A new feature of simulation software eliminates the need for extrusion die designers to make manual adjustments to improve die geometry after each flow simulation. Using a feature that's being rolled out as part of a SolidWorks software add-on can reduce the development time for such dies by more than 50 percent. Rather than rely on trial and error, die designers now can fine-tune their dies even before they are machined.
Mahesh Gupta, a professor in mechanical engineering at Michigan Technological University in Houghton, Mich., and president and CTO of Plastic Flow LLC, Hancock, Mich., presented the findings at the SPE Shape Extrusion Topcon conference, held March 29-31 in Gurnee, Ill.
For the case studies, simulations were conducted on sheet and profile extrusion die designs on a Dell Precision M6700 laptop. Plastic Flow's polyXtrue extrusion die simulation software was used as an add-on to SolidWorks. SolidWorks creates the die geometry and polyXtrue then is used to produce flow simulation.
At the end of May, Plastic Flow introduced the newest version with unique capabilities, so that dies can be optimized automatically. According to Gupta, a key goal in design of an extrusion die is to develop a die channel geometry that provides uniform velocity distribution at the die exit. That uniform velocity distribution is critical to ensuring limited distortion of the extrudate. Extruded sheets made this way end up in products like wrapping films or, in the case of profile extrusion, medical tubing or windows, doors and automotive interiors.
"In the past, designers had to manually change the geometries using the CAD software," said Gupta. "Many of our customers use our software inside SolidWorks, but the new version will automatically optimize."
Depending on the complexity of the die geometry, a designer might need anywhere from 10 minutes to one hour to make changes after each flow simulation. This new capability automatically improves the die geometry after each flow simulation.
In his case study for simulation of a sheet die design, Gupta used ABS on a die that has a coat-hanger type manifold. Before using the software to optimize the die geometry, the ABS sheet extrudate that exited the die had a faster exit velocity near the middle than at the two ends. Once the die design was optimized using the software, the exit velocity was much more uniform along the entire width of the die. That will equate to a highly uniform thickness in the sheet that is extruded from the die once the die is in production. The software needed 2 hours, 48 minutes to achieve optimization, a fraction of the time that would have been required by a human operator.
In the case study of profile die optimization, Gupta also used ABS. In this simulation, the flow at the exit of the square die was balanced by the software by changing the thickness of the horizontal and vertical walls in the intermediate die plate, according to Gupta. This approach led to uniform velocity distribution at the die exit, which resulted in smaller distortion for the extrudate when compared to a die designed without the software. This die was optimized in 41 minutes.
Gupta said the polyXtrue software has been used by customers worldwide on a limited basis but acceptance is growing as it is upgraded and computers become faster.
"It has become feasible now to do [simulation] where it was not as easy 10-15 years ago," he said.
Angie DeRosa, managing editor
Contact:
Plastic Flow LLC, 906-483-0691, www.plasticflow.com
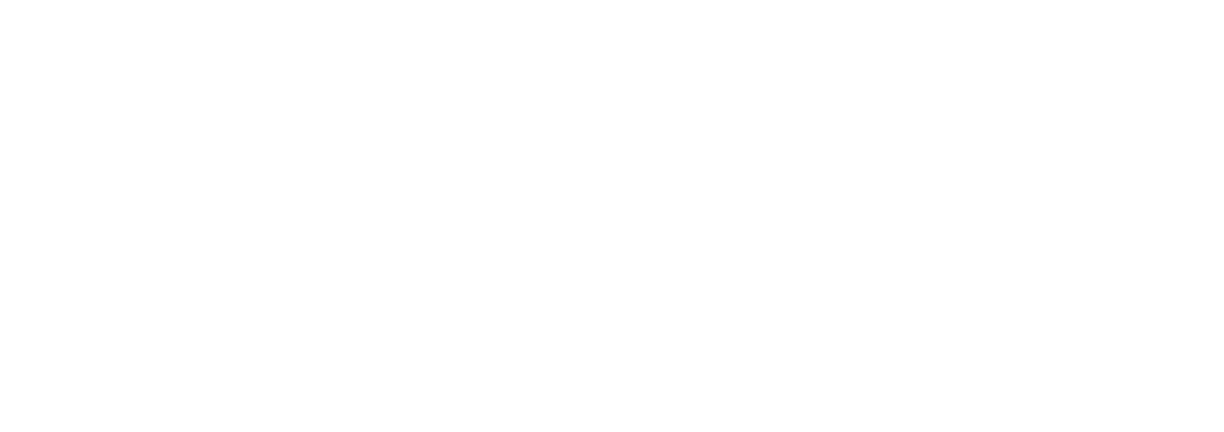