Special Report: Testing materials before processing helps quality, costs
Concerns about costs have forced processors to take a hard look at the materials they're using. With that has come growing demand for devices that quantify polymer characteristics.
"Until about eight to 10 years ago, most plastics manufacturers were not interested in the testing of raw materials; they were even less interested in testing fully homogenized compound before and after — except for the most sophisticated markets, such as medical and aeronautical," said David Newell, director of sales for North America, Dynisco, Franklin, Mass. "But after the '08-'09 market crash, companies began to realize they needed to get hold of quality, because of the cost of waste."
Materials testing requires devices for compounders, as well as for processors. Units can measure melt-flow index (MFI), thermal properties and moisture, as well as other characteristics.
Making materials to form
Multiple companies offer rheological measuring tools, such as Dynisco's LCR7000 Series Capillary Rheometer. Demand for the devices, which measure melt flow, comes from companies hoping to contain costs, Newell said. In fact, confirming resin pellets' MFI is like verifying the fuel that's fed into a sports car, Newell said. The car's owner could take it on faith that the pump really has 93 octane, but if it were your $100,000 sports car, you'd likely love a test to confirm the fuel is right. "MFI is the octane of plastic pellets. Buying it on faith is a real roll of the dice."
Dynisco provides a number of products to help compounders verify that their product is within specs. A capillary rheometer can be used to ensure the compound is fully homogenized for the full amount of time at the right temperature. Dynisco provides two options, with units that can be used in the lab or attached to the extruder with information provided in real time. "Those are the two primary pieces of equipment by which you can know that your product shipped as expected," he said.
For processors, materials testing is equally important. Automation has made the job easier, said Florian Liebert, manager, plastics and composites, Zwick USA, Kennesaw, Ga. "Materials testing is a critical issue for plastics processors managing customer requirements and demonstrating that their products satisfy prescriptive specifications." Both Zwick and Tinius Olsen TMC-United States, Horsham, Pa., offer devices for measuring melt flow.
Zwick recently introduced its Xflow series of melt-flow index testers, which are primarily used by processors to test resins prior to processing. Automation has made this job easier, Liebert said. "The most basic principle of melt-flow properties measurement involves manual timing, cutting and weighing of the extruded material to provide a value of melt mass-flow rate," he said.
The automated features of Zwick's two new plastometer systems — Aflow and Mflow — improve testing speed and reliability. The measurement and control software of both systems offers extensive user- management features, enabling lab managers to coordinate operator resources and assign varying levels of access to review the work performed by each operator.
Tinius Olsen is developing a system that uses a closed-loop load-cell-based technology with force feedback for both its melt-volume-rate and melt-mass flow-rate (MFR) procedures, said product applications specialist Harry Yohn. In traditional deadweight MFR systems, the operator has to physically place the weight used for the test load on the piston or motorized weight lift platform. The loads can be quite heavy — close to 50 pounds — so eliminating this step is one way to improve worker safety.
To improve the process, the company is working on a system that would allow operators to select the load they want to use in a way that's similar to how gym-goers can select parameters on cardio equipment. It would be available as an option with its MP1200 melt-indexing system. The company is also developing a load-cell-based system to entirely replace the need for dead weights in testing.
"The problem," Yohn said, "is that the major international test standards for melt-flow test specifically require a deadweight loading system." To gain acceptance, the company will have to perform much testing on the new system, so, it has not set a release date for the technology.
Feeling the heat
Melt flow is just one temperature-dependent characteristic processors must assess. Instron, Shimadzu Scientific Instruments Inc. and Mettler-Toledo LLC provide testing units for measuring other properties.
In designing its new HV series of heat-deflection testers, Instron considered plastics manufacturing trends, basing the devices' design on market demand for productivity and improved user experience. The Norwood, Mass., subsidiary of Illinois Tool Works Inc., Glenview, Ill., says the devices make materials testing simpler, smarter and safer. Machines in the series, which includes three models, HV3S, HV6M and HV6X, measure the behavior of plastic materials at high temperatures.
Shimadzu, Columbia, Md., which provides equipment for both pre- and post-processing testing, recently released the CFT-EX series capillary flow tester for evaluation of the fluidity and thermal properties of thermoplastic resins, toners, rubber materials, thermosetting resins and adhesives, composites and ceramics. With the unit, materials are subjected to temperatures up to 752 degrees Fahrenheit; the tests provide information about characteristics such as shear rate and viscosity.
