Manufacturers of recycling machinery are worried that depressed prices for resin are hurting machinery sales, but Germany's Vecoplan AG said that its North American market is strong and has shown no signs of slowing.
Jörg Müller of Vecoplan AG
"In general, we finished 2015 on budget," said Jörg Müller, director of business development for Vecoplan AG, Bad Marienberg, and president of Vecoplan LLC, the U.S. subsidiary based in High Point, N.C. "The U.S. market was absolutely great."While a favorable exchange rate helped, Müller said the company's strong market position in the U.S., where it had sales of more than $50 million for all products, played a big part. Overall, Vecoplan reported worldwide sales of $105 million in 2014, and expects to announce sales of more than $110 million when it releases its 2015 report in a few weeks. Vecoplan does not break out sales of plastics-related equipment.
Vecoplan divides its business into units for recycling, waste and wood. Plastics falls into the recycling business unit, along with paper recycling. Each segment generates approximately one-third of Vecoplan's total sales. In the U.S., plastics equipment is the largest segment, followed by paper and wood recycling machinery.
The company's core products are shredders, conveyors, screens, separators, storage silos and dosing and feeding products.
Müller said that the low prices recyclers are currently getting for their reclaimed resin is making them hesitant to invest in new equipment. "Nobody thinks that resin prices will stay low. Long term, recycling makes sense," Müller said. "But right now it is not on the peak that it was."
The key to staying ahead of the competition is to continue to invest in research and development for new products, he said. "You cannot survive when you are not in a low-cost country unless you keep developing new, state-of-the-art products. You have to stay two to three steps ahead of the competition."
Bob Gilmore, managing director and chief sales officer of Vecoplan in the U.S., said his customers are taking more time to educate themselves about the equipment and company that makes it before they purchase. "People are going after the smart purchase," he said. "This actually helps us because Vecoplan is a higher-quality choice."
Vecoplan makes equipment for all recycling applications, from small units used by processors to handle in-house plastic scrap to large recycling facility systems. It developed its first shredder in 1969 for shredding wood and entered the plastics recycling market in 1989 by adapting its VAZ shredder for plastics. The VAZ is still in Vecoplan's inventory.
Customers are asking for more effective plastic shredding equipment so Vecoplan is focusing research on difficult-to-shred materials such as film and fiber materials. "There is good demand in the area where conventional size-reduction equipment fails," Müller said.
"We are also expecting — but we don't yet see it — that when material recovery facilities (MRFs) become more sophisticated and have better sorting capabilities to produce cleaner plastics streams, there will be a demand for shredders that can handle more contaminated plastics," he said.
Vecoplan introduced the V-Eco single-shaft shredder in a range of four sizes last year and it has proven to be very successful. It is designed to shred a wide range of rigid and flexible materials, including all plastics, films, fibers, paper, cardboard and textiles. Thirty-three V-Eco shredders were sold last year.
The V-Eco uses a variable-frequency inverter drive that eliminates gearboxes and fluid couplings, can be configured with a single or double row of bed knives, and has a hydraulic lift-up cutting chamber floor and drop-down screen carriage providing quick access for screen changes. The design minimizes heat generation and produces particles of consistent size.
"The V-Eco is blurring the lines between a traditional shredder and granulator," Gilmore said. "You are able to drop an entire bale of post-
consumer bottles into the V-Eco and produce
granulator-quality flake. The typical process would be to shred, convey, then granulate, or to break those big bales apart and feed them into a granulator. The 'dump-and-run' convenience of the shredder is a big benefit."
Gilmore said that the U.S. market is experiencing strong growth in large shredders that can process 50 tons or more of material per hour. One current project has Vecoplan installing shredders and auxiliary equipment at a plant in Reno, Nev., being built by Fulcrum BioEnergy Inc., Pleasanton, Calif. The plant, which has one acre under roof, will take in 100 tons of waste products per hour and convert the materials, containing a high percentage of plastics, into jet fuel.
The Fulcrum plant is a $12 million project for Vecoplan, which designed and engineered the system that takes incoming waste from the loading dock and prepares it for conversion to fuel. Vecoplan's system utilizes conveyors, pre-shredders, waste screens, wind sifters, over-belt magnets, eddy current and non-ferrous separators, picking stations, three-way optical sorters, dust collection systems, balers and integrated controls.
The Fulcrum project is one of the largest of six waste-to-fuel projects Vecoplan has been involved with in the past six years.
