufacturers, in some cases working with injection molding machine manufacturers, have also made significant progress in simplifying controls.
Engel Austria GmbH, Schwertberg, has made strides in this area. According to Walter Aumayr, director of automation worldwide for Engel, programmability of robot controls has been a top concern for customers. "The big issue for all of our customers is that they needed special skills to program a six-axis robot," he said.
Engel has simplified the programming of its HMI for its easix six-axis robots. Programming requires no special skills; in fact, easix uses the same HMI as the company's linear robots. Engel has developed a common controls interface to work with robots manufactured by Stäubli Corp. and, since last year, Kuka Robotics Corp. , Aumayr said.
Arburg GmbH + Co. KG, Lossburg, Germany, has integrated its intuitive, graphics-oriented Selogica user interface with robots manufactured by Kuka. Matthias Lang, senior sales manager for automation, said the effort has significantly simplified programming. In addition, once the robotic program has been created, all robotic actions can be managed from the injection molding machine's control panel, he said.
According to Arburg, no special programing knowledge is needed, even for complex sequences. Robotic sequences can be created quickly and easily with graphical symbols, including functions such as moving to start positions or separating good parts from rejects. Users can change robotic sequences independently at any time.
The easier-to-program six-axis robots can result in significant processing advantages for the molder. An interesting example is a turnkey system using a six-axis robot that Arburg demonstrated at the Fakuma 2014 trade fair. The company built the system around a hydraulic Allrounder 470 S press to demonstrate particle foam injection molding. An Agilus six-axis robot manufactured by Kuka was equipped with a Selogica control interface and moved in the traverse direction to the press along an additional linear axis. It picked up the part and inserted it into the mold. The arrangement allowed more dynamic movements and fast entry into the mold, resulting in short cycle times and higher productivity, the company said.
Similarly, TM Robotics (Americas) Inc., Elk Grove Village, Ill., a unit of Toshiba Machine Industrial Robots, has been working on controls technology for tighter integration with Toshiba injection molding machines. The key, according to Ryan Guthrie, executive VP of TM Robotics, is that both the robots and the injection molding machines share the same programming language. Guthrie said that by the first quarter of next year, TM Robotics will launch a tightly integrated robot and injection molding machine package that will function as one seamless machine. The integrated robot and injection press will also have a smaller footprint, he added.
Guthrie said an example of the tightly integrated setup between robot and injection press will be on display at the K show in October. TM Robotics will demonstrate two six-axis robots on an injection molding machine. One robot, a TV1000, will do parts removal; the other, a TVL700, will do assembly work.
The TV1000 has an arm length of about 3 feet and a maximum payload of 11 pounds. It will remove parts from a family mold and feed them to the TVL700, which will assemble the components into the final model. Guthrie describes the TVL700 as a lightweight, energy-efficient machine that is designed for operating in tight spaces. It has an arm length of 2 feet, 4 inches, a maximum payload of 8.8 pounds and a standard cycle time of 0.4 seconds.
According to Guthrie, TM Robotics streamlined its procurement process when it designed the robots in the TVL series. As a result, the TVL robots cost 15 to 20 percent less than the company's standard robots. Six-axis, articulated-arm robots such as the TVL series show their value where there are quality issues, he said. "By having a dexterous, fully functional six-axis arm, we can be doing assembly work, family-mold kind of work, gate cutting and sprue cutting without taking up extra floor space," he said.
SUPPLIERS ADD NEW MODELS, EXTEND CAPABILITIES
Yaskawa's Elkins acknowledges that six-axis, articulated-arm robots are not a cost-effective solution for mere part extraction. But for secondary operations such as trimming, grinding or assembly, they can be of real value.
He pointed to two examples where six-axis robots are providing more efficient post-molding tasks. One is the use of machine vision, to guarantee the right orientation of the part. The other is the use of ultrasonic trimming when trimming or deflashing is required. Ultrasonic trimming is a cleaner process that does not use consumables, and it provides improved cut quality, requires less floor space and produces less noise and waste compared to traditional methods, he said.
