Special Report: Unique integration of robotic, nonrobotic cells on rise
Custom automation solutions that utilize multi-axis robots, pick-and-place units and Scara robots are often overlooked but their use is growing. When automation system integrators and robotic suppliers create these one-of-a-kind automation cells, efficiency is the name of the game.
Automation integrators use simulation tools to build and test virtual automation cells including robots and customized equipment selected by their customers. Iterations of the virtual systems account for payloads, pre-existing equipment, robot reach, cycle times and configuration/layout of the cell in the plant. Versatility is also a major consideration.
Other than the robot itself, the integrated work cell can include end-of-arm tooling (EOAT), conveyors, robot guarding and other auxiliary equipment. In addition, users might have the option of operating the automation cell through customized controls or through controls provided either with the robot or molding machine.
MULTI-ROBOT AUTOMATION CELLS
Robotic Automation Systems (RAS), Waunakee, Wis., is a certified automation integrator that uses several robot suppliers, including Fanuc, Wemo, Hahn Automation, Epson Robotics and ABB. RAS' automation cells range from simple to sophisticated and cost from $5,000 to $1 million.
RAS designs the entire turnkey system: conveyors; guarding, inspection or detection equipment; EOAT; programming software; and more, said President Craig Tormoen.
"We design and build to spec each component that goes into an automation system, including the end effectors for the press-tending robot or tables, fixtures and pick-and-place stations for the support robot. Because we sell many types and brands of robots, we can select the ideal robot type to meet a customer's cycle-time constraints, payload constraints or [robot] reach constraints, and we can determine the appropriate level of functionality for the robot, the end-of-arm tooling and for devices in the automation cell," Tormoen said.
RAS can equip each device in the automation system with an Ethernet-ready PLC and HMI. The company can also link the automation to the control of the press-tending robot or to the processing machine. The press-side unit is linked to the machine via a Euromap 67 interface. Communication confirms that an action has taken place, adds a level of traceability to the production line and protects both the robot and the mold, Tormoen said.
For one customer, RAS created three versions of an automation cell designed for use in the production of a tight-tolerance, insert-molded part involving automotive electrical connectors.
In these applications, a six-axis Fanuc robot places three different types of tiny inserts in a specific order and orientation into eight pre-stage nests. A second, six-axis Fanuc robot picks up the eight sets of inserts and transfers them to the mold using a specialized end effector from RAS.
The press-tending, six-axis Fanuc robot in the automation cell incorporates an integrated Fanuc IR vision system, which is used to compensate for thermal expansion of the robot during operation. "The robot does a micro correction every cycle during the last 6 inches of travel into the mold as the thermal expansion of the robot has exceeded the allowable tolerance of loading the inserts," Tormoen said. The vision system can also be repurposed for part inspection.
RAS used a coordinate-measuring machine to manufacture the pre-stage nests. "We needed to know the true X and Y position of each insert to ensure proper alignment to the mold," Tormoen said. The EOAT is designed with two docking bushings that engage during insert pickup to prevent or correct for potential misalignment of as little as 0.005 inch.
The exact design of an automation cell de- pends on several factors, including cost, plant layout and available equipment. In one layout designed for the automotive electrical connector molder, RAS designed a rotary three-station table with three sets of pre-stage nests. The first six-axis robot picks up the different pre-stamped inserts that are bowl-fed and oriented with that device. The press-tending six-axis robot and EOAT pick up the full complement of inserts.
Automation cells are increasingly incorporating the EOAT with servo motors, which are replacing pneumatic drives. Applications where inserts are placed inside the tool at different planes or depths, and those that require twisting or linear motions, are the earliest candidates.
However, incorporating servo motors into the EOAT means more of the maximum payload of the robot is committed to handling the weight of the tool.
INTEGRATOR OFFERS PRE-ENGINEERED AND 6-AXIS SOLUTIONS
CIM Systems Inc., Noblesville, Ind., works as a preferred integrator with six-axis robot maker ABB Inc., Auburn Hills, Mich. CIM Systems President Dave Fox said numerous factors might prompt a company to transition from a manual operation to an automated operation. "Pieces of equipment or duties [that can result in] injuries, or where repetitive motion can cause fatigue, are candidates for automation," he said.
He added that molders who have top-mounted or side-entry three-, four- or five-axis robots often realize that they could add more value to their process by updating to a six-axis unit.
