Special Report: Lab extruders provide way to test materials prior to production
The market for extruders in laboratory applications continues to evolve. Machinery makers are adapting to new and varied materials. Customers are looking for ease of use and flexibility. And government regulations addressing safety and the environment pose an ever-present challenge.
KRAUSSMAFFEI USA
To meet those needs, Matt Sieverding, VP, extrusion division for KraussMaffei USA, Florence, Ky., said customers are increasingly seeking laboratory extruders that can simulate production equipment. In general, they use laboratory extruders to develop new mixtures or to perform quality assurance of in-house mixing systems.
"After the mixing process, before you put it in production, some customers verify the quality of the batch by running a small sample through our machine to record the processing data and compare that to the 'standard' for the mix," said Sieverding, whose company markets a lab extruder called the KMD 35-26.
Sieverding said lab extruders, such as the KMD 35-26, provide better and more complete data than standard lab equipment, such as rheometers. The KMD 35-26 is a parallel, counter-rotating twin-screw extruder that can perform material testing or be scaled to complete production runs. It allows customers to quickly test small batches of PVC powder.
Sieverding said a challenge in the market remains keeping lab machines simple. "If something is easy to handle and conveniently designed, the chance that people will use it increases dramatically."
Besides KraussMaffei, a number of companies provide machines that help customers reproduce their extrusion processes on a small scale.
Davis-Standard LLC
Carli Guigli, the marketing coordinator for Davis-Standard LLC, Pawcatuck, Conn., said the company can provide comprehensive options for its customers, who increasingly are seeking turnkey lines. "Many customers prefer to purchase extrusion lines which can serve as instruments for product development, polymer research, material testing and quality control, as well as pilot-scale, limited production runs," she said.
The company's lab extruders include the MEDD extruder and its HPE Horizontal and Adjustable extruders. All three types have small footprints and can handle coextrusion and multilayer applications. Recent improvements to the three include new screw designs for microbore tubing and other low-output applications.
American Kuhne
Graham Engineering Corp.'s American Kuhne, York, Pa., has seen a trend toward new, exotic materials in the medical market. The cost of such resins — as much as $1,000-$5,000 per pound for some bioresorbable polymers — means small-batch testing has become imperative, said Gina Haines, Graham Engineering VP and chief marketing officer. Testing curbs the waste that could otherwise be incurred in production, especially when dealing with these hard-to-process resins. According to Haines, compared to other resins, the bioresorbables are heat sensitive and lose their molecular weight when exposed to a long residence time.
To address the needs of manufacturers using exotic materials, American Kuhne has developed microextruders ranging from 12mm to 19mm, said Steve Maxson, director of global business development, medical, for Graham.
"These equipment solutions, coupled with our processing expertise, help our customers achieve their technical and business objectives," he said.
For laboratories working with multiple material types, another option is a modular micro system. Users easily can remove the barrel and screw for cleaning and replace it with a barrel/screw designed for running a different polymer.
Leistritz Extrusion
Leistritz Extrusion has introduced several products that are applicable to the laboratory market.
The company, based in Somerville, N.J., markets its ZSE 27 MAXX twin-screw extruder direct-to-sheet system, which is a "fairly new concept," President Charlie Martin said. The system facilitates rapid in-line compounding and production of prototype sheet samples. The extruder features a 52-to-1 L:D ratio with modular barrels and segmented screws; a 1.66-to-1 OD/ID ratio for the screw; and a 40-kilowatt, water-cooled motor.
In addition, the company unveiled the ZSE-18 GMP twin-screw extruder last year. The machine features an improved 18mm co-rotating twin-screw extruder that uses a brushless AC servo motor sealed against water and dust. The new motor is substantially quieter than standard motors, and the servo motor technology facilitates a 1,000:1 turndown ratio, meaning that the screw's fastest speed is 1,000 times faster than its slowest speed. That's beneficial in a laboratory environment developing multiple products using a wide range of screw speeds, Leistritz said.
In March, the company debuted an air-quench pelletizer series for highly filled and water-soluble formulations. The LHLG series, which can be used with a lab extruder, enables die-face cutting of pellets in air for water-soluble, highly filled and foamed formulations typically used for medical and specialty plastic products.
Finally, the company has added a Nano 12 twin-screw extruder for small-scale feasibility testing involving batches as small as 10 grams.
The Nano 12's patented micro-plunger feeder can meter very small amounts of material, allowing the extruder to simulate the starve-fed melt extrusion process. Together, the extruder and micro-plunger can replicate the shear-imparting mechanisms of production-scale, twin-screw extrusion equipment. The machine uses the same gearbox as the Nano 16 and micro-18mm twin-screw extruders, also offered through Leistritz. Both the Nano 12 and Nano 16 can perform small-scale feasibility testing, while the micro-18 also can perform clinical batch sample production and scale-up.
Century Extrusion
At Chinaplas in April, Century Extrusion, Traverse City, Mich., launched a more economical version of its CXE 26, which can be used in laboratory applications. The CX 26 has the same gearbox, screws and shafts as its more expensive predecessor, but is available at a lower price, because it is put together in China, as opposed to the United States. Both versions are available in North America.
Charlie Spearing, twin-screw operations GM for Century Extrusion, said the extruders are designed to save space and money. To maximize productivity, they allow quick material changeovers. "Whether it's a production setting or whether it's a lab, it's the same process, just smaller equipment." Using the extruders, Spearing said, customers can test their processes and materials. "You want to run it, and maybe you want to tweak the process, so it's suitable to run on a bigger line."
