Controls are the brains of any extrusion line and absolutely essential to producing high-quality products with minimal disruption and downtime. But making sure that happens is a big challenge.
Fortunately, there have been major hardware and software advances to make the task easier. Controls suppliers and extruder manufacturers point to advances that make the job of operating an extrusion line more manageable, whether specifying a new extrusion line or upgrading an older control package.
Among the most significant trends are:
• Better connectivity among peripheral devices;
• Easier integration of upstream and downstream equipment;
• Improved machine data and ways to view it;
• Remote troubleshooting.
CONTROLS SUPPLIERS FOCUS ONSEAMLESS INFORMATION FLOW
Brian Fieseler is program manager for OEMs for Rockwell Automation Inc., Milwaukee. He said controls suppliers have been able to consolidate control platforms, networks and gateways — translator-type hardware boxes that convert from one type of information protocol to another. This trend makes it easier to share information on the process. The end result, he said, is better communication among devices on a production line.
When processors purchase a piece of equipment for their lines, they should pay attention to the control platform, he said. He noted that Rockwell works with specialized equipment suppliers to help them integrate their control technology on manufacturing lines.
He said that having a common control platform eases integration of disparate equipment and creates commonality in how things are programmed and how information is generated and transmitted among pieces of equipment. On the other hand, having disparate control platforms requires hardwiring the control modules. "That's not productive," he said. "It's a waste of time and money, and it makes the system loosely coupled, as well."
Paul Whitney, Rockwell's commercial program manager, agreed. He noted that Rockwell's equipment can communicate via Ethernet, facilitating better communication among programmable logic controllers (PLCs) in a production line. In Fieseler's view, although the industry is moving toward better integration of disparate machinery, it would be helpful if an industry organization such as SPI would get involved in developing a standard that companies could work toward. "It's a free-for-all right now," he said. "Rockwell has come as close to anybody to having an unmodified Ethernet network as a choice; there is no proprietary nature to it."
Having uniform controls makes training employees easier, Fieseler said. The more complex the control in the process line, the more challenging training becomes, he said.
While PLCs remain well-established in the plastics extrusion industry, Fieseler sees new opportunities for programmable automation controllers (PACs), which are multidiscipline in nature. One PAC hardware device can perform PLC functions, as well as other functions, such as safety, motion control and process loops for temperature and flow. Fieseler said PACs bring tighter integration with fewer wiring and programming requirements. "All this information that's coming from the sensors on the machines and coming into these PAC controllers can, with the proper programming, allow you to coordinate the whole line in that fashion," he said.
He adds that PACs have potential in machine safety applications, because they can control the machine functions as well as monitor the safety aspects on the machine or production line.
Those trends are allowing vendors to design their controls for greater usability. Mathias Radziwill, business development manager for plastics OEMs at Siemens Industry Inc., Norcross, Ga., said simplifying operator interfaces is important as production lines become more complex.
The company's Simatic S7-1500 controller has Profinet interfaces, an open standard for industrial Ethernet, which was introduced in 2012. It offers a color display with plain text. For troubleshooting, the controller provides detailed information, identifying the damaged part, including part number and network address, so maintenance employees know what to replace.
EXTRUDER OEMS EMBRACEINTEGRATION, CONNECTIVITY
Among extruder manufacturers, one of the biggest trends in controls is connectivity. "A lot of customers want to connect the control system either to a plant-management system or a central data-collection computer," said John Clemens, director of extrusion controls for Davis-Standard LLC, Pawcatuck, Conn.
The company offers three levels of controls, two with a PC-based operator interface and the third with a basic HMI package. All three tie in to a plant network for data collection, he said. Clemens said that the controls are PLC-based. "It's an industrial PC that we provide to the customer, but all of the control is still within the PLC," he said. The company is coming out with a new version of its basic DS-eTPC controller, which has an HMI and fixed PLC. The new version will have an HMI and a PAC, which will have more flexibility and connectivity. He expects the controller to be available soon.
Clemens added that remote connectivity has become increasingly important to processors. The feature allows Davis-Standard to access the PLC on a customer's extruder to perform troubleshooting remotely via a secure Internet connection.
