Using simulation software adapted from a system used to map blood flow in the brain, one company has improved the precision of its heat-transfer and chill rolls. It's a sophisticated method to learn how thermodynamics affects the rollers. Once manufactured, these rolls end up in film conversion facilities across North America. The goal is to have them perform to the exacting standards of Menges Roller Co., Wauconda, Ill.
"OEMs come to us all the time to do the simulations," said Matt Menges, president and owner of the company. "It's a huge opportunity for us to sell. We can help in the project design in the beginning, working with the engineers at the OEMs to provide the design that is going to work for the customer."
Film converters need the rollers for precise temperature control of the product coming off their extrusion lines. Any variation in temperature can cause problems in the extruded sheet, such as poor optical qualities or damage. Film conversion keeps growing in complexity and the demand for precision rollers grows with it. One example is the seven layers it takes to make the bag used to package Pop-Tarts. That film structure includes barrier layers for vapor, oxygen and moisture. There also are recent introductions by Toray Plastics America Inc., North Kingstown, R.I., including its oriented PP (OPP) films for non-retort pouches, which are used to package products such as dish detergent. At the retail level, what once came in boxes now is available in pouches — thanks to advances in film technologies to serve those markets. Another product, Toray's bio-based film for solar-control window film applications, is a biaxially oriented polyester made from multiple layers that have special surface and optical qualities. This film has to have low haze and high scratch resistance.
In this complex world of film production, imagine all the factors that have to be considered. These include roller dimensions, the surface of the roll face, the internal cavity fluid volume, the speed of the line and roll rotation rates. What are the properties of the steel grade being used? Also, what are the thermal transfer properties of chrome finishes? What is the angle of the spiral baffle? One has to consider the chemical properties of thermal fluids, the flow rates and pressure measurements, the properties of the web and substrates, and the ambient humidity and temperature. These factors and more are modeled by the software.
"It made us so much more precise overall and made us so much more precise in fabrication," says Matt Menges, who has brought his son, Charlie, into the business. "We knew what the roller was going to do before we made it. It takes into consideration the roller design with all these different parameters of fluid dynamics that are required."
Rollers in demand
Menges will celebrate its 50th anniversary this year. Matt Menges estimates that plastics and packaging now represent roughly 75 percent of sales. The company also makes products used in the steel and paper processing industries. During a tour of the facility in early April, Charlie Menges showed how the company is bursting at the seams, not only in the manufacture of rollers but in maintenance of the products used by its customers. The rollers have a long life once they leave the factory so rubber covering and repair are key after-market services.
The company operates in a 20,000-square foot manufacturing plant in an industrial park in a Chicago suburb, where it also owns some other buildings. The plan is to split its two core competencies of large roll core and heat transfer fabrications and its covering division that includes rubber, chrome and plasma coating capabilities between two buildings. To this end, Menges will take over a 32,000-square-foot building in its real estate portfolio.
"Every square foot is producing something," Matt Menges said. "Lean manufacturing is key."
Matt Menges has been in the business since 1984, when he started working with his father, Louis Menges. He has watched the company evolve from supplying rollers to the offset printing industry to primarily supplying the plastics and packaging industry. But offset printing is what allowed Menges to evolve into such large roller sizes today. In offset printing, each of the four color units — cyan, magenta, yellow and black — required 14 rollers.
Matt Menges said that his father Louis Menges bet the farm in the late 1970s to expand into the first roll builder and he had many factors against him, one of which was the increase in interest rates to 28 percent. He lost nearly everything — the business and even his home, but not his pride. He began again, this time with sons Matt and Glenn, who worked side by side with him. They couldn't cope with the large quantities and all the different specifications of the offset rollers so they started with large industrial rollers.
"It's funny sometimes [that] you think that your inability is a weakness, not being able to handle all the sizes and quantities of offset rollers, but that was one of the luckiest things that ever happened to us," Matt Menges said. Competitors ended up fighting over the offset roller business. Menges focused on the large rollers used in converting and plastics.
