Special Report: Blending systems offering flexibility and speed
Equipment for blending plastic materials continues to evolve. Blender manufacturers are working to integrate machinery communication, keep up with new resins and allow faster product changes.
Maguire Products
Maguire Products Inc., Aston, Pa., last month unveiled a new controller for its popular gravimetric blender. The controller has enhanced data processing capability for better communication with other devices and centralized control of blending and loading.
The Maguire 4088 controller operates with seven times the speed of the Maguire 1212 controller and has eight times the memory. The controller receives data reports from the load cells, which are used to weigh batch ingredients, 45 times more frequently than before, resulting in greater accuracy and faster responses by the controller. Options include a keypad/digital thumb-wheel interface and a new touch screen that is removable for remote operation. The touch screen features built-in software for a conveying system that is used to load multiple materials into a blender, the company said.
The new controller increases the volume, speed and reliability of data transfer, said Frank Kavanagh, VP of sales. "This means that valuable information on the makeup and consumption of the raw materials being metered into the molding or extrusion process can be readily shared with third-party devices via any standard communication protocol, making it possible to integrate Maguire blenders with today's most advanced technologies."
The increased capacity also makes it easier to track down problems and make changes. In addition, the new controller is compatible with previous Maguire blenders and controllers.
The enhanced capacity of the new controller allows the blender to be part of a larger, factorywide network of advanced equipment systems. Maguire's new controller also incorporates loading software.
"We also see trends to seamless data where the push for simplicity and visualization is crucial," said Tiffany Maguire, marketing manager for the company. "This allows managers to see in a moment really how the process is running and that a plant is effectively controlling its raw material simply and efficiently."
A lot of work goes into making simpler, faster and better-connected equipment. "With the speed of change in things like consumer apps, for example, what was great two years ago [is] maybe completely superseded now," Maguire said. "So a major challenge is laying down the backbone to be able to look forward as well as backward. A key premise to design for Maguire has always been the ability to have full compatibility from a system built today as per a system built in 1990."
ACS Group
Tony Johnson, product manager, material handling for ACS Group, New Berlin, Wis., said the trends he sees in the blender market often involve controls. Most customers are seeking controls that are easy to use and troubleshoot. Connectivity, both from a machine control and monitoring standpoint, are key issues.
"We are also continuing to see a wider range of materials that customers are wanting to convey, blend or dry," he said. "There are more and more engineered resins that pop up every week, and many more customers are beginning to incorporate additional powder and liquid materials into their operations."
Integrating control platforms with customer's existing auxiliary equipment controls remains a key challenge. "As the desire for centralized control and centralized [machine] health monitoring grows, it becomes increasingly important to be able to communicate with all types of equipment, whether you are the manufacturer or not," Johnson said.
ACS Group has made several upgrades to its BD-500 blender, which is rated for mixing rates of 500 pounds per hour. Designed for injection molding, extrusion and blow molding applications, the gravimetric blender has been updated with a new gear reducer and a modified paddle for more aggressive mixing action. The new design recently underwent beta testing, but ACS plans to roll it out soon with the BD-500, as well as with its other sizes of blenders.
In addition, ACS has launched a new bowl blender variation of its BD-500 for small batch blending. It uses specialized mixing chambers coupled with customized paddles that provide a strong mixing action for a range of materials, include virgin pellets, regrind and color, Johnson said.
Conair
Customers have several requirements when it comes to blenders, said Alan Landers, blending product manager for Conair Group, Cranberry Township, Pa.
Accuracy is one key, particularly with small amounts of expensive additives. What's important in dispensing, Landers said, is the proper sizing of the metering valve openings. A small dosing valve for a high-percentage ingredient will dose accurately but will limit the total blender rate. And using a large valve to dose a small-percentage ingredient will compromise dosing accuracy.
Processors also need to be able to make color and formulation changes quickly. To address this need, Conair supplies blenders with as many as 12 material hoppers to allow the addition of bins for different color stages. "Sequencing the color recipes from light to dark can reduce the amount of purge time between colors," Landers said.
The company recently upgraded the controls for its TrueBlend blenders. Featuring streamlined navigation and increased capacity for storing up to 3,000 recipes, the new SB3 controls have been designed for user-friendliness, with all set points displayed simultaneously on a 7-inch color touch screen. After the operator enters the percentages of the blend, the controls complete the set-up process. The system automatically weighs the ingredients in the proper sequence and maintains the correct blend ratio. Also included is a new file manager that provides totals about the materials used and creates alarm reports.
To track how much resin, regrind, color and additives are being processed, the TrueBlend operates with the Microsoft SQL reporting method. The system is also available on its TrueWeigh continuous blenders and TrueWeigh extrusion controls. A well-designed query can yield information that will allow processors to operate more efficiently.
Allan Gerlat, correspondent
Contact:
ACS Group, 262-641-8600, www.acscorporate.com
Conair Group, 724-584-5500, www.conairgroup.com
Maguire Products Inc., 610-459-4300, www.maguire.com
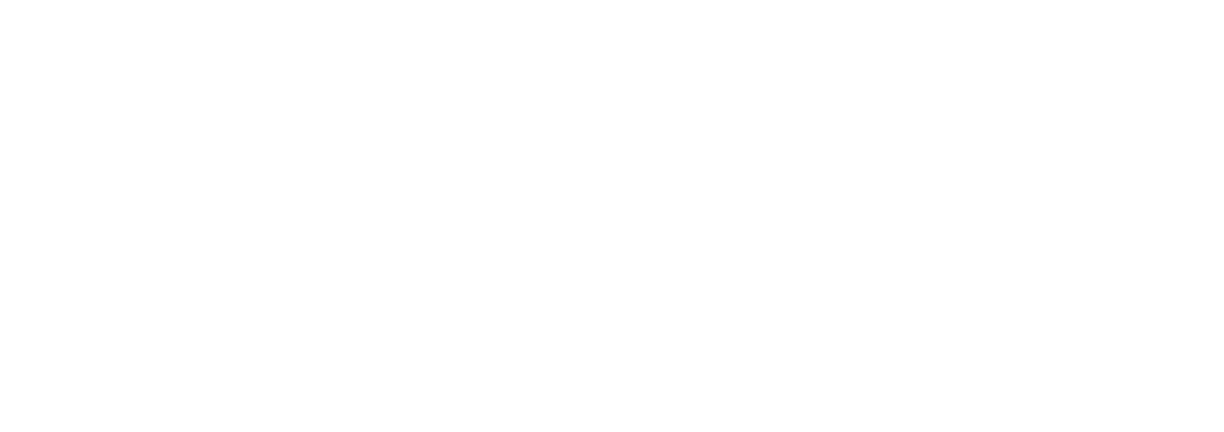