Mettler-Toledo, Columbus, Ohio, said plastic processors are using more composites. Because of that, they are seeking more systems that provide information to reduce the overall costs and increase productivity. The company is focusing on finding ways to allow untrained operators to obtain secure results, and making instruments that provide consistently reproducible results. Its thermal analysis products help determine how to optimize pre-process conditions and the degree of post-process curing.
The company's Flash Differential Scanning Calorimeter 1 (Flash DSC 1) and DSC 3+ measure the difference between the heat flows from a sample and reference sides of a sensor as a function of temperature or time. They can provide information about melt behavior, curing, crystallinity, reactivity, glass transitions and purity, among other characteristics.
The Flash DSC has fast cooling and heating rates. "It enables scientists to study the crystallization kinetics of materials often used in injection and blow molding," said Charlie Rabinowitz, a materials characterization market specialist for Mettler-Toledo. "These reactions occur on time scales that are impossible to measure with the use of a conventional DSC, enabling unprecedented insight into rapid crystallization events and therefore the processing conditions of many materials."
The system has ultra-fast cooling rates that allow materials with defined structural properties to be prepared; ultra-high heating rates to reduce measurement times; and a working temperature range of minus 139 degrees Fahrenheit to 842 degrees Fahrenheit.
The DSC 3+ includes a robot that can process up to 34 samples at the touch of a button and produce as many as 50 values a second.
Wringing out the details
In addition to its calorimeter devices, Mettler-Toledo provides equipment for measuring moisture. Halogen moisture analyzers are used primarily prior to processing to monitor the moisture content of plastic pellets for injection molding. The instrument can also be used following processing, if a final product fails quality tests and the root of the problem needs to be investigated, said market manager John Tholen.
The latest generation of the company's HX204 can be adjusted and calibrated at operating temperature, ensuring the instrument is performing optimally. The moisture analyzer has a high-resolution weighing cell, making it possible to determine very low percentages of moisture content, such as that of plastic pellets, Tholen said.
"The HX204 is also incredibly easy to use," he said. "Production workers can operate it with little training."
Lisa Jo Lupo, correspondent
Contact:
Dynisco, 508-541-9400, www.dynisco.com
Instron, 800-877-6674, www.instron.us
Mettler-Toledo LLC, 800-638-8537, http://us.mt.com
Shimadzu Scientific Instruments Inc., 410-381-1227, www.ssi.shimadzu.com
Tinius Olsen TMC-United States, 215-675-7100, www.tiniusolsen.com
Zwick USA, 770-420-6555, www.zwickusa.com
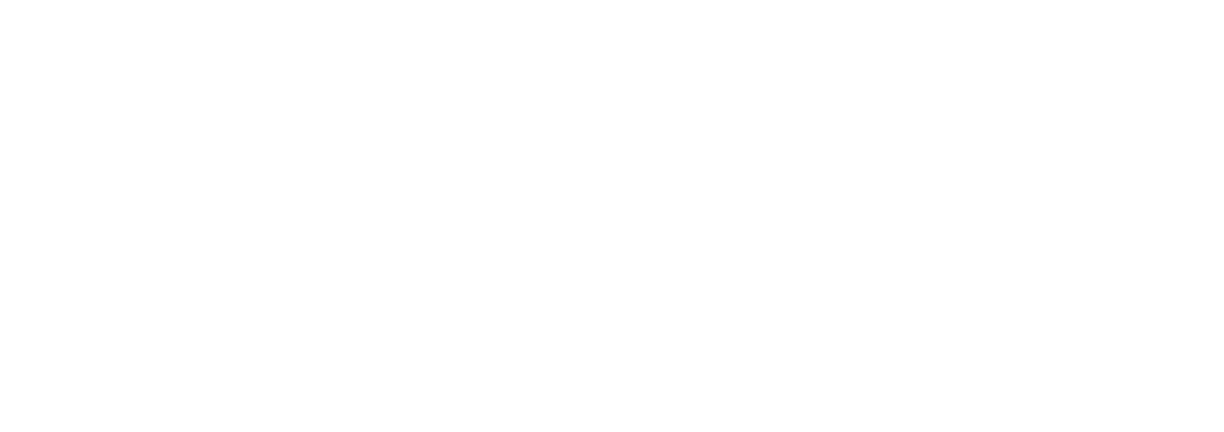