Equipment suppliers presented technology developments designed to optimize injection molding efficiency at the recent Molding 2016 conference in New Orleans.
AUTOMATION CELLS INCREASEMOLDING EFFICIENCIES
A new program from Sepro America LLC, Warrendale, Pa., allows for more efficient operation of injection molding cells that use sprue pickers and side-entry, SCARA and three-, five- and six-axis robots.
The company's "Solution by Sepro" program launched in January provides injection molders with the equipment and engineering expertise needed for increasing the efficiency of a molding cell through automation, said Jim Healy, VP of sales and marketing.
The program ties together robots, peripheral equipment, system design and related services that allow for the creation of more complex and efficient automation solutions. Sepro guarantees successful commissioning of the robots and the peripherals integrated under the initiative. Users can add value to the molded part right at the machine by integrating automation into the work cell, said Healy.
The automation cell can employ new or existing Sepro robots, integrating them into a manufacturing cell that is built around new or existing machines, regardless of the brand, Healy said. Having the automation work in a more integrated fashion allows personnel to be reassigned to more challenging tasks.
The latest iteration of Sepro's Visual control platform, called Visual 3, allows Sepro to integrate the robots, multifunctional end-of-arm-tooling (EOAT), insert feeders, positioning systems, post-mold inspection equipment, assembly and packaging equipment and more, as part of a complex automation cell. The programming sequence for each robot in the cell is created in a step-by-step approach. Molders can see the sequence of the different pieces of automation and related peripherals from the Visual 3 software.
Sepro offers automation for insert placement, overmolding, assembly, palletizing and more. Automation cells can be designed for the detection of components, parts handling, welding, screwing, gluing, cutting and traceability. It designs, configures, tests and commissions the cells.
The company recently installed automation for two manufacturing cells at a factory that performs insert molding and overmolding. Each cell has an injection press and two robots: a Sepro 6X-60 six-axis articulating arm robot and a Sepro three-axis Cartesian robot. The Cartesian robot is mounted axially on each of the 550-ton molding machines. The six-axis robot picks inserts from a feeder bowl and orients them for the Cartesian robot. The dual-purpose EOAT on the Cartesian robot picks, then places the inserts into the mold cavity, then retrieves finished parts from the core side of the tool. The Solution by Sepro program can design automation for molding cells with multiple injection molding machines and robots, as well.
Healy envisions even further integration, between the automation cell and the molding cell, where the robots can be controlled either from the molding machine or from the robot controller. Robot control can then be mirrored on the injection unit. Users can start the machine and the automation program from a single control for faster startup. "Robot alarms can be displayed on the screen of the machine control," Healy said.
SPEED CONTROL YIELDSENERGY SAVINGS
Injection molding machines waste energy at every stage of hydraulic power generation, yet understanding where and how waste occurs is the key to improving the efficiency of the molding machine, said CCS Technology, a Coventry, England-based designer and supplier of industrial automation and control systems.
CCS Technology, represented in the U.S., by PlasticMetal USA Ltd., Huntington Bay, N.Y., offers SyncroSpeed, its dynamic motor speed control system. It is designed as a retrofit for any brand of hydraulic injection molding press to reduce energy consumption costs 35-55 percent while maintaining, or in some cases improving, productivity. SyncroSpeed is not new, but it is seeing an uptick in demand and is being applied to new areas like preform molding for bottle manufacturing. The technology now also is being used in injection blow molding. Some of SyncroSpeed's high-profile clients include Procter & Gamble, Tupperware and many Tier 1 automotive suppliers.
In the current manufacturing environment, molders are challenged to manage two energy-related issues: the energy consumption of the injection molding machine and the energy losses stemming from inadequate control of power generation.
The SyncroSpeed system is designed to control a fixed or variable speed motor used to drive a hydraulic pump on a press. Users are not required to change the motor in any way, yet the system allows the hydraulic injection molding machine to operate nearly as efficiently as an electric press.
SyncroSpeed comprises electronics hardware and control software components, sourced from global suppliers and assembled in a custom industrial steel cabinet positioned next to the injection molding machine. The system connects to the machine control and the motor.
Robert Knaster, CEO of PlasticMetal USA and director of sales and business development for SyncroSpeed in North America, said hybrid presses with electric screw drives are candidates for SyncroSpeed, because the hydraulic motors idle during screw rotations, offering a savings opportunity. Savings can also be realized when the system is used on injection machines with accumulators.
"SyncroSpeed delivers the correct amount of oil volume needed to accomplish a task, so the molder realizes savings by using only the energy required to do the job," said Knaster. The system ensures adequate oil volume is available for correct speed of movement, eliminating the overproduction of hydraulic power without compromising the molding cycle.
