Special Report: Coating formulations preserve, enhance plating
Tungsten and ceramic coatings from two suppliers raise the bar on wear- and corrosion-resistance for plasticizing equipment.
The efficiency of plasticizing equipment decreases dramatically when mechanical and physical components that process the polymers wear. "When the clearance between the outer diameter of the feed screw and the inner diameter of the barrel increases to twice the gap tolerance set by the original equipment manufacturer, output can decrease by 25 percent," said Greg Quinn, senior VP for the plastic and rubber industry, Extreme Coatings Engineered Surfaces. The St. Petersburg, Fla., company supplies tungsten-carbide coating formulations.
"A widening of the gap between the top of the screw flight and the inner barrel wall of as little as 0.015 inch can cause excessive scrap generation and machine downtime," Quinn said.
Poor melt quality is more likely as the wear increases. When wear widens the screw and barrel clearance, a processor has several choices to remedy the problem.
To maintain output at a desired level while compensating for wear, a molder or processor will typically increase the screw speed of the machine. "However, the higher screw rpm can impart excessive shear heat to the melt, resulting in a higher melt temperature, which can degrade the polymer, further decreasing production, while raising power consumption," said Quinn. Alternatively, a processor could maintain the same screw speed with the worn screw, but melt temperature would rise while output would drop.
AGENTS OF WEAR
According to Extreme Coatings, opportunities for wear include when the screw flight contacts the barrel wall; when polymers reinforced with fillers such as fiberglass, titanium dioxide or
calcium carbonate are compressed against the screw and barrel surfaces; and when acids, gases and other chemicals are released during processing. These acids and gases cause pitting in the surface of the metal component. "Pitting can collect, melt, burn or degrade the polymer being processed," said Quinn.
Quinn said the CarbideX line of proprietary tungsten-carbide coating formulations achieves abrasion- and corrosion-resistant characteristics unmatched by conventional alloys for metal surfacing, chrome-plating or metal- strengthening approaches such as flame hardening or nitriding.
In December, the company introduced CarbideX CPR, its newest tungsten-based spray-coating formulation designed specifically for use with single feed screws, twin feed screws and mixing rotors processing PVC, chlorinated PVC (CPVC) and other chlorinated materials. CarbideX CPR is nonporous, unlike the more entrenched chrome-plating treatment that has been an option for processors of chlorinated materials. "Hydrochloric fumes are created during processing of the PVC resins, which seep through microcracks of the porous chrome plating. The fumes attack the substrate, the screw," said Executive VP Scott Caplan.
CarbideX CPR is a specifically formulated blend of carbon and chromium in a nickel matrix, engineered as a replacement for chrome plating, said Caplan. The low-porosity coating is morecorrosion-resistant than chrome plating, and delivers three to five times the service life. The new coating reduces scrap production, keeps cycle times consistent, improves barrel life through reduced wear, extends screw life and delivers two to three times more throughput by maintaining screw and barrel tolerances.
Extreme Coatings builds a 0.003- to 0.004-inch layer of the CarbideX CPR coating using a proprietary process to ensure uniform deposition and excellent bonding.
CarbideX CPR is applied to the feed screw or component using a high-velocity oxygen-fueled (HVOF) spray gun designed by Extreme Coatings. This is different than an electrolytic plating approach used for application of the chrome. The spray gun creates a flame with a temperature of 6,000 degrees Fahrenheit to deposit heated material to the surface of the substrate. The substrate temperature must remain below 350 degrees, otherwise the coating will oxidize and not bond to the substrate, resulting in delamination when the screw is in the machine and process pressures are present, said Caplan. Extreme Coatings developed a proprietary dual-gap cooling system that keeps the substrate cool.
CarbideX CPR fully encapsulates the working surface of the feed screws, including the root, radius, flight sides, outer diameter and mixers, said Caplan. It is also used to coat valve/tip assemblies, continuous mixing rotors and dies, as well as ultrasonic horns, conveyor augers, pump sleeves, hydraulic shafts, heat exchanger tubes and fans, said Caplan.
"Chrome plating can have trouble building a uniform layer, especially on the radius and flight sides of a feed screw, so a plating company would have to use a conforming anode to flow the chrome into areas where it does not want to build up. The anodes can be expensive," Caplan said. (A conforming anode follows the contours of the substrate and performs like a screen or cage to guide the flow of the chrome.)
After application, the coating is polished to a 2-4 Ra mirror finish, which results in a low coefficient of friction. Purging, cleaning and color changes are faster because materials do not stick to the coating, said Quinn.
CarbideX CPR is more expensive than chrome plating but more economically priced than the firm's other coatings designed for very corrosive environments. Extreme Coatings uses its own nickel powder in the new formulation, which lowers the cost.
The new formulation broadens the company's family of CarbideX products, which provide varying levels of corrosion-, abrasion- and wear-resistance. These include four CarbideX C1000 grades, which combine tungsten carbide with either a cobalt matrix, a nickel matrix or a cobalt and nickel matrix. A CarbideX C9000 grade is formulated with micron- and nanometer-sizedtungsten-carbide particles in a cobalt matrix, where high wear-resistance is the goal. The CarbideX formulations deliver a hardness range from 68 to 71 Rockwell C, said Quinn.