Charlie Martin, president and GM of Leistritz Extrusion, Somerville, N.J., said a couple of trends are allowing extruder manufacturers to cut engineering costs and integrate machinery. He said that distributed input/output offers significant savings on wiring costs in new installations. Leistritz offers Flex I/O, a distributed I/O technology, which reduces the need for wiring. It locates the I/O near sensors and actuators, eliminating long wiring runs and cutting down on engineering and installation time. Martin said that using Flex I/O can reduce as much as 60 percent of the wiring requirements.
Martin also points to a second trend in programming that allows easier integration of upstream and downstream equipment in an automated line. A decade ago, an extruder manufacturer building the line would write the code to integrate upstream and downstream equipment, he said. Today, PLC suppliers such as Rockwell have made available blocks of information that can be pulled into the PLC and automatically create registers, or areas of memory that store bits of information.
The advantage of this is that extruder manufacturers no longer have to write thousands of lines of code to communicate with their devices, he said. "That way you have got the expertise from all the subsuppliers, and all you are doing now is handshaking and reading the data acquisition by these pre-defined registers," he said. The benefit is that "it makes it cheaper and better and more accurate."
Al Bailey, East Coast controls manager of Entek, Lebanon, Ore., said newer I/O platforms and electronics deliver better diagnostics of devices, resulting in better performance data. For example, the company uses variable-frequency drives (VFD) that communicate over an industrial Ethernet network to the processor. From the developers' perspective, this has made it easier to integrate the drive into the control program and get it working with the PLC software, he said. "It's basically plug-and-play," he said.
Bailey sees a major trend away from proprietary networks and toward open networks such as Ethernet. A decade ago, PLC manufacturers had their own proprietary networks. This hampered the number of devices that were available on those protocols, he said. That limitation has largely gone away with open networks. "We use all Ethernet communications, primarily for speed and bandwidth. You can get a lot of data and you can get it quickly," he said. "The nice thing is that there are a plethora of devices out there for it."
Bailey said trends such as distributed I/O and Ethernet are allowing the company to make components such as I/O devices, variable-frequencydrives (VFDs) and PLCs more compact and powerful. The smaller components mean that the electrical enclosures can be smaller or house more items.
For example, Entek uses distributed I/O in barrel cooling. Under the old system, a series of valves would be wired to the PLC for opening and closing during the cooling of the barrel. It has replaced that with an integrated valve bank, with distributed I/O built in with the valves. "Instead of running all of those wires to each of those valves, we just run an Ethernet cable and 24-volt DC power out to it and we are done," he said.
In another example, the Entek side feeder used to have a large electrical enclosure integrated into its frame that housed its VFD and other controls. Since the footprint of these electronic control devices has decreased, Entek now incorporates the VFD and controls for the side feeder into an onboard extruder enclosure. With this setup, a much smaller side feeder cart can plug right into the extruder.
Bailey noted that using an open network allows Entek to tie the entire production line to one operator station. He added that remote access has been a major boon for customers. Entek has supplied a number of extrusion lines with a remote access communications box to the line, giving the OEM the ability to assist the customer remotely from its office.
Bailey said Entek's customers are requesting more automation, better diagnostics and more data that they can pass on to their customers. Although a customer may not be able to afford advanced automation or diagnostic features upfront, it can at least get started by specifying an open communications platform and single control system based on a unified platform. He advised: "Take the time upfront to make sure that whoever is putting the package together is going to put the hooks in to integrate everything."
Graham Engineering Corp., York, Pa., has leveraged PC-based technology in its extruder controls. Justin Kilgore, VP of engineering, said the company prefers PC-based controls, which he said offer the greatest performance gains for extruder customers. The company's Navigator control is a PC-based system. "There are no PLCs at all. All of the machine control and the HMI user interface is contained within a single PC," he said.
A PLC-based control entails a piece of hardware manufactured by a specific manufacturer, running an operating system specific for that hardware; typically, a software development package from that specific manufacturer is required to configure and generate control programs. A PC-based control, on the other hand, is typically a software-based control engine operating within a hardware platform modeled on a conventional PC with a common operating system such as Windows or Linux.
