Manufacturers of components that deliver the melt from the plasticizing unit into the tool downstream have upgraded their products to provide more consistent operation.
ALL-PURPOSE VALVE UPGRADEDFOR IMPROVED OPERATION
R. Dray Manufacturing Inc., Dallas, has updated the interlocking-sliding-closing function central to its All Purpose Valve (APV) technology. The nonreturn valve performs in a more consistent way than conventional sliding ring valves or ball check valves, according to President Robert Dray.
The APV uses a sliding closure, rather than a rear-seat closure and frictional forces, to shut off the flow during injection. "A positive seal is obtained when the ring slides past a circumferential groove in the body of the valve. As the ring contacts the upstream retainer, an even more positive seal is now achieved," Dray said.
In tests, the sliding closure of the APV withstands pack and hold pressures up to 20,000 pounds per square inch (psi) for 20 seconds without minimizing cushion. Cushion is the remaining available forward movement of the screw after injection is completed. If the valve leaks excessively during injection or pack and hold, the available space is used up and poor-quality parts result. The sliding closure of the APV does not require high initial velocity for sealing, and the zero internal leakage maintains the cushion position of the screw.
Some molders compensate for leakage by decompressing the screw, making the screw pullback distance greater; this can also result in off-spec parts. The APV normally does not require decompression.
The APV does not require a thick check ring and high frictional forces to achieve a complete seal. The minimal land length incorporated in the APV minimizes pressure drop. The minimal land allows the APV to close more quickly, eliminating leakage and reducing cushion variation, as well as minimizing wear on the barrel and valve components. Screw recovery times are faster and the melt experiences fewer temperature changes, said Dray.
The updated sliding closure has a distance to close of 0.03 inch, which compares to a standard ring valve with a distance to close of 0.12 inch. The closure, introduced this year, is standard on the APV, which Dray commercialized in 2001.
NOZZLE TIP DESIGN ATTRACTSHIGH-TEMPERATURE PROJECTS
Molders Choice Inc., Parma, Ohio, a supplier of injection mold components, says two of its well-established products, its family of coil-heated nozzles and the E Universal nozzle tip, have experienced a strong uptick in demand in new applications.
The E Universal nozzle tip, commercialized in 2013 and designed as a replacement for general-purpose nozzle tips or shut-off nozzles used when processing nylon, is being used increasingly for molding nylon automotive parts, as a means to minimize stringing of the material, said President Kenneth Berger. The E Universal nozzle tip is designed with a reverse taper and a unique bore radius that better handles nylon, reducing downtime and reject parts and minimizing short shots, said Berger. The nozzle is offered in a choice of orifice sizes and tip lengths, and is made from an H13 heat-treated tool steel.
Berger said demand from the automotive sector for its coil-heated nozzles has increased by at least 50 percent over the last year from processors handling high-temperature resins.
"Conventional nozzles fitted with mica bands do not hold up when processing materials at temperatures in excess of 600 degrees Fahrenheit," said Berger.
The company's coil-heated nozzles bring the heater closer to the melt stream, and have a built-in thermocouple located at the tip end that is used to stop material freeze-off.
The coil-heated nozzle eliminates drool, and is designed to operate at higher temperatures while reducing heater band damage. Molders Choice produces the nozzle in a range of lengths, from 5 inches to 24 inches.
SHUT-OFF NOZZLE REIMAGINEDFOR BETTER MELT FLOW
Zeiger Industries Inc., Canton, Ohio, updated its air-operated, pin-type shut-off nozzles for improved performance, said sales director Stan Glover. Now there is no pressure drop through the body of the nozzle until the melt reaches the orifice, Glover said.
The company reimagined the melt flow path through the shut-off nozzle, now offering the device with four channels inside the nozzle to provide as much or more flow as at the entry point. "There are shut-off nozzle designs that feature a large opening at the entry which tapers down through the body. This can cause a restriction, which can cause a pressure drop," Glover said.
With its four flow channels, the device maintains resin flow through the orifice.
"It is a pin-type shut-off nozzle that closes off at the nozzle tip. This compares with a spool or rotary-type shut-off nozzle that does not close at the forward-most point of the nozzle tip," said Glover.
The pin-type shut-off nozzle is typically pneumatically actuated using standard shop air. The nozzles can use a hydraulic cylinder that works hydraulically or has been modified to work pneumatically. A Zeiger-supplied, solenoid-operated directional valve is used to control the pneumatic/hydraulic nozzles.
