A pulverizer takes pellets in one end and produces powder at the other end. It is often used to get virgin resin ready for rotomolding, or for modifying material for rotomolding, by adding color, for example. A pulverizer also can take scrap in one end and deliver powder out the other for recycling.
Pulverizer suppliers provided details about recent updates to their products.
Powder King introducesPKA Velocity
Powder King LLC, Anthem, Ariz., in March launched its PKA Velocity pulverizer, the fourth generation of pulverizers for the company, said owner and President Jim Hummel.
The new model is suitable for recycling applications as well as for producing powder for rotomolding, achieving throughputs of up to 2,000 pounds of PE per hour for the latter application, he said.
The pulverizer features a direct-drive mill to utilize 100 percent of the power from the 150-horsepower motor. The motor is driven by an inverter drive mounted into the control panel of the machine. To prevent expensive spikes in electrical demand, the inverter drive draws only 50-55 amps at startup, the company said. The inverter drive also adjusts the speed of the mill's discs, to accommodate different resins.
Integral platforms allow operators to access the different machine levels, and completely guarded sifters protect workers from the moving sifter boxes. Designed for easy cleaning, Velocity also has heavy-gauge pipe with O-ring sealing clamps to ensure that powder won't leak. The machine has touch-screen controls.
The new design has dual air inlets to improve air cooling of the mill chamber, and dual material outlets on each side of the mill to remove material quickly and reduce heat buildup, Hummel said.
Reduction Engineering
Reduction Engineering Scheer, Kent, Ohio, recently added several new tooth configurations to its pulverizers to maximize throughput and improve quality for a wide variety of plastics, including temperature-sensitive materials such as PP and PS, a company representative said. Traditionally, such materials are processed cryogenically. While throughput varies by material type, on average the new configurations yield a 15 percent increase in throughput for temperature-sensitive resins.
The company also has found strong success with its disposable cutting discs. They have double the service life of standard discs at half the cost. Made of a wear-resistant alloy, each disc weighs 15 pounds, compared to 60 pounds for a previous product. The disc is also 75 percent thinner. A larger diameter improves throughput and a larger inlet allows for more efficient cooling.
The life-cycle cost is about half that of standard discs, when taking into account the repeated expense of shipping the discs for sharpening. Reduction Engineering Scheer has installed the disposable discs in 20 percent of its pulverizers worldwide.
One customer, Aaron Industries Corp., Leominster, Mass., said the disposable discs have been a money-saver. The long life, the ability to make quick changes and the different blade styles allow the company to be flexible with very little downtime, plant manager Joe Firmani said. "They provide us the opportunity to do many different polymers, and more importantly, we are able to experiment with new polymers without tying up cash with more expensive blades that require sharpening," he said.
Herbold Meckesheim USA
Herbold Meckesheim USA, Slatersville, R.I., recently upgraded its SMF fine granulators to make them more effective for pulverizing difficult materials. Herbold now offers 12 options for the number of rotating and stationary knives, ranging from the S5 model with a five-knife rotor to the F16, which has a 16-knife rotor, said President David Lefrancois.
A screen beneath the grinding chamber allows the material to pass through when it reaches the correct size. New screen options include square, round or slot-type holes, as well as Conidur-brand screens, allowing the granulators to accommodate a wide variety of materials, including plastic chips from the production of pipes and profiles, plastic fibers, foam, film and rubber. An open rotor design allows the maximum throughput of cooling air. Throughput is up to 4,400 pounds per hour.
Zerma
Zerma North America, Crystal Lake, Ill., completely redesigned its PM disc pulverizers about a year ago. The PM units are used for processing PE for rotomolding applications and for pulverizing PVC regrind for pipe and profile recycling. They are designed to work inline with a shredder and granulator to handle production waste.
Each machine has a vibratory feeder, two cutting discs, a process cooling system and a material take-off system. One improved feature is that instead of cooling the machine housing, a water jet system cools the discs, allowing for a larger surface area on the discs, and thus for higher throughput with lower energy use. Optional features include metal separators, rotary valves, an auto-feed system and screens for size control.
Pallmann
Pallmann Industries Inc., Clifton, N.J., manufactures pulverizing systems for the international market. Pallmann takes credit for inventing equipment for pulverizing heat-sensitive plastics at ambient temperatures. The PolyGrinder system, type PMM, is used for pulverizing thermoplastics for masterbatch and compounding operations without the addition of cooling agents such as liquid nitrogen.
The system can process up to 3,300 pounds per hour. It is used for producing high-quality powder from PVC and PE, as well as difficult and heat-sensitive materials such as EVA, PP, nylon, polyester and PC.
The combination of a minimum-maintenance drive concept, a simple-to-clean interior and the quick adjustment of the grinding gap results in economical operation. Because of its compact design and the fact that it can be installed without a base frame, PolyGrinder can be easily integrated into existing production lines.
Merle R. Snyder, senior correspondent
Contact:
Herbold Meckesheim USA, 401-597-5500, www.herboldusa.com
Pallmann Industries Inc., 973-471-1450, www.pallmannindustries.com
Powder King LLC, 623-551-9897, www.powder-king.com
Reduction Engineering Scheer, 330-677-2225, www.reductionengineering.com
Zerma North America, 815-477-2800, www.zerma.com
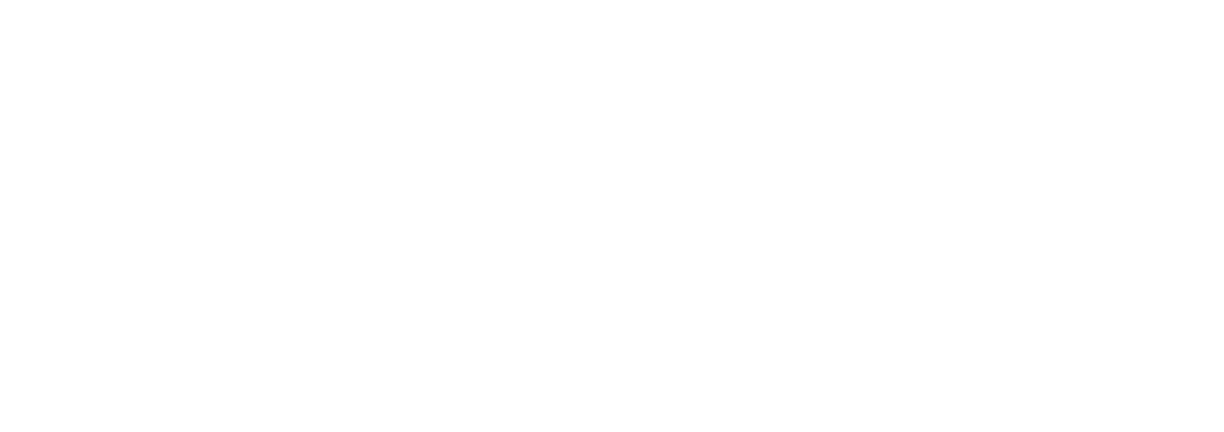