Md Plastics Inc., Columbiana, Ohio, a maker of screws, nonreturn valves, nozzle tips and related machinery components for injection molding and extrusion, has launched a new melt temperature monitoring technology that measures the resin as it is being processed.
The firm's new Temp-Tek Melt Profiler VII temperature monitoring system is used to measure melt density, viscosity, temperature and total energy input (the amount of work put into the resin by the injection molding machine), said President Michael Durina. "A user can see and verify the effect machine variables such as injection pressure, screw speed, injection velocity and operating temperatures have on the polymer," said Durina. Molders can use the resultant readout of the sensor and software to monitor and control their process, said Durina.
The sensor can be installed in a nozzle, nozzle adapter, mold cavity, discharge vent, barrel or end cap of the injection molding machine forward of the check valve, or in an ejector pin, core pin or cavity block slide, said Durina.
At the core of the system is the company's Temp-Tek nozzle sensor. The patented thermoelastic radial strain sensor was designed by Fred J. Buja, a former VP of technology at Eastman Kodak and owner of FJB Plastechnology, Rochester, N.Y. Md Plastics is the exclusive manufacturer of the sensor, which is made by micro-welding two spherical beads from two different metals, where one spherical bead is magnetic and the other nonmagnetic.
The spherical bead sensor is extremely sensitive to temperature changes. "There is a significant difference between this specially designed exposed bead sensor and more conventional sensor designs that are covered or sheathed or grounded, in that our sensor [within a stainless steel body] is exposed directly to the melt," said Durina.
The bead volume of the melt sensor area is reduced by the applied pressure of the melt, which compresses the sensor area. The radial force also generates pressure. The sensor provides temperature readings at all stages of the process, even during decompression or when the screw is idle prior to injection. The sensor is not a pressure sensor per se, but provides a reading indirectly, based on the work done on the material by the injection unit, expressed as temperature, said Durina.
A thin film protects the sensor tip that is exposed to the melt, said Durina. The sensor is designed to respond instantaneously to variations in temperature. The temperature sensor can be calibrated on a variety of scales. It captures data relating to the thermal energy being imparted to the polymer, according to the company. A molder can control injection forward pressure transfer based on the cavity density of the melt, and can use the system to adjust back pressure, barrel temperatures, screw speed and melt decompression to optimize the molding process.
The Temp-Tek sensor is combined with the company's Melt Profiler VII, PC-based software, which converts the data from the sensor into graphs and charts that the molder can configure. When the molder establishes a benchmark that reflects processing conditions for making a good part, it can compare that thermal template to subsequent production runs to detect process changes caused by resin quality, screw or barrel wear, an incorrect nozzle orifice, bad heater band or a poorly performing check ring, according to Durina.
Temp-Tek Melt Profiler VII features updated software that adds a new Viscosity Rise capability which measures the work necessary to move the viscous material from the injection cylinder into the mold for each shot. It takes into account the specific heat and the temperature output monitored by the sensor, said Durina. This function joins three other metrics in the software that help determine whether the machine is making good parts. This includes the calculation of total thermal profile, achieved by monitoring the total process cycle. A Power Factor function captures data during mold filling and packing that indicates the state of the polymer during this phase of the operation. Maximum Te monitors the maximum temperature output during the fill and pack phase.
Temp-Tek Melt Profiler VII joins two other melt temperature technologies offered by Md Plastics. This includes its Melt Profiler 1 or DAC 1 unit, which has been available for more than a year and has a single sensor that samples melt data 14 times per second. This is a lower-cost, simple system. The company also introduced a module nine months ago that can accommodate up to 16 sensors and samples data up to 75 times per second. As many as seven sensors can be plugged into the Temp-Tek Melt Profiler VII, which was introduced two months ago. The sensors connect to a module that sends the data to the software.
Durina established Md Plastics in 1999, following 16 years as VP of sales and service with Spirex Corp., Youngstown, Ohio.
Mikell Knights, senior correspondent
Contact:
Md Plastics Inc., 330-482-5100, www.mdplastics.com
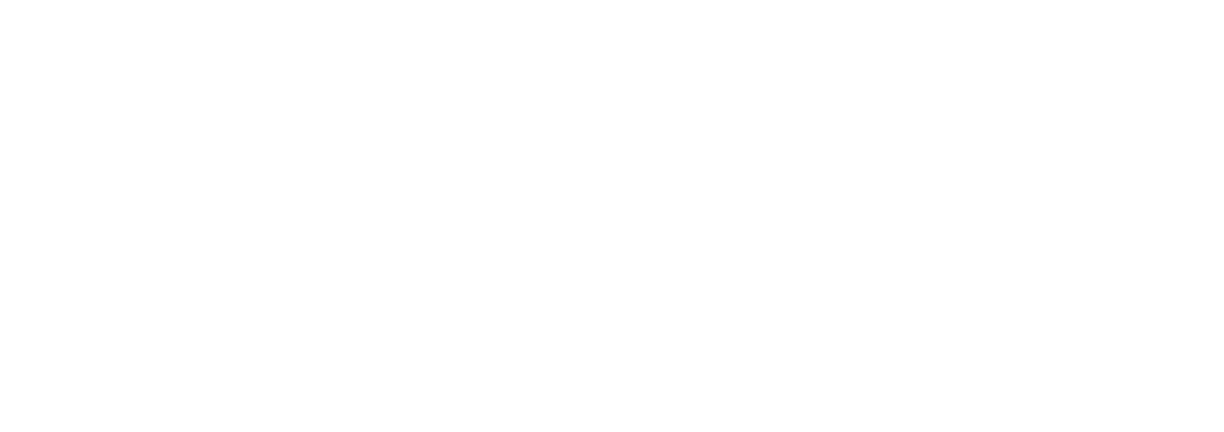