The redesigned nozzle has a smaller footprint than previous designs. An actuator arm that is part of the nozzle is now positioned to pivot inside the body of the unit. And a pin that holds the actuator arm in place, previously supported by a bracket, has been incorporated into the body of the unit. The repositioning of these components removed 2 to 3 inches of the diameter of the nozzle, said Glover.
"The redesigned nozzle is more efficient and takes up a smaller footprint. It is a complete retooling of this shut-off nozzle," Glover said.
The shut-off nozzle is designed for direct gating to the part, allows for screw recovery while the mold is open, minimizes pressure drop and has a fast-acting, full-flow design that completely closes at the orifice of the nozzle's tip.
MILACRON GAINS NONRETURN TECHNOLOGY THROUGH ACQUISITION
Milacron Holdings Corp., Cincinnati, earlier this year acquired CanGen Holdings Inc., Atlanta, a supplier of highly engineered aftermarket process control components for extrusion and injection molding applications.
The purchase includes CanGen subsidiary Canterbury Engineering Co., Chamblee, Ga., which manufactures screws, barrels, check valves and nozzles for injection molding. The acquisition brings Canterbury Engineering's Repeater series of nonreturn valves, standard check valves and four-piece free-flow valves and nozzles under the Milacron brand.
The Repeater nonreturn valves are actuated solely by a pressure differential rather than by methods that use the melt flow to open ball- or ring-type check valves. The use of melt flow to actuate a ring- or ball-type valve can lead to backflow over the screw, causing a pressure drop and the potential for inconsistent closing and wear on valve components, Milacron said. The valve may not close immediately at the start of injection or sometimes not at all due to inconsistent backflow of resin.
The Repeater valves feature a central piston with a sliding surface that is not contacted by the plastic flow, so seals are not exposed to contaminants, Milacron said. The piston valve closes as a result of a pressure differential on either side of it. According to Milacron, the valve incorporates a pre-closing movement designed to develop pressure on the forward end of the piston. The pre-close is achieved by maintaining hydraulic back pressure for a short time on the molten polymer that is pooled ahead of the screw. The back pressure is generated as the screw rotation is halted, prior to injection, Milacron said.
This design eliminates backflow while maintaining consistent valve position and pressure at the start of injection. The valve closes quickly and completely as the screw begins its forward injection movement, the company said.
Mikell Knights, senior correspondent
Contact:
Milacron LLC, 513-536-2000, www.milacron.com
Molders Choice Inc., 800-809-4623, www.molderschoice.com
R. Dray Manufacturing Inc., 214-368-5424, www.rday.com
Zeiger Industries Inc., 330-484-4413, www.zeigerindustries.com
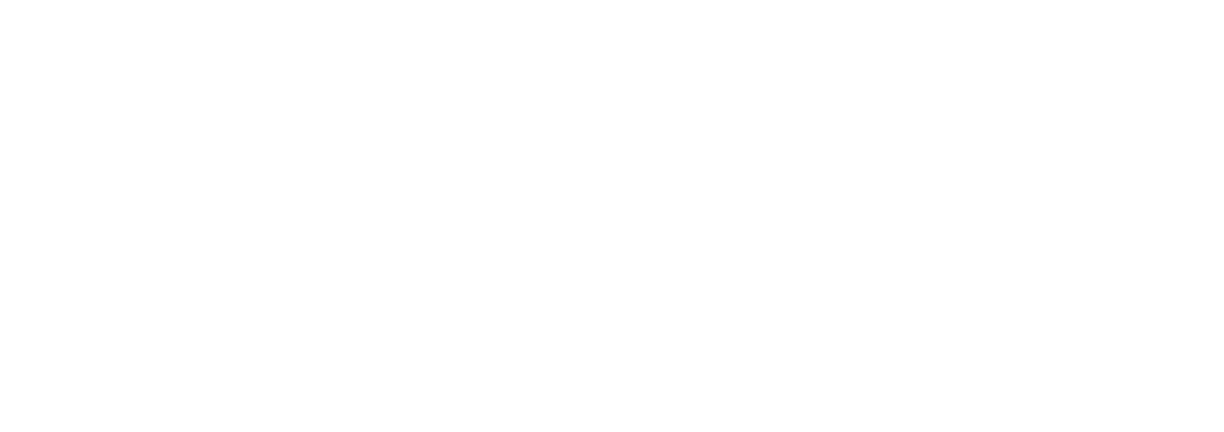