"Some customers who have purchased a three-axis gantry-style unit use it to keep the operator out of the molding area to minimize mold open time and get more products out. But many parts are dropped onto a conveyor for transport to a downstream value-added device. Some now are implementing a six-axis robot in place of the gantry unit, which allows them to incorporate the downstream step into the robot operation," Fox said.
An emerging area in automation integration where an ABB six-axis robot can distinguish itself is force control. "Downstream operations like assembly, polishing or grinding, where an even pressure needs to be applied for a given amount of time and at a specific point of a part, is a capability for six-axis robotics," Fox said.
In addition to software programs that enable a robot to provide precise force, ABB developed SoftMove software for part-demolding applications in which the robot can contact the part before the ejector pin fires. Here, the program operates the robot like a spring as the ejector actuates, allowing for a secure transfer of the part from the core of the mold to the robot.
ABB's SafeMove program can minimize the need for fencing around a product. "The robot does not move beyond the established perimeter, so the fencing can be brought back tighter to the molding machine, saving space on the plant floor," Fox said. CIM Systems typically ties together the safety systems for the molding machine, the robot and the automation.
CIM Systems offers a line of pre-engineered automation cells in addition to custom automation configurations for inspection, dispensing, deburring and palletizing. "These units would not be tied to an injection press or blow molding unit where they would unload parts. They are typically fed parts," Fox said.
The biggest development in pre-engineered systems is how the parts are presented to the automation cell. Previously, a rotary table with two sets of fixtures would be required, with the molding machine and robot on one end and the pre-engineered system on the other end. The robot would pick and place the parts onto a fixture like a rotary table, which would then rotate into an automation cell for the next task. Then the table would rotate finished parts out of the cell back to the robot.
CIM Systems now offers a pre-engineered, pneumatic, shuttle-sliding system as an option. Fixtures on each of the slides shuttle between the molding cell and the automation cell in an alternating pattern. When one slide and fixture is accepting the demolded part from the robot, the fixture on the other slide is in the automation cell. This configuration can reduce cycle time and minimize robot idle time.
EOAT ADVANCES IN FOCUS
Yushin America Inc., Cranston, R.I., builds custom EOAT, downstream automation, conveyors and safety guarding for use with its three-, four- and five-axis servo and hybrid servo-pneumatic robots, said Ron Bryant, manager of equipment sales.
A Yushin customer with a part-labeling application had initially planned to place four or six parts each cycle onto a transfer conveyor that would orient the parts. A vision system would verify part orientation, apply an adhesive label using a support robot, and box the labeled parts using another robot. The molder needed to apply labels with different information for different lots of parts, which is why it planned to incorporate the extensive multi-robot automation cell.
Instead, Yushin created custom EOAT with a special vacuum-cup design to pick up and orient the labels. It also created a pneumatic system to apply the label in the exact position on the part in-mold before the robot removed it. "We combined all of the post-mold handling and labeling operations into one EOAT design, saving real estate on the shop floor while eliminating the vision system and the transfer system," Bryant said.
Sometimes, the construction of a table or other structure can facilitate the movement of a part out of one injection mold and into another, providing further efficiency to secondary operations like part overmolding.
"There are times when that feature can be incorporated into the safety guarding already erected around the robot, so the user does not require additional floor space. The legs of the table or structure may already exist as part of the safety guarding. The risk to the molder in applying the technology in new ways is low because capability of the various pieces of equipment in place is already proven. It is the application that is new," Bryant said.
MOVING AWAY FROM MANUAL HANDLING
Satoshi Yamamuro, VP of sales for robot maker Sailor Automation Inc., Placentia, Calif., said U.S. molders with applications for medical and food industry products are showing increased interest in EOAT and automation technology.
Last year, the company developed its first automated bagging machine designed to handle petri dishes. "A customer used to manually place stacks of lids and containers into a bag, close the package with an impulse-sealing device, then place it into a box. We developed a machine that automates that process," Yamamuro said. The unit can handle different petri dish sizes by changing the sealing and other mechanical devices.
The petri dish and lid are molded in a single press with a tandem mold. Sailor's five-axis RZ Sigma II robot is used in conjunction with the tandem tool and the new bagging system. Yamamuro said the automation can be run from a stand-alone control, or Sailor can design a special display screen for the automation that corresponds and synchronizes with the robot.
