Special Report: Companies tout range, price of latest temperature controllers
New and established suppliers of hot-runner temperature controllers have rolled out new process-enhancing capabilities.
VULCAN HOT-RUNNER CONTROLLERS
Vulcan Hot Runner Controllers, El Paso, Texas, a new supplier of no-frills hot-runner controls, launched its first commercial modular controller in January, says David Crain, VP of sales.
The company, established in May, manufactures its equipment without premium features such as flat-panel displays, or functions like archiving and retrieval of production settings parameters. Instead, toggle switches, button-style function keys and LCDs for each heating zone comprise the essential elements needed to operate the system, says Crain. He recognized the industry's need for such a unit while working for five years at Husky Injection Molding Systems Ltd. In all, Crain's career includes 25 years in sales for the injection molding industry.
Vulcan says its hot-runner controller is offered complete with mainframe, modules, connectors and cables. The controller is manufactured under a private-label agreement with a supplier in Shanghai.
"We wanted to bring a robust, high-performance, low-cost unit into the marketplace that has a low component failure rate, which would lower warranty costs, yet we did not want to go into manufacturing," says Crain. "We found a company in China that for the past decade adopted hot-runner manufacturing methods common in the U.S., and also used high-quality components to build their hot-runner controllers."
To ensure high quality, the manufacturer follows Underwriters Laboratories (UL) and European Conformity (CE) standards for wiring and electrical runs. It performs electronic component assembly and testing in-house and in a clean room, in a manner similar to U.S. methods, says Crain. The controller is built using components familiar to North American molders, including a central processing unit (CPU) and information-control devices sourced from Microchip Technology Inc. and Motorola; transistors and diodes from Toshiba; capacitors from TDK Corp. and resistors from Samsung.
Vulcan's new YK-D model is offered with one to 96 heating zones, although the most common constructions don't have more than 48 zones. Temperatures can be set from 110 to 1,000 degrees Fahrenheit, with accuracy of plus or minus 0.5 degree Fahrenheit. Basic functions include soft start, temperature unit setting, thermocouple setting, high- and low-temperature alarm settings, temperature boost for fast heating, temperature correction and output power control. Automatic, manual and standby control modes are standard and are displayed through indicator lights.
During the past nine months, Vulcan has shipped numerous six-zone and 12-zone controllers as a beta test to proprietary and custom molders and mold makers that serve a diverse range of end markets, including automotive and electronics. The YK-D can be configured for use with any hot-runner system. Vulcan stocks the controller at its warehouse in El Paso, Texas.
Vulcan planned to debut the YK-D at the Plastec West show in Anaheim, Calif., this month. The company plans to develop other mold-related technologies this year, starting with an ultrasonic mold-cleaning unit.
HUSKY INJECTION MOLDING SYSTEMS LTD.
Husky Injection Molding Systems Ltd., Bolton, Ontario, has upgraded its Altanium family of hot-runner temperature controllers with a new control card that delivers better zone control, troubleshooting and diagnostic features, as well as a new capability to control movements within the mold that are driven by servo motors.
The Altanium series includes the Neo2, a cost-effective controller for two to 48 zones of temperature control, the Delta3 premium performance controller for up to 128 zones, and the Matrix2 high-end controller for up to 254 zones. Now, that series incorporates an H series control card. The new card is able to handle double the number of temperature zones as the previous X and XL Control Card series it replaces, in the same amount of space, meaning the size of the controller doesn't change, says Matthew Cummings, product manager for Altanium.
"When a molder moves into higher-cavitation tooling, they typically need one zone of control for each nozzle heater and one zone of control for each manifold zone," he says. A larger manifold serving a mold with more cavities usually requires more heating zones, prompting the use of a physically larger controller with added control cards. The H series card handles four zones per card.
In addition, mold diagnostic and troubleshooting features deliver a premium level of control and traceability, including a faster, more accurate analysis of problems. System diagnostics automatically test individual or multiple zones for voltage delivery to each heater, thermal response and the electrical wiring, thermocouple status and power usage. The upgraded diagnostic and troubleshooting features are a benefit to molders of hard-to-process materials for the automotive and medical industries, says Cummings.
Husky also added a servo control function to the Altanium line that can control valve-stem motions, slides, unscrewing or core movements where the power source is servo rather than pneumatic, hydraulic or mechanical. The customizable servo control allows users to achieve mold qualification more quickly with greater reliability and repeatability.
