Twin-sheet thermoforming is a rapidly growing field in plastics manufacturing.
"More machines in the past three years are doing twin sheet than ever before," said Michael Alongi, sales director for Maac Machinery Corp., Carol Stream, Ill.
Many of the new markets are in the automotive industry as car makers work to meet fuel-efficiency standards. Processes are now available to accommodate many materials with starting sheet thicknesses as thin as 0.03 inch and going up to 0.75 inch, Alongi said.
Twin-sheet thermoforming involves heating two extruded plastic sheets simultaneously with separate molds on the top and bottom platens. The heated sheets then are brought together under high platen pressures and bonded. The result is a single product with hollow areas.
Depending on the application, other materials can be inserted into the void between the two molds, including wood, aluminum, steel and foam. More advanced applications can involve inserting tracking or measuring devices into the void, for example, to sense how much fuel is in a tank.
Typical twin-sheet applications include air ducts, fuel tanks, kayaks, medical devices, pallets, portable toilets, toys and transportation-related products.
MAAC MACHINERY CORP.
Maac makes a number of twin-sheet machine models. They include the R3PT rotary, three-station pressure former, and the R4DPT rotary, four-station double-oven pressure former.
In the past year, Maac has made several upgrades to its rotary twin-sheet machines to increase speed. All machine movements and machine control sequencing have been redesigned to reduce cycle times and some typical processing delays, Alongi said. The company continues to make improvements.
"Every machine we build, we do a little better and faster," he said. "With the increased speeds and programming, it has pushed the twin-sheet process into new markets for thinner materials and for materials that typically did not retain enough heat to properly bond with one another in the process.
"This has opened up markets to make twin-sheet parts lighter and more cost-effective by using less material, yet with higher strengths," he said.
It also opened up markets for foam-based materials, acrylics and PCs that traditionally cool quickly and are difficult to bond.
Maac's recent twin-sheet upgrades also include new articulating clamp frames that were redesigned within the past two months to allow for a reduction in sheet size. Custom clamp frames allow the loading of smaller sheets that are stretched prior to forming, which helps when materials with low-melt strengths sag more than desired. Also, traditional clamp frames are fixed or stationary, whereas articulating frames can move.
A third motion plug assist is being built into an increasing number of twin-sheet machines, Alongi said.
"Where further, more precise plug assists are needed, we are actually integrating a third movement/drive system within the machine's platen, which allows us to move loose pieces within a mold to plug the opposing mold half."
Maac reports that an increasing number of its customers are asking for automatic inserters due to the growing demand for hollow parts.
"Many clients are seeking ways to safely insert items in between the upper and lower mold halves," Alongi said. "This is requiring the machinery to have further automation with pick-and-place systems that will transfer wood, metal or even electronics into the part prior to the bonding."
CANNON USA
Since March, Cannon Group, an Italian manufacturer of industrial equipment, has introduced two new twin-sheet thermoforming machines — the Twin Crea 0604 and the Crea 2515TS.
The Twin Crea 0604 is designed for high-speed, high-precision, extremely repeatable production. It makes small parts that require a high degree of accuracy. The aeronautics and space, automotive, medical and sports industries could benefit from this technology, according to the company.
For example, the automotive or medical equipment industries could use it to manufacture bladders that would hold a high air pressure at an elevated temperature, said Zvi Rapaport, a plastics technology senior specialist for Cannon Ergos, one of the company's divisions.
When the upper and lower molds come together on this thermoforming machine, the closing force can exceed 30 tons.
"The machine has a very, very high requirement for precision and repeatability," Rapaport said. "The tolerances on the platens' parallelism are plus or minus 0.002 of an inch."
He added that the heating control system for the plastic sheets is highly accurate, as well.
"As far as the heating control system, that is the heart of this machine," Rapaport said.
The temperature of the sheet, cycle to cycle, is within 3.6 degrees Fahrenheit. A closed-loop heating control system monitors the output of heaters in real time. The heaters are divided into five zones per sheet to ensure each zone follows the target temperature throughout the process.
"The tricky part is, each sheet can be a different thickness, delivered at different times in the production cycle, so the control compensates by using less or more power as the sheet is heating up," Rapaport said.
Another important feature is the ability to place inserts automatically inside of the part. A robot can deliver the inserts to be bonded internally or externally with the part surface.
Cannon's other new unit is the 2515TS, which features a centrally located robot. The robot moves the sheets between all of the stations from pallets to the conveyor for finished parts.
"Imagine, along the whole line there is no need for manual labor in producing the part," Rapaport said.
The other new feature is an "intelligent sag control system" that prevents sheets from sagging and stretching as they are heated.
During the heating process, air is blown against the upper and lower sheets to combat gravity and prevent the sheets from sagging. If sheets sag, they get closer to the heater and stretch even more. The "pillows of air" result in better heat control and more uniform parts, Rapaport said.
The Crea 2515TS is suitable for making larger and thicker parts including twin-sheet pallets, doors and panels for portable toilets, boats and kayaks.
