Special Report: Latest equipment prevents, controls dust and fines
A pressing concern for users and manufacturers of materials-handling equipment is the prevention and control of dust and fines — or how to use those materials in a productive way. Equipment makers offer several remedies, including velocity control and pipe elbows that reduce friction.
Pelletron Corp.
Two factors create dust in conveying systems, said Heinz Schneider, president and CEO of Lancaster, Pa.-based Pelletron Corp. — velocity and the design of pipe elbows.
Dilute-phase conveying systems generate a lot of dust and fines because of their high velocity. Schneider said Pelletron recommends modifying existing systems with its Strandphase conveying technology, which uses low velocities.
Pelletron's Pellbows are its answer to long-radius elbows, which Schneider said are a major generator of dust in dilute-phase conveying systems. The Pellbow creates a soft-impact zone with no grinding action, preventing the material and pipe from being damaged.
The company also offers the C-20 and RC1 dedusters, which have been upgraded in the past year. Designed for injection molding machines, the C-20 can process up to 100 pounds per hour of dry, granular material. It has been updated with an improved inlet design and new flexible agitator paddle and combined cyclonic dust-collection module. The RC1 is designed for both extruders and injection molding machines. The system, which can process as much as 750 pounds per hour, was upgraded this year with a new variable-speed paddle and wash air fan. With a combined cyclone-filter-fan assembly, the machine now has a smaller overall footprint.
Hosokawa Polymer Systems
For a U.S. manufacturer of blow molded HDPE containers, the use of dedusting systems has provided cost savings, according to Hosokawa Polymer Systems, Berlin, Conn. The blow molder realized a return on investment within four months of installing Hosokawa's KSI dedusting system. With the system, the manufacturer experienced less downtime and reduced labor and maintenance costs associated with clogged material lines.
A second Hosokawa customer, a PVC sheet extruder, experienced similar results, as the need for filter cleaning dropped from every two to three hours to once every two weeks.
The KSI comes with a static-elimination system and can be fitted for metal-separation applications. It is often used inline with granulators and is suited for a range of materials, including PC, thermoplastic elastomers and nylon.
Hosokawa estimates that its dedusting systems can produce savings of $100,000-$140,000 per year and lead to reductions of 80-90 percent in part-reject rates. The various models have capacities ranging from 50 to 10,000 pounds per hour.
HammerTek Corp.
HammerTek Corp., Bethlehem, Pa., has steadily expanded its Smart Elbow deflection-elbow series. Now available in tube and pipe styles with 16 diameters, the Smart Elbow changes the direction of materials such as regrind or pellets with no impact, even at high speeds. Its spherical chamber, which extends beyond the bend in the elbow, causes a ball of pellets suspended in air to rotate, deflecting incoming pellets and preventing them from hitting the elbow wall or generating heat.
The Smart Elbow benefits processors because it prevents the friction that causes pellet surfaces to melt and form streamers, angel hair and snakeskins, protecting the physical form of the conveyed material while reducing its heat history. By preventing impact with the elbow wall, the product also prevents wear associated with elbow failure, system shutdowns and recurring elbow replacement costs.
Pellets flowing through the deflection elbow in a curved pathway exit the elbow's cross section evenly, returning quickly to a laminar, steady state of flow within the conveying line, with less turbulence than "rope-shaped" lines of pellets that skid against the outer wall of conventional and plug T-shaped elbows, said Charles Williston, national sales manager for HammerTek.
For processors, one way to cut costs is to eliminate parts, labor and downtime costs associated with elbow replacements because of wear. The deflection elbows cost more, however, so HammerTek finds some customers need to be convinced to invest for the long term, Williston said.
Witte Co. Inc.
Designed to prevent and control dust and fines in compounding operations, the 200 series of pellet classifiers from Witte Co. Inc., Washington, N.J., separates out fines and oversize material using screens and perforated decks. The company also offers its 400 series classifier, which combines a fluid bed processor and pellet classifier in one machine. The fluid bed processor can be used to cool or dry the pellets.
"Combining the two pieces of equipment saves space and makes a more efficient pellet processing line," said Tyson Witte, president and COO.
He sees a movement in this market toward equipment that can handle large capacities. That means making larger machinery that's as user-friendly as smaller equipment, despite components that are much heavier and could be difficult for one operator to handle.
Witte said the company can make components that split apart or use special lifts to allow parts to be lifted mechanically.
Novatec Inc.
Baltimore-based Novatec Inc. markets filterless vacuum receivers for vacuum conveying systems, including the VR-FL Series with 12- to 114-pound capacities, and the VRH-FL Series with 12- to 76-pound capacities. They can be effective in separating airborne dust from the resin pellets, said Jim Zinski, VP of product technology.
Novatec's airflow regulators maintain a narrow air speed range at the vacuum pump. They reduce dust and fines by eliminating air-speed spikes through varying loads. And Novatec's MCS and FlexTouch variable speed pumps and conveying controls also address the issue. Vacuum pumps can reduce fines and dust when they are slowed down to move less air and have less suction, Zinski said.
