Special Report: Auxiliary feeder capabilities tapped to meet simple and complex jobs
Makers of feeders are adapting their equipment to meet a variety of needs. Suppliers interviewed for these stories shared updates to existing technologies and provided information on their newest products.
Plastic Process Equipment
Plastic Process Equipment Inc., Macedonia, Ohio, is offering its line of TAL stainless-steel vacuum hopper loaders. This equipment has a detachable remote control pad with a 6-foot cord, said sales manager Gary Croy. The line comes in conveying capacities of 150, 450, 660 and 900 pounds per hour. More advanced features include a material shortage alarm, run and alarm lights, stainless-steel hopper and pick-up probe for clean material processing. There also is a pivotal discharge flap with a magnetic level-control switch.
Plastic Process Equipment also has a new line of LV Venturi hopper loaders that operate on compressed air. The loaders are fully automatic, Croy said, with no motors or brushes to replace. They consist of a stainless-steel hopper, base and pick-up probe. They come in conveying capacities of 88, 132 and 400 pounds per hour.
Advanced Auxiliary Equipment
Advanced Auxiliary Equipment (AAE) Inc., Mathews, Va., offers a range of loss-in-weight color feeders from Movacolor B.V., Sneek, Netherlands. The MCBalance and MCTwin gravimetric models are for injection molding and extrusion applications, with the MCTwin designed for feeding two materials at once, typically virgin pellets and regrind. The volumetric Movacolor color feeders are the MC12 and MC12-Micro, which are also suitable for injection molding and extrusion. The MC12-Micro is designed for small extruders and injection molding machines with a feed range of 0.02 to 1 gram per second. Movacolor also offers the MC18-Micro, which has the same features as the MC12-Micro, as well as an integrated hopper loader control and automatic synchronization with the extruder feed.
AAE owner Don Rainville said the MCTWin's control manages the variations in regrind that can be available from the grinder.
"A range of allowable regrind can be set, allowing the feeder to measure the availability of regrind and match the consumption with the availability," Rainville said. "The color proportion to the uncolored virgin material is adjusted as needed to maintain precise control over the color of the end product."
Schenck Process
Schenck Process LLC, Kansas City, Mo., recently introduced its Simplex Flat Bottom, a high-capacity, stainless-steel feeder for materials with light and fluffy characteristics, including chopped PP or PET film for use in extrusion. It includes a bottom-driven vertical agitator and an auxiliary agitator, making it suited for feeding lightweight plastics.
The Simplex FB can be operated as a loss-in-weight or volumetric feeder. When designed as a loss-in-weight feeder, the machine comes with weighing modules that can be placed under the feeder or on the mounting floor.
Different types of feeders require different types of dust-collection systems, often based on hopper volumes, said Tom Symoniak, industry manager for the plastics/chemical industries for Schenck. "Typically with a loss-in-weight feeder what we wind up doing is a nitrogen blanket system, so that there's no possibility of a spark [igniting the dust] when it's nitrogen blanketed."
ACS Group
ACS Group's feeders include volumetric AF additive feeders and its DD Digital Dosing System, which feeds pellet or powder additives. Both are suitable for injection molding, blow molding and extrusion applications. The New Berlin, Wis., company's gravimetric feeders include the AF1000 additive feeders and the GH-F Series.
Feeder customers are increasingly seeking better controls, said Tony Johnson, product manager — material handling. Customers are looking for ease of use and centralized connectivity, regarding both the machine and health monitoring. In addition, the company is facing the challenge of integrating its control platforms with customers' existing auxiliary product controls.
ACS is seeing a greater use of a variety of engineered resins and the desire to incorporate additional powder and liquid materials in their operations. How the diverse new materials interact with equipment such as feeders also needs increasing attention, Johnson said.
Moretto
Moretto SpA, Massanzago, Italy, offers a range of dosing systems, which it says can handle different materials, including granules, dust and flakes, and perform with precision even in the presence of vibrations. The range includes its DPM microdosers and DVM volumetric dosing line. The DVM series is Moretto's basic line for the dosing of masterbatch and additives in granule form. Designed for easy color changes, the DVK Krystal is a dosing unit suitable for masterbatch that can be directly mounted on the processing machine.
The DGM Gravix dosing series features high precision, with a 0.001-percent variance. The models handle a range of capacities, up to 12 tons per hour, and can dose as many as 12 components. And then there's Moretto's loss-in-weight system, which adapts to extrusion production requirements as it feeds resin, additives and colorants. The system, which has been available in the U.S. for about a year, reduces waste, the company said.
Allan Gerlat, correspondent
Contact:
ACS Group, 262-641-8600, www.acscorporate.com
Advanced Auxiliary Equipment (AAE), 804-725-1950, www.dryers-loaders-blenders.com
Moretto USA, 614-541-9696, www.moretto.com/en/
Plastic Process Equipment Inc., 216-367-7000, www.ppe.com
Schenck Process LLC, 816-891-9300, www.schenckprocess.us
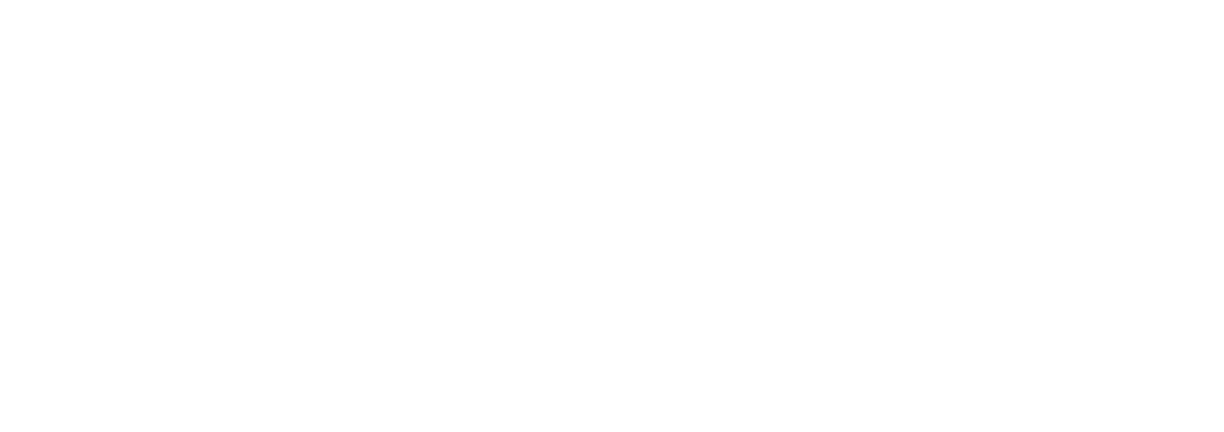