Yaskawa has recently extended its six-axis, articulated-arm series of robots with the Motoman GP8 model. Elkins said the robot has a slender profile and is a high-speed machine. It is suited for small- and medium-tonnage injection molding machines.
In addition, ABB Inc., Auburn Hills, Mich., has recently introduced the IRB 1660ID robot. It has a rigid upper arm with a reach of 5 feet and a payload of 13 pounds. It has a compact footprint that allows for efficient work cell layouts, according to the company.
Laxmi Musunur, the director of the picking, packing and palletizing segment for Fanuc America Corp., Rochester Hills, Mich., said six-axis, articulated-arm robots are gradually gaining capabilities, which will expand their use in plastics processing. He said they are becoming more sophisticated, which will make them more valuable for post-molding operations. He noted that robots are now capable of controlling the force applied to parts in such operations as degating, deflashing or drilling holes. Controlling the force, coupled with the use of machine vision, can improve the quality of post-molding operations significantly, he said.
As for future developments, Musunur said self-learning features that are now being applied to robotics in other industries will eventually make an impact in plastics. One example: Fanuc has developed a learning vibration control (LVC) technology that allows a robot to learn its vibration characteristics for higher accelerations and speeds. LVC technology is now used in automotive spot welding, but Musunur said it is only a matter of time before it finds its way into plastics molding.
"We see future applications of self learning in the plastics industry," he said. "But first we must take baby steps. It's an evolution."
John DeGaspari, senior correspondent
Contact:
ABB Inc., 248-391-9000, www.abb.com/robotics
Arburg Inc., 860-667-6500, www.arburg.us
Engel Machinery Inc., 717-764-6818, www.engelglobal.com/us
Fanuc America Corp., 888-326-8287, www.fanucamerica.com
Kuka Robotics Corp., 866-873-5852, www.kuka-robotics.com
Stäubli Corp., 864-486-5421, www.staubli.com
TM Robotics (Americas) Inc., 847-709-7308, www.tmrobotics.com
Yaskawa America Inc., Motoman Robotics Division 937-847-6200, www.motoman.com
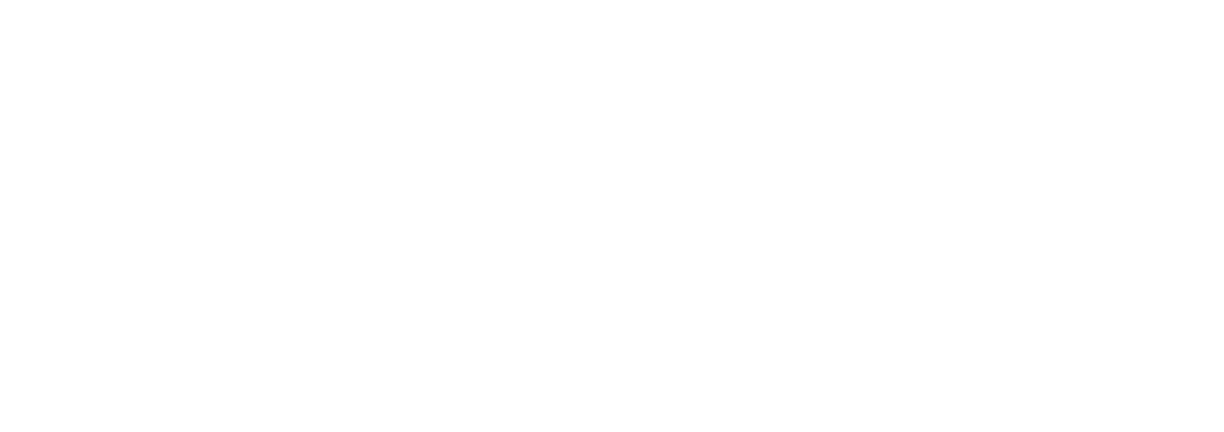