"Because the controller is in communication with the servo motors, it detects anomalies in the process and can halt production, preventing damage, and servo-controlled mold movements are more programmable, precise and repeatable," says Cummings.
Altanium Servo Control is designed to control up to six servo axes, and it can work with a wide range of servo motor types, which Husky or the molder can select. It uses Husky's hot-runner temperature and valve-gate control, and offers simpler process setup, adjustment and traceability when a servo motor is incorporated into the mold. "The benefit to the molder is that commissioning a mold takes drastically less time since the temperature controller and mold movement are coordinated through a single interface," says Cummings.
The use of an Altanium unit with servo control allowed a Husky customer to more consistently produce a medical part in a multicavity tool that incorporated a membrane created via a coining step. The coining step, previously achieved with hydraulic actuation of a coining pin located on the cold half of the tool, generated scrap parts if the pin did not actuate to the correct position. Before adopting the servo control, all parts made since the last control check would be scrapped when the molder discovered part failure. In those instances, manual inspection of each part was necessary until the operation produced a steady stream of good parts.
"With servo control, the process halts the moment a deviation in pin operation occurs, minimizing the production of failed parts while pinpointing the source of the trouble," says Cummings. The Altanium servo control brings part inspection into the process, and the molder no longer inspects parts manually.
GAMMAFLUX LP
The prevention of damage to functional elements in an injection mold or its hot-runner components, as well as the reduction of incidences of material degradation, can be done through the addition of a common flow- or temperature-sensing device, says Mike Brostedt, director of market development at Gammaflux LP, Sterling, Va. These issues can occur during startup or restart of a process.
Gammaflux says using such devices creates what it calls process/production interlocks that unite the operations of the mold, hot-runner temperature controller and molding machine to form a new type of closed-loop control designed to prevent common errors that cause production downtime.
"Monitoring multiple points of temperature, pressure and flow throughout the mold can identify problems prior to quality-control rejection," says Brostedt. Gammaflux developed three simple checkpoints that help molders avoid common mistakes. The three interlocks can be implemented using the company's G24 hot-runner temperature controller. The three interlocks stem from three suggested rules: Don't heat the hot runner if the water is not on; do not operate moving hot-runner components, such as the valve gate or pin, if the polymer is cold; and prevent the burning or degradation of material that is caused by machine idling. In all three situations, most injection molders have no basic connection between pieces of equipment that can alert a molder or halt the process, says Brostedt.
Gammaflux introduced a water-flow monitoring option to the G24 controller last year at NPE. It can notify the molder if the proper amount of cooling isn't reaching one or several channels. "If the molder forgets to turn on the water or flow is restricted, the hot-runner components can expand too much during heating and overheat, burning out gaskets or seals inside the tooling system," Brostedt says.
"A customer with two 96-cavity tools that produced a closure resumed production after a period of downtime, forgetting to turn on the water. In approximately 48 hours, the high heat in the tool cracked the manifold," says Brostedt. Gammaflux suggested that the customer incorporate a monitoring thermocouple in the mold plate or other strategic location — and connect it to the G24 through the water-monitoring system. The molding press would be inhibited from operating if it received an alarm through the hot-runner controller. "Water monitoring protects the tool and ensures you are making good parts," says Brostedt.
Operating moving components in the mold when the plastic in the system is cold can create excessive pressure within the tool and damage components. Use of a thermocouple or temperature sensor can ensure that all of the material in the hot-runner system is at the correct temperature before molding begins. Moving parts can be damaged if the system is not in a steady state. The G24 can generate a signal that operations can be started, based on a combination of data from the water-monitoring software and sensor output.
Material degradation can be avoided with incorporation of a simple switch that indicates whether the mold is opening and closing. If the mold temperature does not oscillate, the switch can indicate that the machine has stopped cycling. A molder can tie the temperature sensor to a timer that moves the controller into standby if it receives a signal, says Brostedt.
Gammaflux also added two new functions to the G24 related to heater control that are based on a concept it calls Triangulated Control Technology. The first function, output attenuation, gives the molder the ability to restrict the power to the heater in increments ranging from 1 percent to the maximum power. "A mold maker had trouble validating a massive mold for a thermoset application. The space designed into the tool for the heaters to expand into meant the heaters did not connect to the mass of steel when cold. The heaters burned out during warm up because they did not expand fast enough to connect to the mass they were designed to heat," says Brostedt. With output attenuation, the mold maker can set the power at a level high enough to hold setpoint without reaching 100 percent. This allows the heater to expand without burning itself out. This way, the heater can reach a steady state more quickly.
