Injection molding machinery suppliers debuted new products during Taipei Plas International Plastics & Rubber Industry Show held Aug. 12-16 in Taipei, Taiwan.
FCS introduces HE Series
Fu Chun Shin Machinery Manufacture Co. Ltd. (FCS), Tainan, Taiwan, debuted the first model in a new line of all-electric horizontal toggle-clamp machines.
The new HE series is designed with five servo motors that govern the primary motions of the injection press, with servo belt-driven ball screws for recovery and plasticizing and direct-drive servo motors for carriage movement, injection, clamping and ejection, said Hank Wu, the company's Taiwan-based area manager. The servo-motor technology is sourced from Phase Motion Control, Genoa, Italy. The model line features a Keba controller for ease of programming and operation.
FCS, represented in North America by Maruka USA, Lee's Summit, Mo., also unveiled a new mold-cavity, pressure-based machine control system on the HE model. As part of the system, sensors placed at the end of fill in each of the tool's cavities feed pressure data back to the machine control. The system's new Intelligent Control adjusts the mold temperature in a particular cavity if it detects an issue.
As many as eight sensors (one per cavity) can be used. The system, which uses sensors from Priamus System Technologies AG, Schaffhausen, Switzerland, also sends a signal to the robot to divert the imperfect part. Once activated, Intelligent Control takes about 50 molding cycles to narrow the range between the upper and lower limits of acceptable part parameters, which improves molding quality. The system adjusts the mold temperature continuously.
At Taipei Plas, FCS exhibited an HE-300 machine featuring 331 tons of clamping force, Wu said. A 496-ton unit is in development.
In addition, FCS updated its LM series of two-platen machines, replacing the fixed-displacement pump hydraulic system previously used for plasticizing and injection with its new SV line of servo drive injection units. Wu said plasticizing and injection are done by separate servo motors that are connected to the machine's drive gearbox rather than connected to a belt and ball screw.
Response time is as short as 40 milliseconds with injection speeds up to 250mm per second. Dry cycle time is approximately 4.2 seconds with the updated control and optimized hydraulic circuit, compared with 6 seconds with the prior design, Wu said. Position repeatability is within 0.5mm, making the SV unit twice as accurate as the fixed-displacement hydraulic unit. The switch to the servo drives produces energy savings of up to 70 percent.
The LM series has a Keba touch panel control with a 22-inch screen, an update from the previous 12-inch Keba panel that had no touch screen. With the updates, FCS has increased the LM line's price about 10 percent.
HPM parent company introduces all-electric series
Guangdong Yizumi Precision Machinery Co. Ltd., Foshan City, China, displayed its FE series of all-electric horizontal toggle-clamp machines. The line comprises five models and 12 injection unit sizes, said Samson Chen, pre-sale engineer of the all-electric molding machine department at Yizumi. In the United States, it is marketed as the HSE series, said John Beary, the president of HPM North America Corp., Marion, Ohio, which is owned by Yizumi. Clamping forces range from 65 to 285 tons.
Features include four servo-driven motors that operate belt and ball screws for plasticizing, injection, clamping and ejection. Separate asynchronous motors handle the movement of the injection carriage and the mold adjustment.
According to Beary, the HSE line, which HPM exhibited in beta form at NPE last year, has been upgraded over the last few months. The new features include what Chen calls a negative caster angle for the five-point toggle clamp system. In this system, the links of the toggle move downward only during platen open and platen close movements. This ensures smooth clamping movement.
The machines also have a special three-platen configuration in the clamping unit where fixed platens are used to support a tie-bar system that does not come into contact with the moving middle platen, which is connected to the toggle. This reduces friction during mold movements and eliminates grease on the tie bars. The ends of the tie bars enter slots on the moving platen but maintain clearance of 0.04mm.
The movable platen rides on low-friction linear rails. The design, in concert with the toggle clamp, provides a platen parallelism during molding and concentrates clamping forces uniformly, Chen said.
The design also allows for greater tie-bar spacing between the tie bars, which ranges from about 14 inches by 12.5 inches to about 26 inches by 24 inches, depending on the model. The machines use a Keba controller with a 12-inch touch screen.
Mikell Knights, senior correspondent
Contact:
Maruka USA, 816-524-1811, www.marukausa.com
HPM North America Corp., 740-382-5600, www.hpmmachinery.com
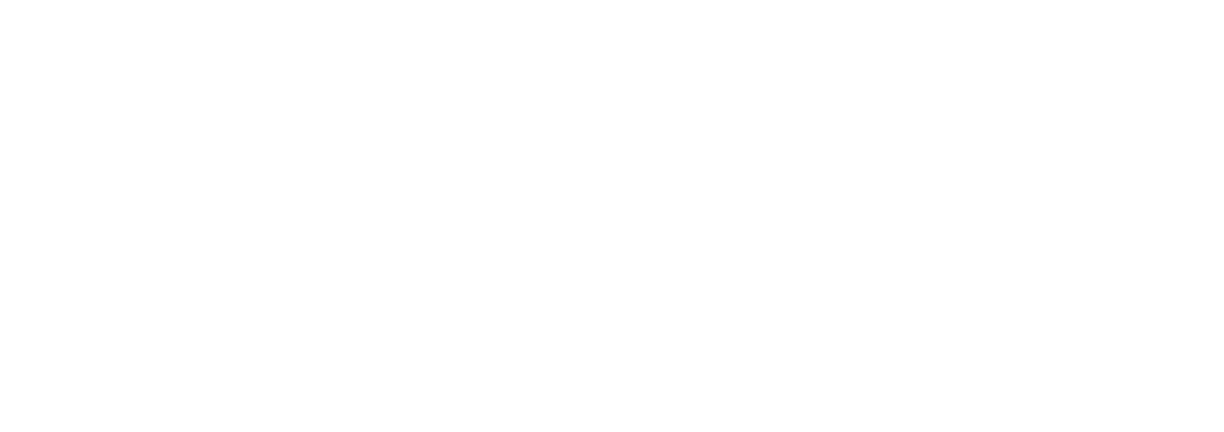