Compression molding has been around a long time. But the method of using heat and pressure to form a part is being adapted with the times and managing to still find growth opportunities.
"We are building more compression molding machines for customers that want the machine itself to be more precise, more repeatable, [have] less downtime, and then have everything be recordable," said Josh Dixon, director of sales and marketing for Beckwood Corp., Fenton, Mo.
At French Oil Mill Machinery Co., Piqua, Ohio, demand for compression molding machines is trending up because of advances in materials and processes, said Dave Sledz, hydraulic division VP. In the past, compression molding was mostly limited to the aerospace industry, because of the cost. But now materials advances have allowed it to be increasingly employed by the automotive, recreational and medical markets, among others. And the aerospace market is expanding.
To meet increasing demands for temperature uniformity of the platen surface, Beckwood employs a multizone heat control technology. It also now builds every compression molding machine with a data recorder to register time, as well as to measure the temperature of each heating zone, the mold and sometimes even the part. "And those will oftentimes be graphed and exported to customer networks for traceability," Dixon said.
That capability also is a key factor for French Oil. "Certain industries, [such as] aerospace, need 100 percent traceability. Our control systems allow that. For each cycle, for each part, we know times, temperatures, deviations, things like that," said Sledz.
In compression molding, the amount of time the machine is applying pressure to the part is known as the dwell cycle. To increase energy efficiency, Beckwood offers a pneumatic dwell system that allows the shutdown of the main hydraulic pump and motor through the cycle. "It's a huge energy consumption advantage as well as just noise decrease," Dixon said.
Compression molding is suited for a wide range of applications, he said. About 10-15 percent of the company's business is with the plastics industry, from thermoplastics for the aerospace industry to the Mr. Clean Magic Eraser consumer cleaning product.
Compression molding applications have evolved with technology changes over the years, and many migrated overseas as they became relatively low tech. The use of composites represents a growth opportunity, said Dave Singer, sales and marketing manager for Wabash MPI and Carver Inc., both in Wabash, Ind. Aerospace has been a strong market for composites for some time. But that is broadening. He said demand for the use of compression molding is growing among more mainstream industries, with applications in the automotive and energy segments. "As the materials get developed at higher temperatures and higher [pounds per square inch], some of them are more applicable to a compression molding application than other means of processing."
Both Wabash and Carver make presses for a variety of applications at the Wabash facility. Wabash focuses mainly on manufacturing applications, while Carver's equipment is designed primarily for laboratory uses.
French Oil is seeing a good number of its customers perform resin transfer molding with compression machinery. The use of compression machinery with material that is pre-impregnated with a resin is also growing. The developments take advantage of French Oil's thermal management experience and its Uni-Temp platens and edge controls. "So we're applying some existing technologies that we've known for years and that we're currently developing, and then applying these to these different processes, also," Sledz said. For this approach, French Oil makes the Techni-Mold hydraulic composite molding press series, which is appropriate for use with rubber, silicone and composite materials.
With advances in materials and processing, compression molding can now replace injection molding and autoclaving composite parts in some cases, said Ben Halford, chief executive at Surface Generation Ltd., Oakham, England.
The company said that its customers are focused on reducing the cost per component. The company's U.S. subsidiary, Surface Generation America, is located in Fort Worth, Texas.
"Users want fiber-reinforced products that are net [final] shape with injection molding finish," said Halford. "To achieve this, equipment manufacturers and materials suppliers are deconstructing the traditional single-station, compression molding process to create lines with separate loading, pre-heating, molding, cooling and ejection stations." That eliminates bottlenecks and allows the user varying degrees of automation.
Sacmi Imola S.C., Imola, Italy, said it is seeing growing use of its Cool+ molds, a modified liquid-coolant circulation system inside the mold that ensures all parts in contact with the plastic are cooled. The system cools better and in less time than comparable technologies, said Iacopo Bianconcini, Sacmi beverage marketing manager, closures and containers.
While virtually any part can be made through compression molding, several factors dictate the process' use, French Oil's Sledz said. Considerations can involve the shape of the product, and the quantity and cost of materials. "To inject a part obviously is much faster than compression molding it, but some particular parts, due to size or materials, aren't potential candidates for injection. I would say the shapes and the materials force you into one particular type or the other," Sledz said.
Compression molding is better suited for larger shapes, Sledz said. But size also can limit the value of the process, as can automation, cycle time and part shape.