A new heater short alarm allows users to select an alarm point based on deviation in the amperage output. "Our standard G24 unit is a 15-amp module. The user can have the system alarm if the amperage is as little as 1 amp higher than expected, protecting the heater from shorting," says Brostedt.
FAST HEAT INC.
Fast Heat Inc., Elmhurst, Ill., has reconfigured the way that its Ion and Pulse lines of hot-runner temperature controllers operate. Both hot runner controls—featuring a new touch-screen interface—have undergone significant upgrades to enable wireless connectivity and remote monitoring via virtual network computing (VNC). With these controllers, users gain visibility into the production environment through their smart phone, tablet or desktop environment. The controllers can send alerts via these devices.
The firm also updated Evensoak, a heat control feature on its Ion controller that handles up to 24 heating zones and on its Pulse controller that handles up to 180 zones, to further minimize tooling issues resulting from uneven heating, says Manny Diaz, operations manager.
"Larger-mass heaters are used in areas like the manifold while lower-mass heaters are installed in places like the drops. How you heat is important because uneven heat expansion can occur between higher mass and lower mass areas of the tool, which can crush seals within the tool. Uneven expansion between the two areas of mass can impact the mold cavity, causing grinding," says Diaz.
Fast Heat's Evensoak feature ensures that users can heat the higher mass heaters up to temperature first followed by the lower mass heaters. "This safeguard ensures that all the parts in the hot half of the mold expand evenly," say Diaz.
Molders using the Ion controller can configure their heater zones into three groups, and can then select the sequence of heating. Molders with the Pulse controller can define six heating groups, says Diaz. The updated functionality of Evensoak was shown in a beta state at NPE last year. A fully functional version will be commercially available during the first quarter of the year, says Diaz.
Users with existing Ion or Pulse hot-runner controllers from Fast Heat can retrofit the upgraded functionality of the new software, touch-screen and remote connectivity. Other upgrades to be incorporated include an instruction manual that will be installed inside the software.
Mikell Knights, senior correspondent
Contact:
Fast Heat Inc.,
630-359-6300, www.fastheat.com
Gammaflux LP, 703-471-5050, www.gammaflux.com
Husky Injection Molding Systems Ltd., 905-951-5000, www.husky.co
Vulcan Hot Runner Controllers, 915-730-6640, www.vulcanhrc.com
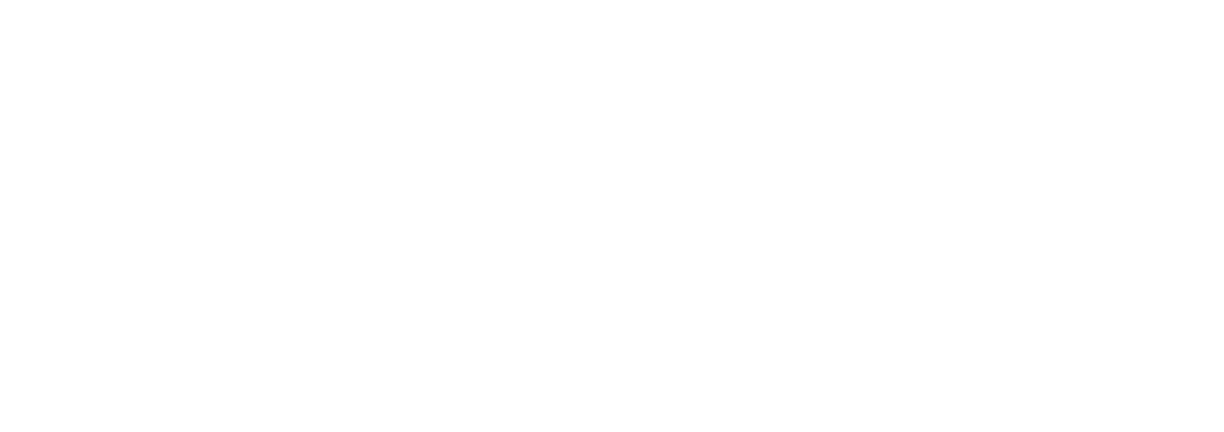