"The sheer multitude of those rollers, we started going bigger and bigger," Matt Menges said. "We started specializing in large rollers. We got good at them. The equipment to manufacture these rollers was expensive, but we put it in and learned how to buy it."
The basic roller design has one outer metal shell; then there is the double-shell, spiral baffle design, which has two shells and spiral baffles on the interior shell. The double-shell, spiral baffle design can be engineered in a mono-flow or duo-flow configuration. For mono-flow, thermal transfer fluids enter one journal bore and leave at the opposite end via another journal bore. In duo-flow, those fluids come in and out of the same journal bore. The specialty for Menges is the double-shell.
The largest roller Menges can produce is nearly 33 feet long and 48 inches in diameter. Using thermal modeling and strength tests conducted through finite element analysis, officials are focused on eliminating time in the production process and delivering what Matt Menges calls a "super-precise product." Menges applies plus or minus 0.0005 inches tolerance because the industry requires it. For the engineers who design the rollers, one aspect of testing is to study the structural design of the roller so that they can see where fatigue areas will be.
"The equipment today is doing the work of several people," he said. "We want this roller not to change from end to end by one degree. We have to keep a certain temperature. We're going to be running it at a certain rate of production."
One great year after another
There was one point in the company's history when Louis Menges couldn't get a bank loan. As it happens, a competitor in 1983 let him borrow $20,000 with which he was able to buy a new, dependable lathe to grind better-quality rolls. Louis Menges credited that loan with saving the company, Matt Menges said.
Last year, the company had its best year ever, in terms of sales and other notables, including equipment renewals. Those renewals included a 33-foot CNC roll grinding lathe with CNC crowning and grooving capabilities; a new CNC lathe for turning new roll cores 24-feet long; and rebuilds of roll covering equipment. The company also extended its roll vulcanization equipment to 33 feet. In 2014, the company won the "Technology of the Year" award from the Association of International Metallizers, Coaters and Laminators (AIMCAL) for its Computational Fluid Dynamics thermal modeling for heat-transfer roll design.
Angie DeRosa, managing editor
Contact:
Menges Roller Company, 847-487-8877, www.mengesroller.com
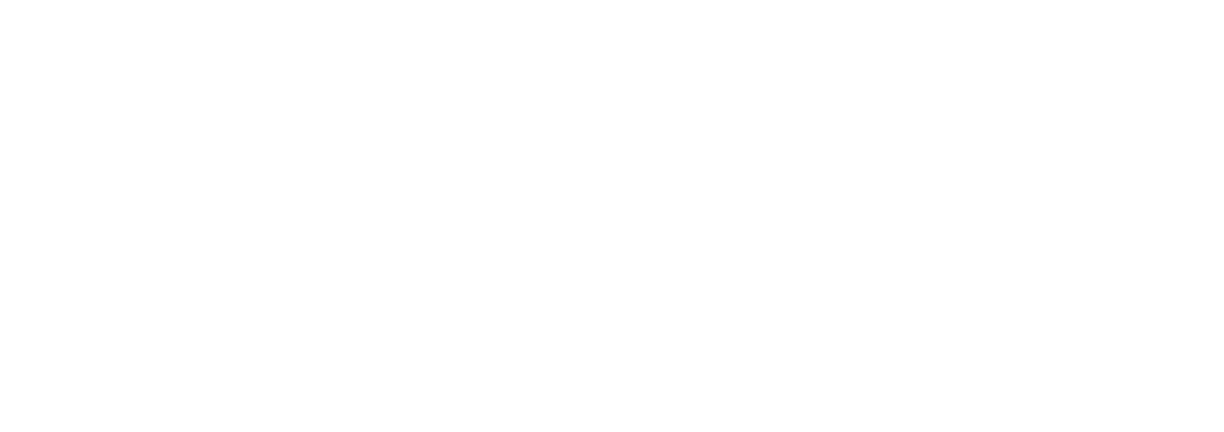