Special Report: Companies take on difficulties of moving powder, regrind
Compared to standard resin pellets, regrind and powder present special, yet different, conveying challenges.
Powder — whether resin or additives — and regrind are completely different bulk solids, said Heinz Schneider, president and CEO of Lancaster, Pa.-based Pelletron Corp. "Powder needs special powder valves for conveying and sometimes special ... technologies for sticky powders, [such as] conveying lines with bypass lines that blow additional air in the conveying pipe to keep the powder moving."
Conversely, regrind consists of chipped or flaked plastics and processors need to convey the chips with specially designed rotary valves to avoid clogging the rotors.
"It's a completely different design compared with a powder valve," Schneider said.
Moving powder and moving regrind, are "night and day different," said Scott Collins, a spokesman for Conair Group, Cranberry Township, Pa. Regrind can involve dust, but, "with powders, dust is what you are conveying. It is a valuable raw material, and your biggest challenge is preventing it from clogging up filters and reducing conveying efficiency. But you also don't want to remove it completely," he said.
It's all about particle size, said Don Rainville, owner of Advanced Auxiliary Equipment Inc., Mathews, Va. He explained that smaller particles can be suspended in slower airflow. If the air is moving slowly enough, small particles fall back into the chamber. Larger filters reduce the speed of the air, he said.
"A good example of a material with both is PET sheet scrap," Rainville said. "Most applications require large, 3-inch tubing to prevent clogging, combined with bag filters for the fine dust or particle separators that let the fines go to bag filters at the vacuum pump."
Managing airflow, filters
The diameter of the tubing normally is determined by the rate and distance. In the case of regrind with square particles, large particles, irregular shapes or soft materials, the tube size may need to be larger to prevent clogging.
Similar considerations are at play when conveying powder. Airflow and particle size determine the needed filter size, Rainville said. It's best to have a filter large enough that the velocity of the air at the face of the filter is not fast enough to support the particles, causing them to fall away from the filter.
In most cases, Rainville said, bags work well with powders because they move with the airflow, similar to snapping a towel.
Advanced Auxiliary has feeders designed to fast-cycle the regrind on a last-in, first-out (LIFO) basis, "so that you can room-dry material directly from a grinder, even when you're not running all the regrind that you're generating," Rainville said.
Rainville sees other considerations when processing regrind. "If you are unable to use all of the regrind generated, an open-loop system is required. Open-loop systems provide for storage of the unused regrind in bins or drums. When running dried material, it is important to quick-cycle the regrind to avoid regaining moisture."
The company has systems that reduce the time it takes to transport the regrind from the grinder to the machine throat down to a few minutes. This can be done with proportional loaders or low-volume blenders or feeders.
"Running dried material is complicated when more regrind is produced than is allowable in the process," Rainville said. "That requires a LIFO system that bypasses the excess regrind while returning only the freshest material to the process."
Valves offer remedy
One big challenge in moving regrind is that rotary valves can lock when used for conveying or discharging the material, said Pelletron's Schneider.
Because regrind flakes do not flow freely and have differing sizes and thicknesses, flakes can slip between the rotor and the housing, locking the valve. A larger clearance between the rotor and the housing would avoid the problem, but would also result in a lot of leakage, he said.
To solve the problem, Pelletron developed a special rotary valve, the GRM-RG, which stands for granular rotary valve medium pressure-regrind. "The valve has a combination of features that prevents locking of the valve," he said. "The anti-shearing device [works] in combination with V-shape rotors."
Moretto SpA, Massanzago, Italy, offers a variety of conveying systems that are suitable for powder and regrind, as well as One Wire products for overall system management. The One Wire series includes the EXA, One Wire 3 and One Wire 6 products. The EXA system can manage up to six receivers.
One Wire 3 features centralized server functionality and the ability to add up to 80 inputs, such as receivers, suction units and automatic manifold units. It provides a dual-zone function that allows for management of two vacuum pumps connected to a single sorting station. By determining receivers' fill levels through vibrations, the One Wire 6 conveying-management system automatically sets up and optimizes the quantity of resin being conveyed.
Tony Johnson, product manager, material handling, at ACS Group, New Berlin, Wis., said the company specializes in conveying pellets, but is seeing an increasing number of customers requesting systems for powder additives. The company is revamping its VacTrac VTC Series of conveying controllers.
The upgraded system, which has been designed for extensibility and flexibility, will be capable of handling regrind and powders, though special pumps would be required for powder applications.
The company said the controls will allow customers to easily reconfigure their conveying systems as their operations grow. ACS Group plans to make the upgrades available this fall.
Allan Gerlat, correspondent
Contact:
ACS Group, 262-641-8600, www.acscorporate.com
Advanced Auxiliary Equipment (AAE), 804-725-1950, www.dryers-loaders-blenders.com
Conair Group, 724-584-5500, www.conairgroup.com
Moretto USA, 614-541-9696, www.moretto.com
Pelletron Corp., 717-293-4008, www.pelletroncorp.com
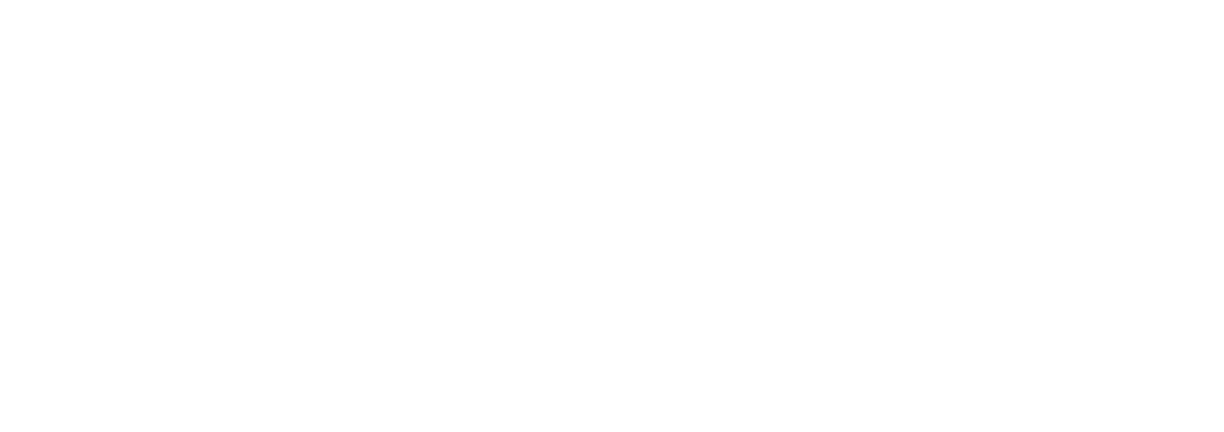