Kilgore referred to the PC-based Navigator control as a "soft PLC." That's because some of the programming techniques for Navigator are similar to those used by a PLC, but they're performed via software. He maintains that Navigator is every bit as robust as a traditional PLC. He noted that the look and feel of I/O modules that connect devices to the control are similar to the look and feel of PLCs. He added that the controller allows for easy remote connectivity between the OEM and the extrusion plant. The user interface offers intuitive tools, including an I/O de-bugger and electronic documentation.
Tom Vaughn, Graham Engineering's senior electrical engineer, said that the company's approach leverages the dominance of Windows-based platforms in the business market. Navigator offers users "real-time performance metrics at the machine, providing actionable items they can respond to immediately, rather than waiting for a shift report."
Graham Engineering uses EtherCAT, anEthernet-based open communications protocol. Vaughn said EtherCAT's open communications protocol facilitates easier integration of components and lowers the cost of integration.
In the last two years, Graham has implemented integrated safety modules within the I/O racks. Prior to this, all of the individual points of operation emergency stops would have to be wired together through every point of operation, resulting in long and complex wire runs. The new modules allow safety devices such as emergency stops to simply be wired right back to the nearest I/O rack. This reduces wiring costs and improves the overall diagnostic capabilities of the machine.
A DRIVE FOR DATA
Sal Spada, research director of discrete automation at the ARC Advisory Group, Dedham, Mass., said OEMs are looking for ways to provide remote monitoring for their customers. In some industrial markets, machine builders are remotely collecting operational data from their customers' machine components, analyzing performance to see if there is any outlying behavior and troubleshooting with the operator remotely. He noted that remote service experts can look at technical trends and aberrations in the data sets, and warn customers that components need to be serviced.
Although manufacturing plants are collecting more data on their manufacturing processes, many companies do not have the resources to analyze it. This provides an opportunity for OEMs, many of which provide remote troubleshooting. All of these connected services strategies can be applied to the extrusion process — or any machinery segment where there are a lot of process variables, he said.
John DeGaspari, senior correspondent
Contact:
ARC Advisory Group, 781-471-1000, www.arcweb.com
Davis-Standard LLC, 860-599-1010, www.davis-standard.com
Entek, 541-259-1068, www.entek.com
Graham Engineering Corp., 717-848-3755, www.grahamengineering.com
Leistritz Advanced Technologies Corp., 908-685-2333, www.leistritz-extrusion.com
Rockwell Automation Inc., 414-382-2000, www.rockwellautomation.com
Siemens USA, 800-743-6367, www.usa.siemens.com
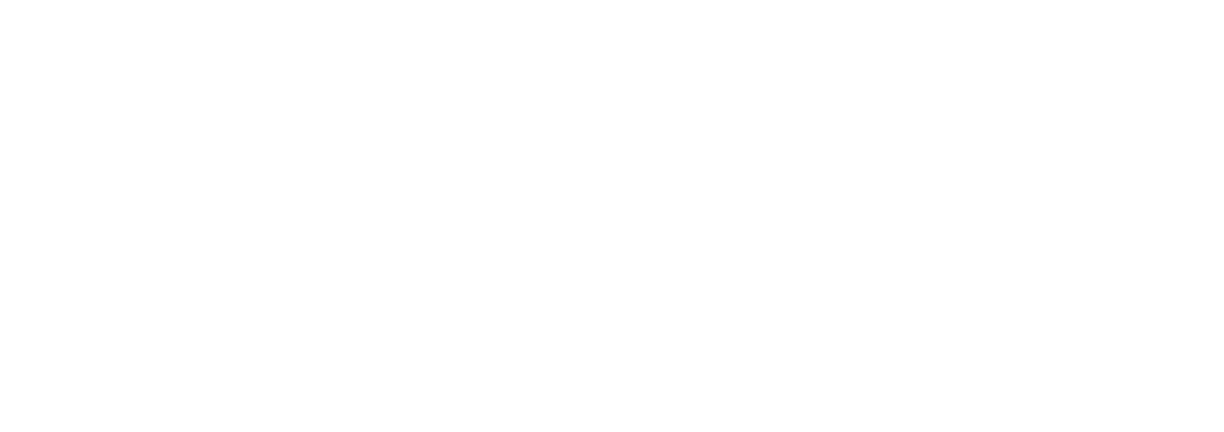