The biggest challenge for compression molding is its lengthy cycle time, Dixon said.
Sacmi finds the technology limited, as far as design options, when it comes to containers with hinged or sports-drink caps. And Surface Generation points to limitations involving material format and flowability. "For high-volume work, this is problematic," Halford said.
Singer describes the compression molding market as steady for the most part, with slight growth. He said he believes that as parts get bigger, there's a demand for larger presses and larger platen sizes. "Some of the newer energy technologies will bring new opportunities for the compression molding market."
Compression molding equipment prices are becoming more competitive, added Sacmi's Bianconcini.
Beckwood's Dixon said demand for the company's plastics machinery is holding steady, while interest is increasing in other markets. He sees growth in the aerospace, automotive and military markets, as well as in applications using composites.
Surface Generation is seeing widespread inquiries on compression molding, with strong demand for lighter, thinner products. Growing use of thermoplastics is also generating a strong market push, Halford said. Built to handle thermoplastics and thermoset composites, the company's new Multiplexing system integrates multiple stations for material loading, infrared preheating, molding and demolding.
Comparing European compression molding equipment to American, Sledz said the Europeans are somewhat more advanced in providing systems rather than a single machine. "Where we might do a press, the Europeans might be a little more aggressive when providing a whole turnkey system. But the requirements are now starting to drift down from aerospace to other industries." Surface Generation's Halford said compression molding's popularity depends on the sector and geographic region where it is used. "We are seeing particular demand for new compression molding techniques from aerospace manufacturers in North America, while in Europe it tends to come from automotive companies," Halford said. "In Asia, we see most demand from consumer electronics manufacturers."
For Sacmi, the Asian and Middle Eastern markets represent greater demand than Europe, Bianconcini said. That's because large European cap converters were already operating when Sacmi entered the market, making it harder for the company to gain business. But he said the market is changing.
Dixon said about 20 percent of Beckwood's business is overseas.
And Wabash/Carver has seen export growth in Europe and particularly Russia. "A lot of that growth is into the laboratory side to our business. Small types of machines for R&D, that kind of thing," Singer said.
Allan Gerlat, correspondent
Contact:
Beckwood Corp., 636-343-4100, www.beckwoodpress.com
Carver Inc., 260-563-7577, www.carverpress.com
French Oil Mill Machinery Co., 937-773-3420, www.frenchoil.com
Sacmi USA Group, 515-276-2052, www.sacmiusa.com
Surface Generation, 972-699-9976, www.surface-generation.com
Wabash MPI, 260-563-1184, www.wabashmpi.com
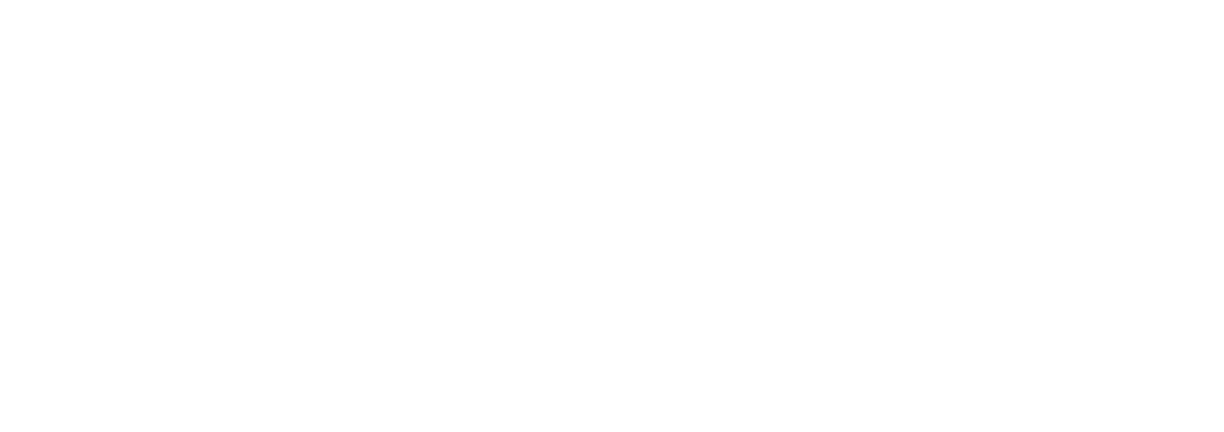