Special Report: Clean-room regulations keep conveyor makers in motion
Chipping paint, swirling dust, dripping grease — these are not concerns for conveyor operators in all molding facilities. But they are deal-breakers within a clean room, say representatives of conveyor manufacturers.
Reducing the potential for contamination is key. Like other equipment within a clean room, conveyors can be subject to safety regulations issued by agencies such as the U.S. Department of Agriculture (USDA) and Food and Drug Administration (FDA). Clean-room conveyors must be resistant to static and corrosion, and designed in such a way that they can be easily cleaned, says Mike Loin, application engineer/sales manager, TEC Engineering Corp., Oxford, Mass. TEC conveyor systems reduce or eliminate particulates, static electricity and particulate adhesion. TEC can install deionizing air knifes or catch trays to prevent particles from entering the environment.
"Our conveyor belts are monofilament anti-static or plastic modular running on a stainless-steel belt pan. Ultra-high molecular weight (UHMW) polyethylene strips are installed between the belt and frame creating a low-friction, particle-free zone," Loin says.
John Schanz, sales manager for Harvard Factory Automation Inc. (HFA), Harvard, Ill., points out some other considerations for conveyors in clean rooms. For example, he says, "You must make sure the framework is not painted, and everything rotating should be sealed — motors, belt drive, bearings, etc." Proper FDA-approved PU belting must be used, he says. Grease fittings are not appropriate.
Additionally, Raul Reyes Jr., regional sales manager/customer service manager for MAC Automation Concepts Inc., Woodstock, Ill., recommends HEPA filters. "High-efficiency particulate air (HEPA) filters are the most common means of controlling contamination with reasonable rates of effectiveness." HEPA filters range in efficiency from 99.997 percent to 99.9999 percent or better, Reyes says. HEPA blowers create positive air pressure within an enclosure to prevent the introduction of contaminants, Reyes says.
Adding HEPA filtration to the conveyor can reduce particulates dramatically. "When anti-[static] units and HEPA filtration modules are added, it becomes its own little 'mini-clean room,' " Schanz says.
Some of the clean-room conveyor options provided by the following companies are:
• EMI Corp., Jackson Center, Ohio: Standard features are aluminum framing and stainless-steel guarding and legs to resist corrosion and eliminate paint-chip contamination; USDA/FDA-approved belting material; open-construction slide bed with UHMW PE contact strips to eliminate places where abrasive debris can collect; a direct-drive motor in lieu of a chain and sprocket; sealed bearings to reduce the chance of lubricant leaks; and control wiring contained in liquid-tight conduit. Common options include stainless-steel framing; sealed belt edges to minimize dust from belt fraying; plastic modular easy-clean belting that eliminates friction contamination;
wash-down compliant electrical components; USDA/FDA-approved side-rail lining; a maintenance-free, eco-friendly gearbox lubricated with food-grade grease to prevent contamination from leaks; deionizing blowers to eliminate static; and catch trays to prevent particulates from escaping into the environment.
• TEC: Aluminum framing with custom stainless-steel side rails or stainless-steel framing and side rails for ease of cleaning and corrosion resistance; FDA-approved, easy-to-clean belting in white or blue; plastic modular belting that can be easily cleaned; and direct-drive motors and sealed bearings to reduce the chance of lubricant leaks.
• HFA: Anodized aluminum framework; FDA-approved PU belting; Lexan covers; paint-free components; sealed motors and bearings; anti-static units; HEPA filtration; and other options.
• MAC: High-strength, anodized extruded aluminum, stainless-steel and powder-coated steel construction; FDA-approved, anti-static belting available in plastic link modules; stainless-steel wear strip;precision-machined, trapezoidal-crowned, stainless-steel pulleys to provide belt tracking and reduce contamination; energy-efficient, variable-speed ionizer to eliminate static electricity; photo eye stop to stop the conveyor when the beam is interrupted; emergency stop with reset button that can be plate- or remote-mounted; AC and DC indexing control packages, so the conveyor runs for a user-defined time interval; reversibility for mounting either an external or internal motor; metal detector with automatic stop and optional alarm on detection; and adjustable telescoping leg supports.
Lisa Jo Lupo, correspondent
Contact:
EMI Corp., 216-535-4848, www.emicorp.com
Harvard Factory Automation, 815-943-1193, www.hfaconveyors.com
MAC Automation Concepts Inc., 815-337-3000, www.macautomation.com
TEC Engineering Corp., 508-987-0231, www.tecautomation.com
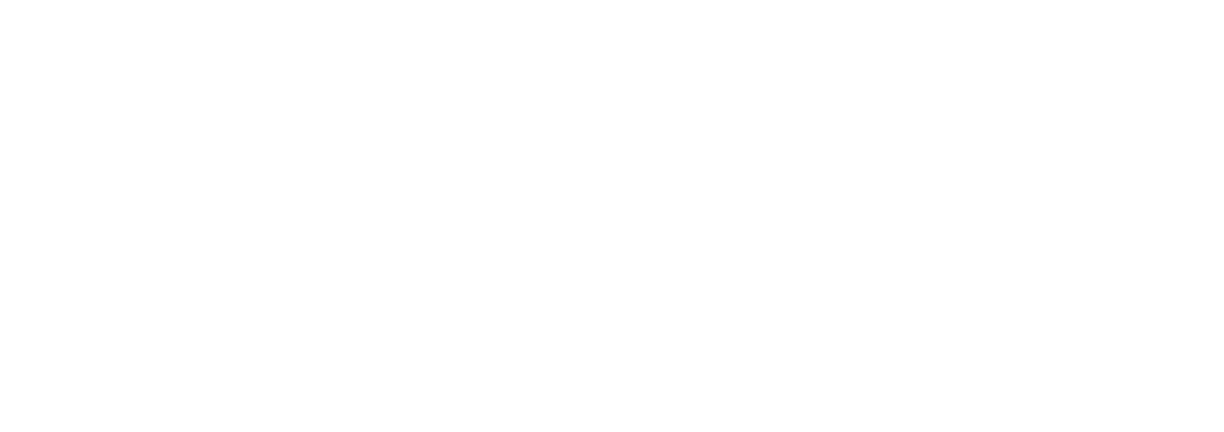