For Steve McCartin, technical sales engineer at Sumitomo (SHI) Demag, Strongsville, Ohio, large molds and small shots are not mutually exclusive. With their wide tie-bar spacing and clean, smooth linear guides, Sumitomo's all-electric SEEV-A machines have the technology to meet the challenge, McCartin said.
"It provides the flexibility to run a wide variety of molds," McCartin explained. "That's a big advantage. You can put bigger molds into smaller machines and still be able to run them."
McCartin presented information about how Sumitomo has addressed medical molders' challenges during the company's recent open house at its facility in Strongsville, where it introduced several new presses. With the addition of five new SEEV-A machines, the company has extended its SEEV-A platform to machines with clamping forces of up to 562 tons. The platform includes two series — the smaller SEEV-A units ranging from 56 to 202 tons and the bigger SEEV-AHD machines, which are named for their high-duty capabilities and range from 247 to 562 tons.
At the open house, a 56-ton SEEV-A was running a family mold of red paper clips in two sizes. Nick Kouloungis, Northeast regional sales manager, explained that the machine series' Flow Front Control (FFC) and Minimum Clamping Molding (MCM) systems make possible flash-free molding — even when different sized parts are manufactured together. With the MCM system, the machine automatically detects the moment when the mold halves meet, so that the optimum pressure can be applied. FFC allows precise control over the flow of plastic, enabling the cavities to be filled evenly.
"What that allows the customer to do," he said, "is to stop the mold. Remember, the plastic's still flowing. It allows the mold to decompress." FFC relies on the elasticity of the material to continue flowing, even though the screw has actually stopped. In this way, he said, operators avoid a common problem involving family molds — the excess filling of the first cavities in a sequence, and the short filling of the last cavities in a shot. The technology also provides a number of secondary benefits: By reducing pressure on the mold, it cuts down on both wear and energy usage.
"We will use less tonnage than any other competitor," said Kouloungis, a sentiment McCartin echoed in his remarks. McCartin cited an example of a mold for a vehicle lens that is normally run on a 600- or 700-ton machine; at the open house, a Sumitomo 562-ton SEEV-AHD needed only about 300 tons of pressure to run the application.
McCartin also pointed to a new 202-ton SEEV-A, as it produced medicine dosing cups in a 2.4-second cycle. The demonstration, he said, showed the benefits of Sumitomo's S-Move servo control technology, which optimizes platen speed to shorten cycle times. Taking advantage of the machine's linear guides to reduce vibration, the system needs just one cycle to automatically calibrate the optimal speeds for opening and closing the mold. Instead of braking or ramping up speeds, S-Move creates a gentle, fluid motion that is actually easier on the tooling, he said. "That eliminates that vibration that would be encountered on other machines from having sharp speed transitions."
Other features of the new machines include an optional screw system known as Spiral Logic (SL). At about three-quarters the length of conventional screws, SL is designed for shear-sensitive resins, McCartin said.
Karen Hanna, copy editor
Contact:
Sumitomo (SHI) Demag, 440-876-8960, http://sumitomo-shi-demag.us
Karen Hanna | Senior Staff Reporter
Senior Staff Reporter Karen Hanna covers injection molding, molds and tooling, processors, workforce and other topics, and writes features including In Other Words and Problem Solved for Plastics Machinery & Manufacturing, Plastics Recycling and The Journal of Blow Molding. She has more than 15 years of experience in daily and magazine journalism.
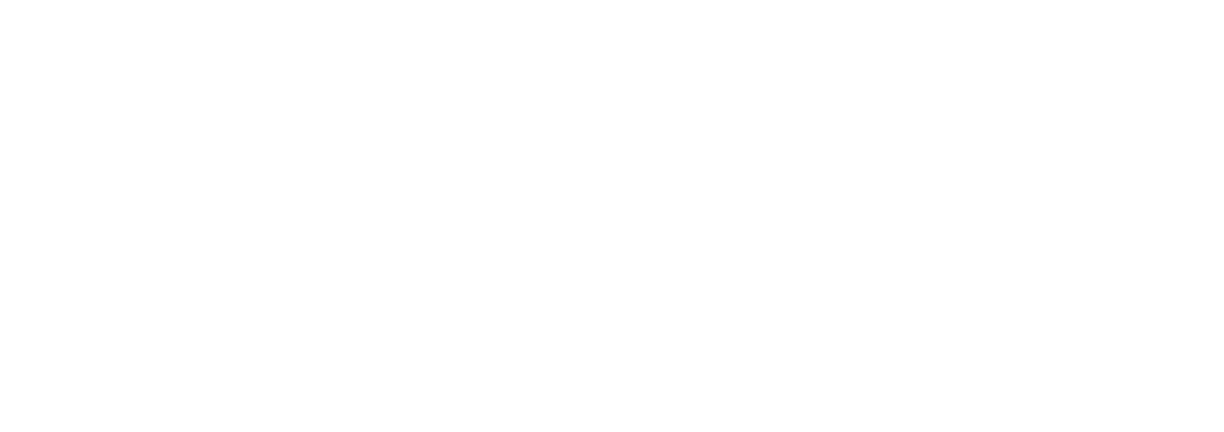