Extreme Coatings offers other coatings in the line that are not based on tungsten. They include its C4000 composed of carbon, chromium and cobalt in a nickel matrix, and its C5000 CPR and C6000 products, separate formulations of carbides within a nickel-chrome-cobalt matrix, according to Quinn.
APPLICATIONS DIVERSIFYFOR CERAMIC COATING
Bodycote Surface Technology, Hot Springs, Ark., a supplier of chemically formed ceramic coatings, said its Tech 17 formulation, originally designed to fill and seal microcracks and pores in chrome-plated screws processing chlorinated materials, is expanding into other, noncorrosive plastics processing applications.
Senior GM Jeff Carr said Tech 17's chromium oxide ceramic formulation is designed for application atop a hard chrome-plated screw. Tech 17 was originally developed for use in nuclear reactors where it would encapsulate and protect radiation detection equipment.
Bodycote developed a process to deposit the refractory coating onto a metallic substrate such as an extrusion or injection molding feed screw. This advance allows the formulation to be applied to metal components with an existing chrome-plated surface, as well as those with a plasma spray or HVOF-applied coating, Carr said.
Tech 17 is a chemical slurry that is applied to the metal at room temperature by drain drip, dip coating or spray coating. Then, it's subjected to an updated firing process that heats the material to 800 degrees Fahrenheit (compared to 850 to 1,050 degrees for prior formulations), which removes the water from the slurry, oxidizes the surface of the substrate and starts a chemical reaction that creates a bond with the metal substrate as well as with the chrome plating.
Designing the formulation to chemically react at a lower temperature ensures the integrity of the chrome plating, which can be damaged at the higher coating temperature for the ceramic. "Initiating the chemical process at a lower temperature allows for the conversion of the material into chromium oxide ceramic without impacting the hardness of the chrome plating," said Carr. Bodycote is phasing out the formulations that have a higher temperature requirement.
After firing, the product is allowed to cool, densifying through a capillary action that draws the ceramic material into the pores and microcracks of the hard chrome plating, said Carr.
The slurry is converted into a chromium oxide ceramic that, combined with the chrome plating, delivers a hardness of 1050 to 1150 Vickers and bond strength up to 10,000 pounds per square inch, for corrosion resistance over more than 1,000 hours. The chromium oxide ceramic extends the life of the chrome plating by four to 10 times. The thermochemical process results in no measurable buildup on top of the plating/coating, and no pre-grinding of the screw or component is required.
Bodycote is generating business coating screws that are used to process nonchlorinated materials that are less likely to cause corrosion. Tech 17 is helping processors purge screws more quickly. "Sealing the chrome plating with Tech 17 enhances the nonstick characteristics of the coating. This makes it easier to remove any cooled polymer that is hardened on the screw," said Carr. Users can replace the use of a power sander with a less abrasive cleaning product.
The ability to enhance the nonstick capabilities of a chrome-plated surface has led Bodycote to explore its use in the melt channel of a tool. Bodycote is also investigating the application of Tech 17 to a nitrided metal substrate, where it may be used to further reduce the porosity of the tool.
The chemical ceramic formulation can be used to coat a range of tool steels. Bodycote also offers a stand-alone Tech 23 ceramic grade that adds a coating to an uncoated component for plasticizing, such as an extruder barrel.
Mikell Knights, senior correspondent
Contact:
Bodycote Surface Technology, 501-760-1696, www.bodycote.com
Extreme Coatings Engineered Surfaces, 727-528-7998, www.extremecoatings.net
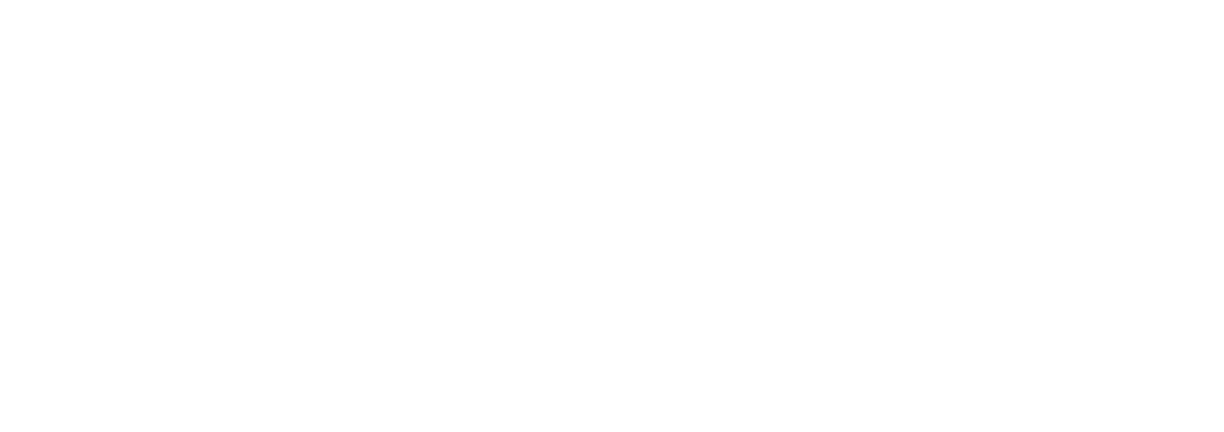