GEISS AG
Geiss AG, Sesslach, Germany, manufactures twin-sheet, roll-fed, zero-gravity, closed-chamber thermoforming machines that use a minimal amount of air pressure to prevent sagging of the plastic sheets during heating.
Last year, the company unveiled its T10 twin-sheet thermoforming machine. The new unit uses servo-driven systems for the clamp frame, mold table, plug-assist and heater movements, said Michael Roche, GM of Geiss LLC, Torrington, Conn., the North American distributor for Geiss equipment. The servo systems are faster, more accurate and more energy efficient than the pneumatic systems they replace, and they provide a higher duty cycle and level of process control. The technology will be incorporated in all of the latest generation machines, Roche said.
Within the past nine months, Mergon Corp., Anderson, S.C., an American-based Tier 1 automotive supplier, began using T10 technology to manufacture lightweight foam air ducts for cars made in the U.S., Roche said. The foam ducts replace heavier and more expensive blow-molded air ducts.
"It's super lightweight, and you can [create] complex tubular shapes with twin-sheet thermoforming," Roche said.
Geiss has been making thermoforming equipment since 1957.
ILLIG MASCHINENBAU GMBH & CO. KG
Illig Maschinenbau GmbH & Co. KG, Heilbronn, Germany, recently made several improvements to its Illig UAR 155g, a twin-sheet thermoforming machine that can be used to manufacture foam air ducts for the automotive industry.
The upgrades have increased energy efficiency and production speed, said Gebhard Ruoff, a senior engineer at Illig.
The changes include:
• Adding adjustable metal reflectors to the heating system to reduce energy consumption and allow for more precise heating of the upper and lower sheets.
• Installing shields that close off the heating system to reduce energy consumption during the cooling process.
• Changing the vacuum pump position and cross section to reduce the time it takes for the vacuum to draw sheets into the upper mold.
• Adding a platform on the upper machine frame to allow for easier maintenance.
One of the UAR 155g's major advantages is that, unlike most thermoforming machines, it doesn't require clamp frames. Normally, processors need to change clamp frames when adjusting the size of the parts being manufactured. However, Illig's technology speeds the process by eliminating the need for clamp frame changes, Ruoff said.
Earlier this year, Illig put its third UAR 155g thermoformer in operation at a Spanish automotive supplier, where it makes air ducts from PE foam. The foam ducts are significantly lighter than the traditional blow molded, hard PP ducts, according to Illig. The foam's lower heat conductivity and heat capacity minimized the development of condensation in air ducts after switching off the air-conditioning system.
Bruce Geiselman, correspondent
Contact:
Cannon USA Inc., 724-772-5600, www.cannonusa.com
Geiss LLC, 203-988-9426, www.geiss-ttt.com
Illig LP, 484-639-7124, www.illigusa.com
Maac Machinery Corp., 630-665-1700, www.maacmachinery.com
Bruce Geiselman
Senior Staff Reporter Bruce Geiselman covers extrusion, blow molding, additive manufacturing, automation and end markets including automotive and packaging. He also writes features, including In Other Words and Problem Solved, for Plastics Machinery & Manufacturing, Plastics Recycling and The Journal of Blow Molding. He has extensive experience in daily and magazine journalism.
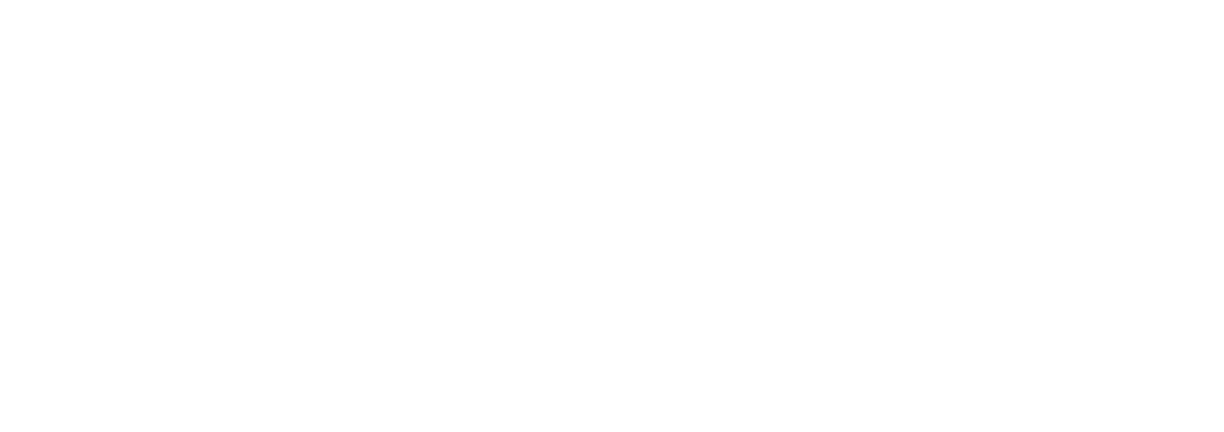