Air-speed control is one variable that Zinski said has increasing importance with customers. Other variables are specialty elbows and tubes and air cooling. "Heated conveying air can increase fines and dust generation for temperature-sensitive materials like LLDPE," he said. "To mitigate this issue, heat exchangers can be installed between the blower and material entry point to remove the majority of the blower's heat from the airstream."
Processors need to understand the importance of equipment maintenance and setup to control the problem. "Fines and dust can be generated by size-reduction equipment before materials enter a conveying system," Zinski said. "Lack of proper design consideration at the start of a project, or when expanding an existing system, can lead to unnecessarily high dust and fines generation."
Size Reduction Specialists
Don Maynard, CEO of Size Reduction Specialists Corp. (SRS), East Lansing, Mich., said he has seen instances of dust and fines composing as much as 48 percent of the material customers are trying to process. Typically, the average is about 15 percent, but badly maintained granulator blades can lead to much greater levels.
Of special concern is the growing use of engineered resins and additives, including fire retardants and graphites, Maynard said. These materials have a tendency to shatter when granulated, leading to even higher levels of dust and fines. To address this concern, SRS offers its DFRS dust and fine removal system, which is available in models for press-side use, and larger versions for central operation.
The system uses paddles to lift and tumble material around divided sections of a rotating cylinder. The cylinder has a filter wrapped around it that can be easily swapped out, depending on the size of the holes appropriate for the application.
With the DFRS, Maynard said operators can purify their regrind.
"By getting these unwanted sizes out of it, what it's done is it's almost got the productivity back up to 100 percent."
SRS offers several sizes of the DFRS, with throughputs ranging up to about 1,200 pounds per hour. Its newest, the DFRS 0308, hit the market about a year ago. With an 8-inch-long, 3-inch-wide cylinder, the DFRS is the company's smallest anti-dust system.
Advanced Auxiliary Equipment
At Advanced Auxiliary Equipment Inc. (AAE), Mathews, Va., owner Don Rainville said dust is a problem for most plastics processors, but AAE promotes using it. "When possible, it is best to use the dust by using loaders with filters that require no regular maintenance and promote the even flow of dust without accumulation. Using dust turns it into profits and avoids disposal problems."
But he acknowledges sometimes dust can't be processed and must be removed. "There are many processing problems caused by dust that can affect the quality of the finished product," he said. "The best example is black specks in clear parts. Compressed air and vacuum loaders with powder-style bag filters can eliminate the filter cleaning normally associated with dusty materials."
He said it's just as important to have bag filters to prevent the dust from accumulating and falling into the process in clumps, which can clog the machine throat and cause process-related quality failures. AAE offers vacuum and compressed air loaders that can remove fines for collection in remote filters.
Everything has dust, Rainville adds, even virgin polymer. "With dust, use it or lose it. That's your choice, and that changes everything."
Allan Gerlat, correspondent
Contact:
Advanced Auxiliary Equipment Inc., 804-725-1950, www.dryers-loaders-blenders.com
HammerTek Corp., 610-814-2273, www.hammertek.com
Hosokawa Polymer Systems, 860-828-0541, www.polysys.com
Novatec Inc., 410-789-4811, www.novatec.com
Pelletron Corp., 717-293-4008, www.pelletroncorp.com
Size Reduction Specialists Corp., 517-333-2605, www.srscorp.com
Witte Co. Inc., 908-689-6500, www.witte.com
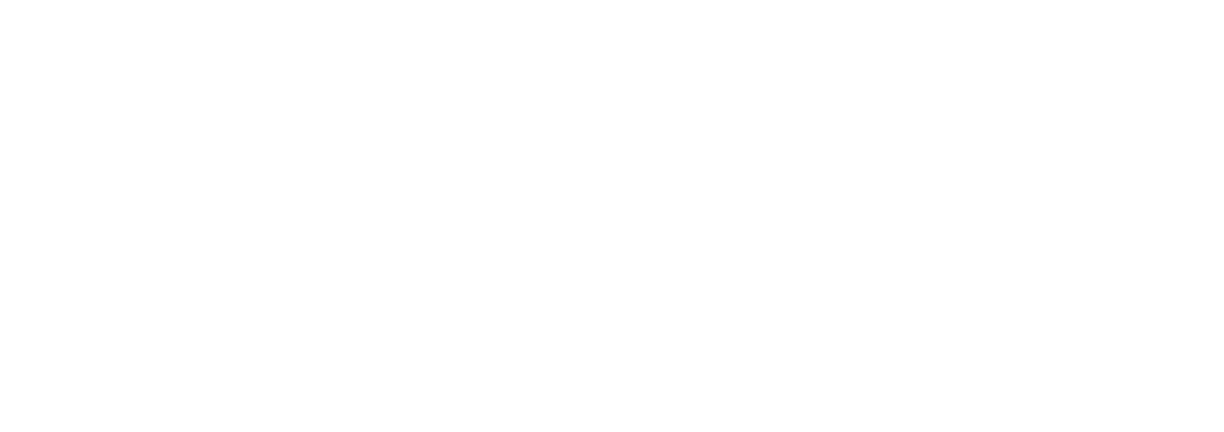