Special Report: Automated functions improve monitoring for injection molding
Two prominent suppliers of process monitoring systems for injection molding have optimized process quality and simplified ease of use through innovative software and hardware upgrades.
NEW TOOLS MINIMIZE PROCESS FLUCTUATIONS
The ComoNeo process monitoring system from Kistler Instrument Corp., Novi, Mich., is designed to lower production costs for injection molders through analysis and optimization of their processes. Introduced last year at Fakuma in Germany and now commercially available in North America, ComoNeo quickly identifies process fluctuations by monitoring cavity pressure.
The ComoNeo system is a hardware and integrated software upgrade to Kistler's Como injection system, which it replaces, sales representative Rich Marinucci said. ComoNeo can monitor and evaluate up to 128 injection molding process variables relating to the mold or the machine to minimize scrap production.
New and enhanced software tools ease system configuration and operation, while several other aspects have been automated, including the calculation of key process parameters and the detection of process interruptions. Screens have been added to monitor windows for good/bad part evaluation and mold identification. In addition to the enhanced process monitoring capabilities, ComoNeo also can be used for production monitoring and mold trials.
To facilitate mold monitoring, ComoNeo has 32 cavity pressure sensor inputs and 16 cavity temperature sensor inputs — twice the number previously available. This allows tooling with more cavities to be connected to the monitoring system.
For machine monitoring, ComoNeo has up to 12 digital inputs and up to 24 digital outputs, and is able to analyze and document four molder-selected analog machine signals, such as screw position or machine pressure.
Kistler developed a new user interface for ComoNeo that displays process trends, production and mold-related information and other relevant data. Up to 50,000 mold cycles — equivalent to about five days of production — can be archived through an integrated data-storage function. The system can present an overlay of a cavity pressure-profile curve (by overall process cycle or by cavity) to display a visual representation of process stability or fluctuation. Users can enter settings and view data from the dashboard through a touch-screen display.
ComoNeo features a new function called the EO Assistant, which allows the injection molder to determine the range within a cavity-pressure curve that corresponds to good or bad part production. Once the process is set up and the upper and lower limits are defined, EO Assistant acts as a quality monitor, said Daniel Fick, Kistler's product manager for the plastics strategic business field. Using this approach, he said users can carefully monitor components and limit the production of unacceptable parts.
ComoNeo has several operating modes, including setup, production and standby. The system can forecast when a production run will end, culling information from each cycle and taking scrap rates into account. When in production mode, the unit can detect when the process has stopped and whether the machine is idle. Following a production restart, ComoNeo can determine the number of cycles in which scrap parts are being produced.
ComoNeo can be integrated into a plant network, or all measured data and evaluations can be transferred to the Como DataCenter, according to Kistler.
GREATER FUNCTIONALITYAT THE PRESS OF A BUTTON
Priamus System Technologies LLC, Brunswick, Ohio, offers Q-Button, a new process optimization function for its FillControl line of monitoring and control products. Q-Button allows molders to calculate and set process values, default settings and monitoring limits for all injection molding process parameters automatically. Q-Button simplifies and shortens monitoring set-up time, regardless of the number of monitoring functions and channels involved, said Marcel Fenner, president and technical manager.
"It can be quite time-consuming for a molder with many sensors in place to set up tolerance limits for each parameter they are looking to monitor. Molders have had to determine target values and establish limits manually," Fenner said. A molder would have to determine ideal upper and lower tolerances for each process parameter. It is not uncommon for a molder occupied with getting the process to a steady state to forget to set the tolerances, he said. Q-Button calculates monitoring parameters as well as Six Sigma quality-control parameters to establish tolerance limits across all monitoring functions. A user also can manually set values.
Q-Button is accessed through a touch screen, which shows a button with four buttons encircling it. The outer buttons allow the molder to adjust FillControl functions: One corresponds to Priamus' Process monitoring software (FillControl Monitor); one relates to the company's process control system (FillControl P); one gives access to Priamus' hot-runner balancing system (FillControl H); and one has no assigned function on the main screen but is used in other screens of the Q-Button system.
When a molder presses one of the outer buttons, values relevant to that FillControl program appear within the buttons. If the button relating to FillControl Monitor is pressed, the molder can view and adjust an integral value, a maximum value, cavity mold temperature and viscosity. If FillControl P is selected, the molder can set values for compression and shrinkage. If FillControl H is selected,
maximum fill-time difference and maximum fill-time deviation are displayed, Fenner said.
A color scheme indicates conditions. Users can tell at a glance if the process is producing good parts (green); is producing good parts but is trending toward the edges of set limits (yellow); is at the threshold of set limits (orange), or is out of tolerance and making bad parts (red). Buttons labeled "maximum" and "integral," accessed through the FillControl Monitor function, can be assigned a value, such as a maximum voltage or a temperature or a pressure signal.
Users can program a visual or audible signal to indicate when a process variable is trending out of tolerance, Fenner said. Overall, the molder can adjust 16 critical parameters manually, Fenner said. A molder with an eight-cavity tool has the option to input a value for each function for each cavity.
Automated optimization of the aforementioned parameters is achieved by pressing the central button. The molder brings the molding process into a steady state, allows the press to operate for 25 or 50 molding cycles, then pushes the Q-button. It calculates the monitoring limits based on the process variation. It also calculates the parameters needed to meet Six Sigma requirements. The preset values established with Q-Button are then applied to each succeeding cycle.
"The width or narrowness between the upper and lower limits of a value provides a glimpse into the stability of a molder's process. The narrower it is, the tighter the process. Six Sigma is the tightest of the tolerance gap," Fenner said. Molders can use the system to detect whether their process is stable or drifting.
Mikell Knights, senior correspondent
Contact:
Kistler Instrument Corp.,
716-691-5100, www.kistler.com
Priamus System Technologies,
877-774-2687, www.priamus.com
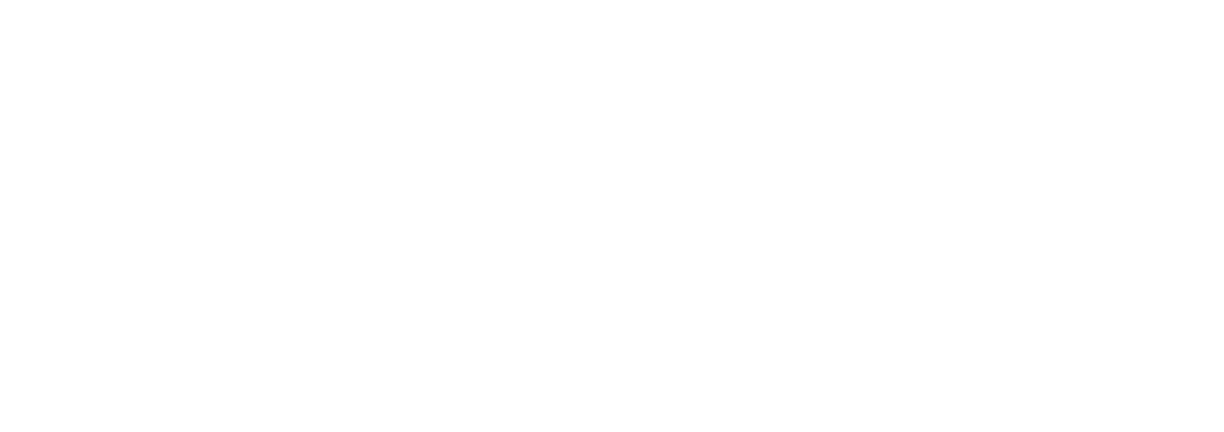