Excess energy use can occur when the motor and pump generate the hydraulic power; when the hydraulic power is transmitted through hydraulic valves, hoses and manifolds; and when the actuator uses power. CCS Technology said culprits for wasted energy include inefficient motors or pump control, and pressure or actuator losses, each of which can amount to 5-15 percent of the machine operating cost. Insufficient control of oil volume can amount to 25-35 percent of the cost of operating the machine.
SyncroSpeed is designed to address energy waste associated with oil volume control, pressure losses and pump inefficiency. A SyncroSpeed system achieves the energy savings by monitoring each stage of the molding process to automatically deliver the optimal hydraulic power. Tighter control of energy consumption extends the life of critical machine components, including motors, pumps, couplings and valves, and also can reduce cooling load requirements.
Molders using SyncroSpeed can qualify for energy rebate programs, in which 20-50 percent of the implementation of SyncroSpeed is paid by the utility. Reducing energy consumption at the machine also reduces energy needs of related equipment, including chillers and water-pumping systems. Reducing heat in the hydraulic oil, by optimizing its use, also saves energy.
Knaster said a key benefit of SyncroSpeed is that the logic of the software is integrated into the control of the host machine, which enables the system to continuously adjust to movement and speed. Competing systems do not go far enough in their integration with the machine control, Knaster said, which results in reduced energy savings, because they don't control motor speed efficiently and at every process step.
At the beginning of the program, SyncroSpeed runs all of the motors on the injection press at full speed for several cycles to capture the operating data of the machine. The software captures, interprets and calculates the oil volume needed for each stage of the production run, operating as a speed-control device for the motors and pumps. Speed is regulated by the system more than 50 times each second. SyncroSpeed can operate the motor across its full speed range as required by the process, even at low pump speeds. "Our control system has algorithms to avoid the high-pressure/low-speed operating points of the pumps, to minimize early damage or accelerated wear of the component," Knaster said.
SyncroSpeed runs automatically between tool changes, so no adjustment or monitoring is required by the molder. Users press a button to refresh the system to run the machine with another mold.
Operators input the energy cost per kilowatt hour and SyncroSpeed calculates the cost to run the machine. The system displays the energy saved for each shot (per part) while another screen shows the cost of energy per part. Users can calculate part cost with the screens, Knaster said.
The SyncroSpeed system's touch-screen interface shows the energy costs during each phase of production and provides the status of the system. Users can establish benchmarks of energy consumption for every job.
Knaster said SyncroSpeed is best suited to machines with 250 tons of clamping force or more, with the return on investment coming in about 18 months. The system can be used with smaller presses, but the return on investment is longer.
Mikell Knights, senior correspondent
Contact:
PlasticMetal USA Ltd., 914-584-1848, www.syncrospeed.com
Sepro America LLC, 412-459-0450, www.sepro-america.com
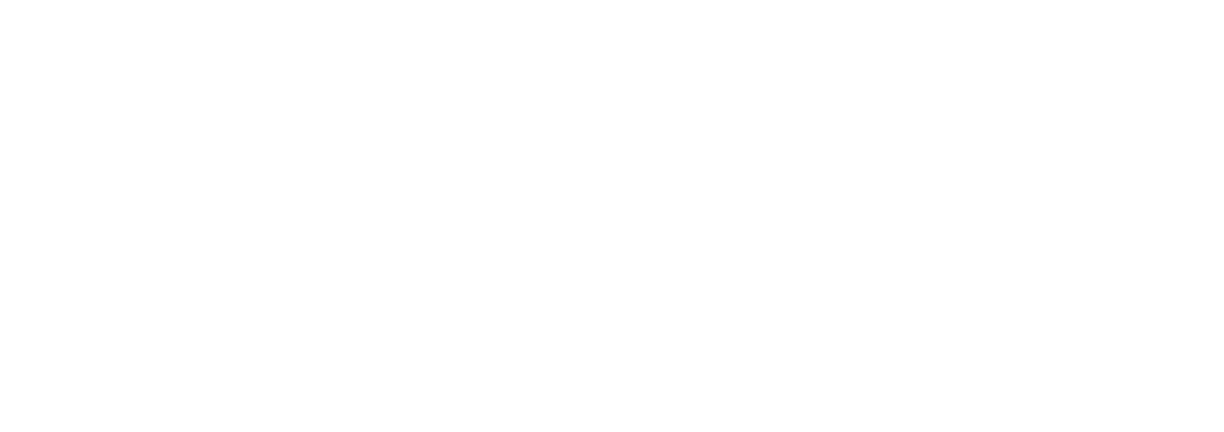