Müller said recyclers are also pushing for better washing technology. In 2015, Vecoplan introduced the HydroDyn washing system that uses the dynamic properties of water spun in a cyclonic fashion to generate friction and clean plastic flake suspended in the water. It is a closed system, with the heat generated through friction producing a hot wash system with no additional power or gas. Two systems have been installed thus far — one in Bulgaria and the second in northern Germany. Recyclers from the U.S. have visited the plant in Bulgaria, and Vecoplan expects it to become a popular system in this market.
"The customers are happy. The purity of material they are making sets a new standard never reached before," said Müller. "The market will pay for that quality. Other companies are now interested in the product." He said a wash line takes a long time to sell and install, but Vecoplan is optimistic about the product.
Vecoplan in North Carolina performs final assembly of shredders that are manufactured in Germany. Some components and the auxiliary handling equipment are manufactured in the U.S. Allen-Bradley controls, which Müller said are generally preferred in the North American market over the Siemens controls favored in Europe, are added in North Carolina. Steel enclosure panels are sourced in the U.S.
Worldwide, Vecoplan has the capacity to deliver more than 700 shredders a year.
In Germany, Vecoplan sources everything it needs within a 25-mile radius of its factory in rural Bad Marienberg. "The key is that we can do up to 95 percent of everything we need to do in-house, but we never do," said Müller. "We use smaller, specialized companies around us. It makes us more flexible to be able to do it in-house during normal times but send it out during peak times."
Vecoplan, which has about 450 full-time employees worldwide, said it uses more than 43 tons of steel every day to build its equipment.
In late 2014, Vecoplan opened a technology center at its German headquarters. On a recent visit, it was jammed with recycling equipment of all types and sizes; some machines were running customer tests. Vecoplan's test lab in North Carolina was refurbished this year with the installation of the company's latest technologies.
"No one asks for components anymore," said Martina Schmidt, sales director for the recycling business unit in Germany. "They ask for solutions. This technical center helps us demonstrate solutions."
She said energy savings and flexibility are two big items on her customers' shopping lists. The new HydroDyn washing system, for example, is designed to be energy efficient and is built on a modular design.
The HydroDyn system is built on platforms that come with the system, eliminating the need for on-site bases or other foundations for individual pieces of equipment. Piping, electrical wiring, drainage and all components are mounted on the platform chassis. The platforms can be shipped by truck or container and on-site installation requires only water and electrical connection.
"Now we are thinking about how we can make other components more modular," she said. "Our customers need to be able to change their equipment around for different applications."
Ron Shinn, editor
Contact:
Vecoplan LLC, 336-447-7665, www.vecoplanllc.com
About the Author
Ron Shinn | Editor
Editor Ron Shinn is a co-founder of Plastics Machinery & Manufacturing and has been covering the plastics industry for more than 35 years. He leads the editorial team, directs coverage and sets the editorial calendar. He also writes features, including the Talking Points column and On the Factory Floor, and covers recycling and sustainability for PMM and Plastics Recycling.
June 24, 2025
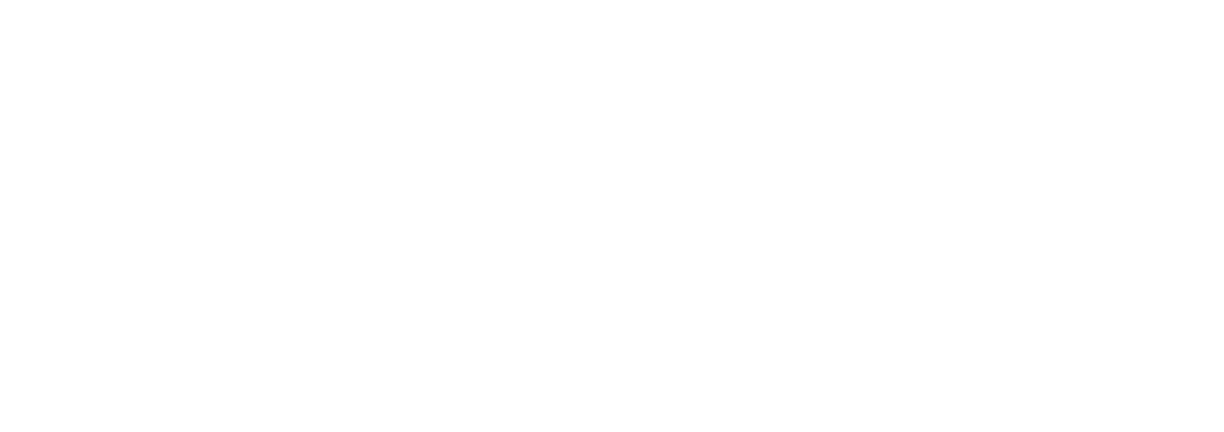