The new active cavity shut-off technology for multicavity injection molds from Ewikon Molding Technologies Inc., Rockford, Ill., prevents cavity failures from causing production delays.
Common causes of cavity failures, such as a broken core, faulty ejector or inconsistent cooling, can cause unexpected production downtime, the company said. Ewikon's new technology allows production to continue despite the bad cavity, and a molder can operate the tool until the order is filled.
The active cavity shut-off technology was developed for use with pneumatic valve-gate drive units that are integrated into the clamping plate. The new technology positively closes the valve pin corresponding to the poorly performing cavity. A molding technician decreases the temperature of the nozzle until the cavity can be repaired.
Ewikon configures the air supply lines differently compared to a conventional valve-gated system, where the clamping plate contains a layout of bores that simultaneously supply several valve-gate drives with compressed air. Active cavity shutoff features a separate, balanced air supply for each valve-gate drive. The air supply layout is integrated into an additional, compact mold plate placed behind the clamping plate, the company said. The compressed air is fed horizontally into the drive supply bores.
Ewikon also developed a new valve technology for the air supply lines. The air supply lines for each valve pin drive unit have specially constructed valves integrated into them to independently operate valve pin opening and closing.
To shut off a cavity, the supply line for valve pin opening is closed, eliminating the pressure. Next, the air supply line for valve pin closing is disconnected using the integrated special valve for that line. However, that integrated valve is designed to be coupled to an additional pressurized air supply line. By doing this, the valve pin is actively kept in a closed position, the company said. The operating unit for the valves is positioned in the mold plate and is easily accessible when the mold is mounted to the molding machine.
A molder could shut off a poorly performing mold cavity by reducing the nozzle temperature and disengaging the valve pin serving that cavity, but this task could be time consuming. In addition, Ewikon said disengaging the valve pin and having a technician reduce the temperature of the nozzle may not be enough to prevent materials with a tendency to drool (such as thermoplastic elastomer) from leaking out of the gate.
Ewikon's active cavity shutoff is currently integrated into five, 24-cavity, two-component molds, for a molder producing a part in which TPE is used as the soft component the company said.
Mikell Knights, senior correspondent
Contact:
Ewikon Molding Technologies Inc., 815-874-7270, www.ewikon.com/en
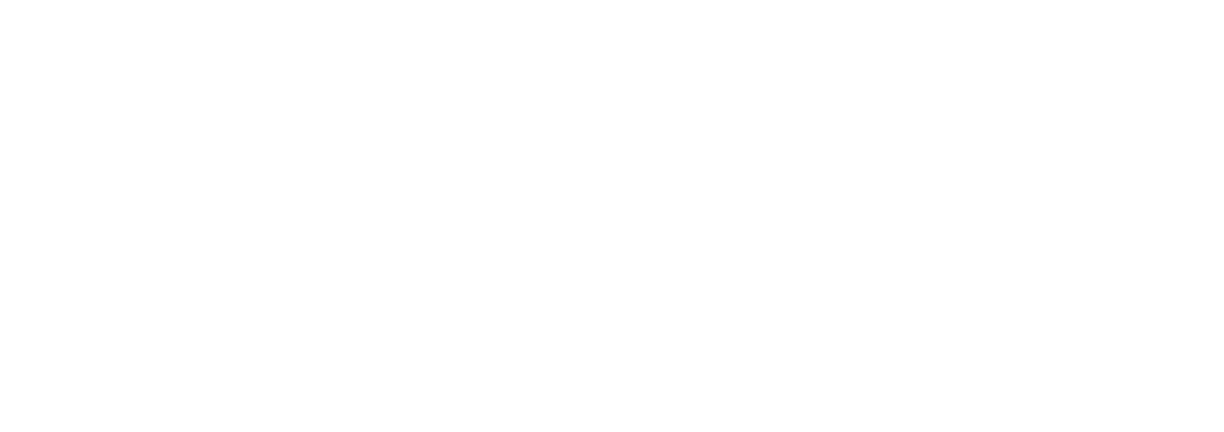