New automation from Sailor helped a manufacturer of molded pipettes produce parts without errors from manual handling. Previously, workers placed several hundred pipettes into each container by hand, a time-consuming process that required precise skills.
Sailor also recently developed post-mold automation for a food company that required the molded container to be opened and closed prior to being stacked and packed. Yamamuro said if required, these actions could be incorporated into the automation cell, along with inspection.
CBW DEBUTS AUTOMATION SYSTEM
CBW Automation, Fort Collins, Colo., will introduce its new Advantage series automation system at the K show. There, it will be paired with a Ferromatik 280 multicomponent hybrid injection molding machine with co-injection capability. The Milacron LLC, Cincinnati, booth will feature the systems working together in the production of Klear Cans, the plastic cans that are being marketed to replace metal cans.
Christopher Kujawa, applications engineer with CBW, said the Advantage series' key innovation is its modularity. The series was designed to minimize the cost and downtime for repurposing. For example, it uses a standardized base and frame. CBW has a new lean manufacturing strategy through which it has standardized certain components of its automation systems to reduce lead times.
"The goal of the Advantage is to have a robot that can be used on multiple different products during its lifespan," he said. During the K show, CBW will showcase the in-mold labeling, single- face version of the Advantage line. The robot — a magazine-fed, four-cavity system — will be fully integrated to perform with 100 percent inline part inspection of the co-injected ethylene vinyl alcohol (EVOH) barrier within the can.
The system will use suction cup retrieval instead of high-flow vacuum blowers. It will employ several features to support the parts during high-speed retrieval.
"This hybrid design ensures that the part does not fall from the suction cup during capture and retrieval," Kujawa said. Suction cups were chosen for their adaptability. They can easily be repositioned to adjust for differences in part sizes between products.
"This allows for a flexibility not seen on other systems," he said. "High-flow vacuum blowers still have advantages and will still be offered on CBW's more dedicated, high-speed retrieval systems such as the SSE and TSE."
Pricing will depend upon customers' specifications. This Advantage series has a lower price through standardization. However, the robot's modularity allows for upgrades and unique functions to be added based on customer needs, Kujawa said.
Mikell Knights, senior correspondent
Contact:
ABB Inc., 248-391-9000, www.abb.com/robotics
CBW Automation, 970-229-9500, www.cbwautomation.com
CIM Systems Inc., 317-773-5600, www.cimrobotics.com
Robotic Automation Systems, 608-849-0880, www.roboticautomationsystems.com
Sailor Automation Inc., 714-528-7711, www.sailorautomation.com
Yushin America Inc., 401-463-1800, www.yushinamerica.com
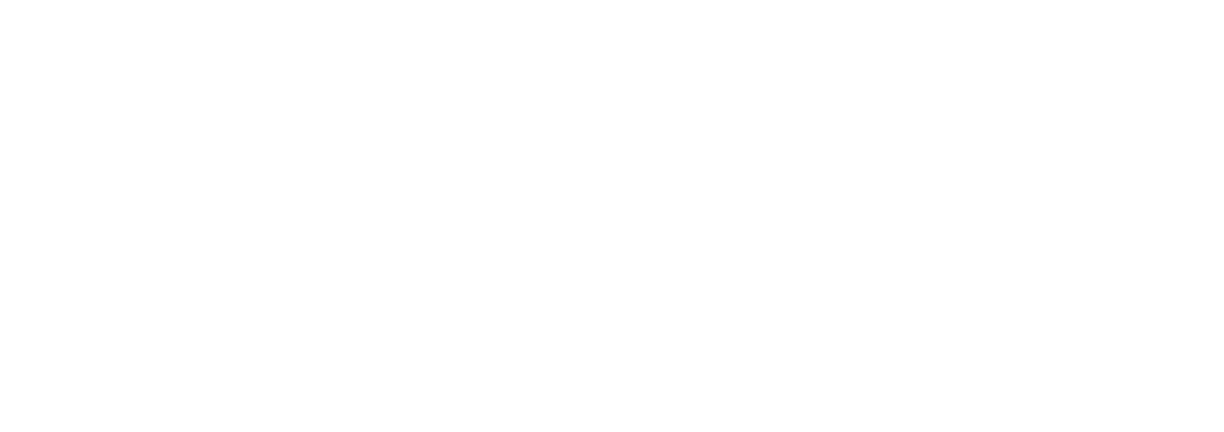