The CXE 26 features an on-board control system and barrel cooling unit that provides for portability and plug-and-play installation. All barrel heater electrics and cooling lines on the CXE 26 use quick disconnects for rapid changeover. The machine produces a torque density of 15 nanometers per cubic centimeter for maximum process flexibility and throughput.
The CXE 26 features a movable motor and gearbox platform that can slide to quickly change the length of the process section.
It is available in screw speeds up to 1,200 revolutions per minute and has an L/D ratio of 60:1.
DYNISCO
Dynisco, Franklin, Mass., provides a machine that can test various extrudate mix levels in a single sample run. Weighing only 120 pounds, the Laboratory Mixing Extruder, or LME, creates intensive and extensive mixing that can be used to test the processability of polymer blends, from very fine powders to coarse materials, including materials with added fillers and pigments. The LME can process amounts as small as 1 gram, with a residence time of less than 1 minute and a maximum temperature of 752 degrees Fahrenheit. Rotor speeds can vary from five to 260 revolutions per minute.
In addition to the LME, Dynisco offers a number of extrusion-testing accessories. Working in conjunction with the LME, the optional LME Take Up System draws and winds extrudate fibers onto a spindle or through a pair of nip rollers; another accessory, the LME Chopper, pelletizes extrudate from the Take Up System. Made to complement its Laboratory Melt Flow Indexer, or LMI, line, the Autocutter eliminates the need for users to come into contact with a hot barrel or die when retrieving samples for testing.
The Autocutter works with LDPE, PP and PET.
Labtech Engineering Ltd.
Labtech Engineering Co. Ltd., Bangkok, has developed a large range of coextrusion machines. The company recently designed a seven-layer, high-speed cast film line for a customer in the U.S., Labtech President Peter Jurgensen said. It will serve as a test line for the customer, allowing it to produce 10-micron-thick cling films.
Also, Labtech recently built for a customer in Germany a line that will be able to produce 11 layers, with the addition of six extruders that will be supplied next year.
"The dies, as well as the extruders, were developed to meet this ever-increasing demand for more layers and to handle all the new polymers that entered the market, such as tie and barrier resins and a lot of specialty compounds," Jurgensen said.
In the U.S., the company is represented by Labtech Engineering Ltd., Braselton, Ga.
Thermo Fisher Scientific inc.
Waltham, Mass.-based Thermo Fisher Scientific Inc.'s extrusion product for the laboratory market is the Process 11 parallel, twin-screw extruder. The company has extended its range of accessories for the machine with a coextrusion die for ease of use, and a sheet die and corresponding take-off unit for a complete extrusion line. It can mimic full-scale processes with as little as 20 grams per hour of throughput, said Dirk Leister, technical marketing manager, pharmaceutical extrusion applications.
Thermo Fisher is seeing increasing demand in the market for small-scale extruders in various industries, from polymers to pharmaceuticals to food. "To put it simply, small/simple/scalable is the direction that laboratory-scale extrusion equipment is developing toward," Leister said.
Effective instrument training and available technical services are a key part of the investment, he said. Thermo Fisher has an international network of application specialists and academic and industrial partners.
Allan Gerlat, correspondent
Contact:
American Kuhne, 717-848-3755, www.americankuhne.com
Century Extrusion, 231-947-6400, www.centuryextrusion.com
Davis-Standard LLC, 860-599-1010, www.davis-standard.com
Dynisco, 508-541-9400, www.dynisco.com
KraussMaffei USA, 859-283-0200, www.kraussmaffei.com
Labtech Engineering Ltd., 404-992-5398, www.labtechengineering.com
Leistritz Extrusion, 908-685-2333, www.leistritzcorp.com
Thermo Fisher Scientific Inc., 781-622-1000, www.thermofisher.com
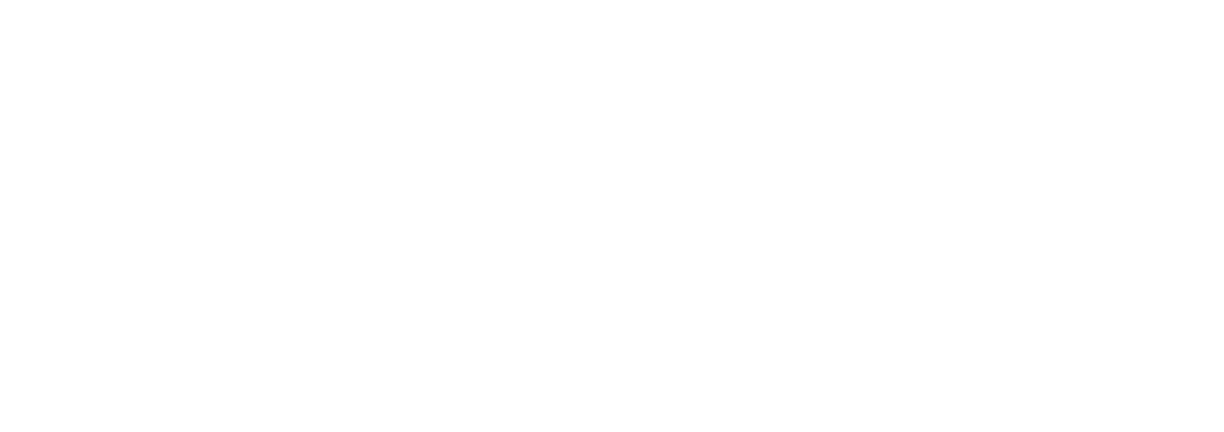