For the first time, Engel Austria GmbH, Schwertberg, brought its trend.scaut international automotive conference to North America. Experts presented information about trends in injection molding technologies for the ever-changing end market during the one-day event in Livonia, Mich., near Detroit. The company also used the platform to announce its partnership with two technological centers in that area. (Read story on here)
Trend.scaut has previously been held in Europe and Asia. Officials said that the time was right to hold it in the North American market because it is a non-NPE year; similarly, Engel sponsors the event in Europe in years when the K show is not held. Although the automotive industry is an international industry, each region presents unique challenges to producers and suppliers, according to Engel.
In North America, for example, lightweighting of vehicles is a priority for automakers. The U.S. government issued Corporate Average Fuel Economy standards, commonly called CAFE standards, requiring carmakers to raise the average fuel efficiency of new cars and trucks to 54.5 miles per gallon by 2025. The 2016 CAFE standard for new cars and trucks is 34.1 mpg.
"Automotive forces us to consistently innovate," said Engel's Christoph Steger, chief sales officer. "We have to be the leader in technologies."
"It is all about lightweight," said Henry "Jim" Moore, advanced technology manager for Magna Exteriors and its Polycon Industries division, Guelph, Ontario. "Lightweighting activity is the key direction, driven by our customers, driven by CAFE standards. In the last three years, there has been a rush of requests coming to us. There is almost a panic when they're coming and asking now," he said.
Moore said that only 5 percent of cars on the road today would meet the standard. "The curve is steep for where people need to go," he said. Design of these parts must take into account the manufacturing process, part performance and material property challenges.
In terms of capital equipment decisions at Polycon, "We're embracing the factory of the future," Moore said. "We want to have equipment that does it all and works together."
Engel's focus primarily is on technologies needed for the future, said Stefan Engleder, who will take over as chairman of Engel's executive board Dec. 1.
"The core of Industry 4.0 is the production," said Engleder, who also will be responsible for research and development. More than just a buzzword, the term has major implications on the factory floor. "Production is the key element." The main thrust of Industry 4.0 is managing complexity because production is getting more and more complex. One of the key features is implementing process know-how on a global scale. Despite regional differences in automotive markets, all OEMs and tiered suppliers have some common challenges, including high costs for water, materials and energy.
The goals of Inject 4.0 are to increase productivity, quality and availability, and provide flexibility.
"Our goal is the smart factory," he said. "The smart factory is the smart machine, smart production and smart service."
Inject 4.0, Engel's version of Industry 4.0, is based on the Internet of Things (IoT) — with its distributed intelligence, universal data utilization and data integration and system layout. Engel says that its products and services for all three areas of the smart factory — smart machine, smart production and smart service — result in higher process capability, productivity, uptime, quality and flexibility.
Data integration and system layout aren't just a focus for Engel, either. A standardization of communication protocols will be announced at the K show, a result of work that has been underway through Euromap, the umbrella group of the European plastics and rubber machinery industry. Participants from all over Europe, especially Germany, Austria, Switzerland and Italy, have agreed to use the software interface standard OPC UA (unified architecture) as a basis, and it is publicly available as an international standard to ensure compatibility across different platforms and manufacturers. This new protocol meets the requirements of Industry 4.0 for the networking of machines, according to Euromap.
Process integration at such a sophisticated level requires an established infrastructure. Central to that is e-connect, Engel's portal that provides plastics processors with a complete overview of all machines in their facilities, including their current status.
During the K show, Engel will present a new e-connect release that will provide even more clarity and functionality, Engleder said. Engel is developing tools for e-connect, to answer questions such as: How long can a screw run? What is the wear on it? When is maintenance required again?
Engleder said that in the future, a service technician will be able to measure the wear of a barrel and screw with an ultrasonic sensor that is affixed to the barrel.
"It measures the screw flight without removing the screw," he said. "You figure out when you have to change the screw. You can predict when the screw will break down."
In the meantime, he said that those technologies with autonomous assistance can prevent all types of issues, for example, automatic detection and adaption of the clamping force through products like Engel's iQ clamp control, which debuted at Fakuma. Injection molders know the issues that can arise when attempting to adjust clamping force. With a clamping force that is too high, there can be venting issues. If there is too little force, flash is a threat. Engel continues to improve its technologies that allow molders to address such issues.
Angie DeRosa, managing editor
Contact:
Engel Machinery Inc., 717-764-6818, www.engelglobal.com
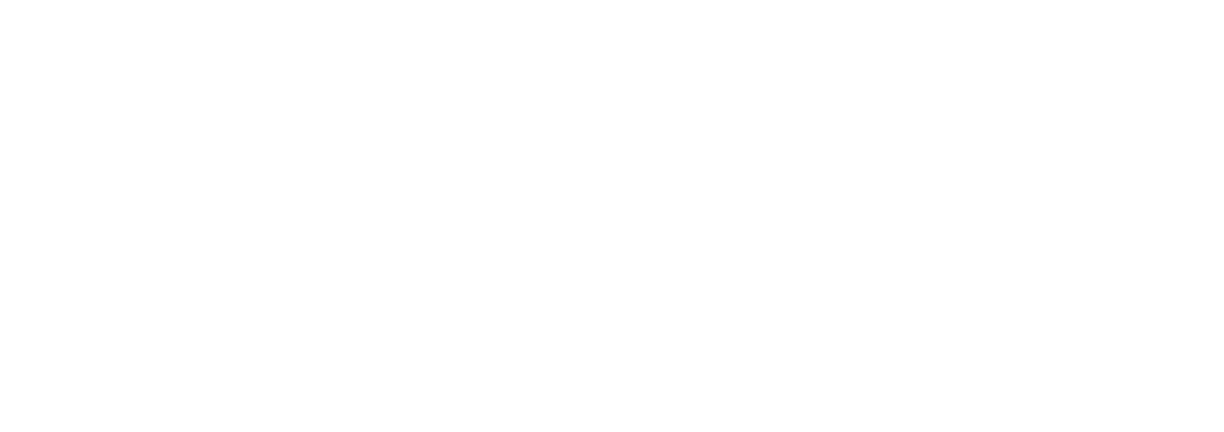