Frontier Injection Molding and Material Technologies Inc. (Fimmtech), San Diego, released Version 8 of its Nautilus process development software for injection molding. The software allows molders to analyze and establish their processes through the use of scientific molding and design of experiments (DOE). Practical scientific molding, unlike simulation software, bases calculations on actual data generated by an injection molding machine in operation.
Nautilus features programs to establish a robust molding process, and was designed by Fimmtech owner Suhas Kulkarni. The Nautilus software helps an injection molder develop and standardize proper process validation procedures, provide training and improve the overall efficiency of its molding operations, said Kulkarni.
The software also uses data from its mold, machine and material databases and information entered by the molder, and then automates the process of finding compatibility between the mold and machines in the shop. "The calculations are based on standard formulas that are very tedious to work out, so we have automated them," Kulkarni said.
Kulkarni standardized the core guidelines and procedures for validating the injection molding process, identifying key factors to be studied based on his degrees in polymer science and molding technology. The Nautilus software can predict the factors that are most important to optimizing the process, and can determine key factors that influence part quality and simulate process changes, said Kulkarni.
Nautilus includes modules designed to analyze or perform molding qualification or mold validation. This includes a six-step scientific molding study module, from which the user can view graphs relating to the viscosity curve, cavity balance, pressure drop, gate seal, cooling and the cosmetic process window. Nautilus also features a module that allows the molder to perform calculations to determine optimal parameters, such as clamp tonnage, shot size, hopper size, injection speed and production output.
Nautilus Version 8 adds a new process-machine capability module that determines if the machine selected by the user is capable of molding a part to a desired specification. The new module also tells the user which process parameters to adjust when there is a problem molding the part, said Kulkarni.
The module takes a number of factors into account in its analysis, including the screw diameter, intensification ratio, transfer position, fill time, injection velocity, peak injection pressure, screw recovery speed and back pressure. The module generates a display showing whether optimal or acceptable parts can be produced on a particular press, said Kulkarni.
The new module complements the mold-machine capability module, used to determine compatibility of the mold with the machine based on clamp tonnage requirement, shot size, material residence time, mold size, material type and other factors, said Kulkarni.
Version 8 can also be used to validate the injection molding process for family molds. "The updated software version can accommodate more part numbers. The software and the structure of the database were improved," allowing for family molds to be tested with the software, he said.
Mikell Knights, senior correspondent
Contact:
Fimmtech Inc., 760-525-9053, www.fimmtech.com
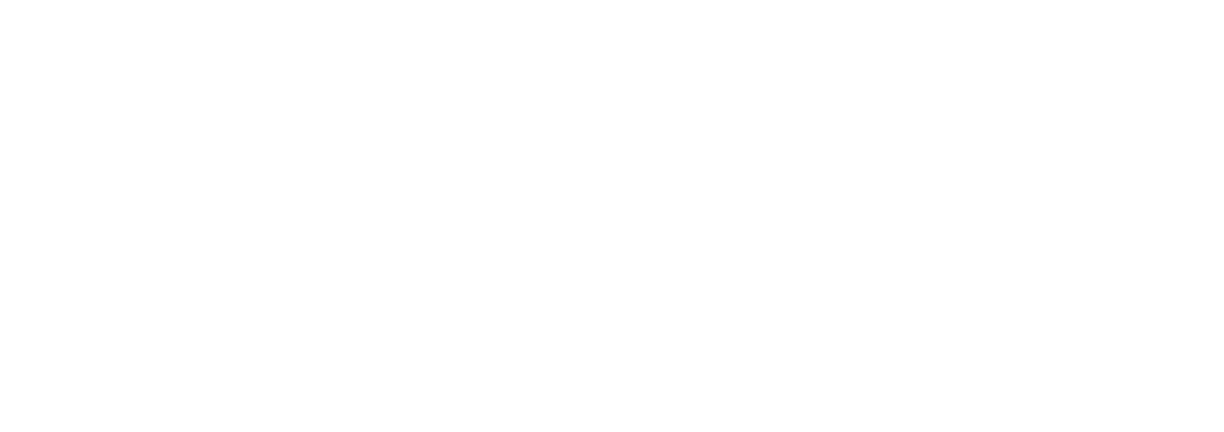