Highlights in barrel developments include a faster way to determine wear and a longer- lasting material for barrel inlays.
GLYCON INTRODUCESWEAR-MONITORING SYSTEM
Glycon Corp., Tecumseh, Mich., a maker of feed screws, barrels, nonreturn valves, tie bars and other equipment, has upgraded a system to monitor critical wear in the barrel and screw of a plasticizing unit in real-time. The software system and hardware allow a processor to determine the rate of wear and judge when a rebuild or replacement should be done.
Glycon's Electronic Measurement and Tracking (EMT) system is a less time-consuming and more accurate way to measure the wear-induced radial clearance gap between the screw and barrel than the conventional method, said President Jeff Kuhman. The conventional method involves halting production of the plasticizing unit, disassembling the machine, then taking measurements of the screw flights and barrel liner manually. The system correlates wear measurements with process data, allowing users to determine when wear begins to have a serious impact on efficiency, said Kuhman.
"Until now, there has not been a convenient way to monitor wear without interrupting production and incurring high labor costs. Consequently, processors would tend to repair or replace worn components in the plasticizing unit only after the process deteriorated to where it is no longer practical to operate," said Kuhman. This practice — known as running to failure — leads to wasted time, increased energy consumption and higher utility costs, as well as increased material usage and higher scrap rates.
Glycon's EMT system includes FliteScan, a handheld digital measuring device with a probe that is inserted into a specially designed port drilled through the barrel wall and barrel liner. The port can be located on the barrel corresponding to a high screw wear area, or in an area of lower pressure, and the probe can be removed when not in use and replaced by a specially made plug. In an earlier version of the system, the probe was permanently located in the port.
FliteScan uses an electronic signal to take a measurement of the distance from the probe tip to the nearest metal surface. It can take into account both the screw flight and the root of the screw while the screw is rotating.
In addition to measuring the distance between the barrel and screw flight, FliteScan can measure the changing distance between the primary and secondary flight of a barrier section, or it can measure the outer diameter of a check ring on an injection machine. EMT can be used with single- or twin-screw systems. With readings taken each time the screw flight passes the probe tip, precession — the nonconcentric movement of the screw within the barrel — is not a factor. The probe's measurements are accurate to within 0.001 inch, said Kuhman.
As part of EMT, a software program stores and interprets the data. The data is compared to an initial, baseline reading to determine the degree and rate of wear, said Mike Mieduch, director of sales at Glycon. The process of collecting the measurement data takes about 15 minutes, said Kuhman. Data can be collected during process startup or shutdown, and even while the machine is near processing temperature.
Data from the FliteScan unit can also be correlated to information the processor inputs into the software. Users can enter process data into the software, such as screw speed, melt temperature, power consumption and other information, such as the costs of downtime or the commissioning of a screw changeout. The date of the measurement, machine number and other information can be entered. The system can be incorporated into new or existing machines.
WEXCO ADDS NEW METALFOR BARRELS AND SCREWS
Wexco Corp., Lynchburg, Va., a manufacturer of screws, barrels and barrel inlays from bimetallic and tool steels, says Dura 686XL, its patent-pending metal, is designed as a higher-wear alternative to its 666 nickel-chrome alloy, said Calvin Lundeen, VP of technical services.
Dura 686XL is a heavy-duty, general-purpose metal with high abrasion-resistance and mild corrosion-resistance. "It takes more energy to wear the material, hence it has a longer life and higher wear-resistance. There are chemical additions to it that make it more wear-resistant than its predecessor," said Lundeen.
Wexco continues to improve the quality of metals in its product portfolio, said Lundeen. Its corrosion-resistant alloys include its nickel-based, high chromium 555 and BO22, as well as its nickel-rich, boron-based alloy B055. It also offers three general-purpose alloys, including the 666, the through-hardened Crucible Vanadium tool steel CPM10V and the Dura 686XL. Wexco also has two heavy-duty tungsten carbide alloys, the 777 Durocast and Durocast premium.
Mikell Knights, senior correspondent
Contact:
Glycon Corp., 517-423-8356, www.glycon.com
Wexco Corp., 800-999-3926, www.wexco.com
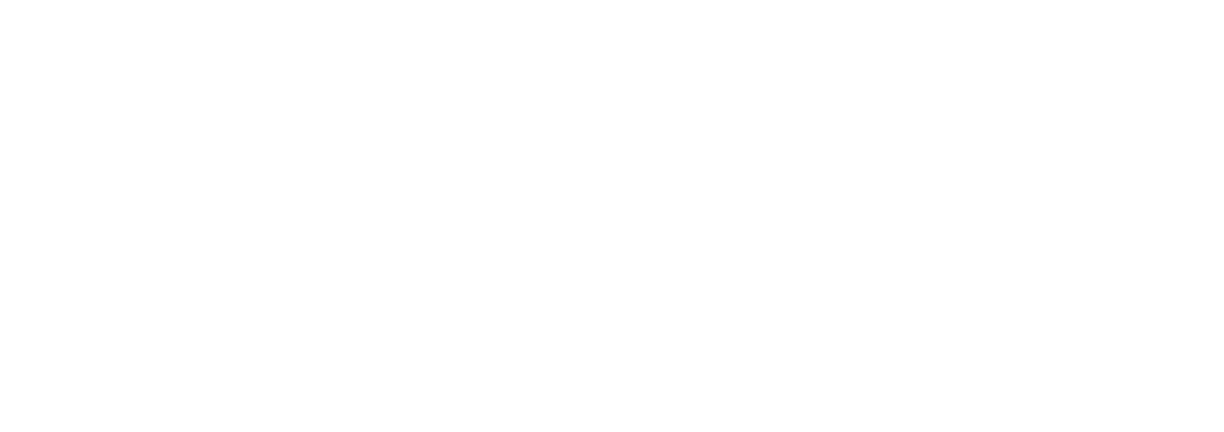