Two-stage shredder-granulator systems and the companies that make them have had some recent updates to their technology. Industry experts are seeing demand increase among processors for in-house use and recyclers.
WEIMA
Weima America Inc., Fort Mill, S.C., officially launched a new granulator series in its size reduction line. In the past, the company has worked with outside sources to supply granulators to go with its shredders, says Marketing Manager Audrey Brewer.
"Now customers can find granulators and shredders under one roof, which we think will be more efficient for the customer," she says.
The latest series of granulators is marketed as the LM/SM Series, which is a heavy-duty option. This is in addition to its NZ Series that has the ability to granulate pre-shredded material to sizes of 4mm to 10mm. The LM/SM Series is offered in eight sizes. The LM Series is designed for processing 1,000 to 3,500 pounds per hour; the SM Series can take on 3,000 pounds per hour and increases from there. The company says that the throughput rate depends on the material and screen size.
"We've sold granulators on and off for years," says Madison Burt, VP of sales, Weima America. More and more customers want complete systems. These systems can be used in different configurations, including stacked or horizontal systems.
The NZ Series traditionally had been used in a two-stage setup. "Too often, I see customers spend more money than they need to spend on granulators that are much larger than their application requires," he says. "Why? Because their scrap is too large to fit in a smaller granulator. This could be rectified by the purchase of a small pre-shredder and a smaller granulator, saving the customer money and a lot of headaches in the long run."
All the shredders and granulators are built in Germany. At its U.S. location, Weima can customize the systems. Weima's more recent modifications have included control integration with Ethernet capabilities and soft starts.
The company says the series is built to process a variety of plastics, including pipes and profiles; hollow containers; drums; bottles; car bumpers; skeletal waste from thermoforming; lumps/purgings; injection molded parts; and flexible plastics such as film.
Although the need for granulation is mostly seen in the realm of hard plastics, officials at Weima are getting new leads every day for other types of plastics, as well.
The key with these two-stage systems is design, officials agree, especially when it comes to maximizing floor space. Most of these machines have been built to fit into smaller spaces. The LM/SM Series has a compact design. It also has a tilting design that allows for quicker access to the cutting chamber and screen, and this design also allows for easier cleaning and routine maintenance.
AVIAN
Avian USA Machinery LLC, West Chicago, Ill., has seen demand increase from automotive companies such as Toyota, Buick, Nissan and Kia for its stacked systems and has had to improve its design due to those demands. In particular, customers are asking for extra features in these products such as higher output, lower energy consumption, noise reduction, longer usage life and easier maintenance.
Avian's system now features a smaller motor to drive the system and improvements in the knives and cutting chamber design, says Andy Gu, Avian's VP of operations. The system now has a lower power motor and drive with gear motor to increase the efficiency and a smaller housing for the cutting chamber.
"We changed the special design for the stacked system," he says, "because normally for the automobile industry, customers want very low decibel and compact machines for their facilities. That is why we have to change and improve our design to provide low utility costs and smaller, compact machines to match their facility."
The stacked system specializes in the reduction of large, bulky parts. In addition to bumpers, the unit is being used for lumps and large vacuum containers. Gu also says that customers are demanding equipment that is easier to maintain. In addition to demand from automotive companies, Avian is seeing demand from recycling companies.
ROTOGRAN
Rotogran International Inc., Concord, Ontario, has added upgrades to its granulators that are used in conjunction with shredders from Vecoplan LLC, Archdale, N.C.
The stacked systems make sense, especially from a processing and efficiency standpoint, says Rotogran President Michael Cyr.
"By putting a shredder on top of a granulator, you can reach and maintain the maximum throughput capacity of an existing granulator," he says. "If the shredder itself does part of the work, part of it is already done before it hits the granulator. It decreases the load on the granulator."
"It also will extend the life of the blades and lessen the frequency of blade sharpening," Cyr says.
The second positive is that a shredder can be loaded by bulk or batch, and therefore, a worker responsible for loading the machine can load it and walk away. Granulators are not built to be shock loaded, says Cyr. The material has to be metered in. The shredder is getting the material down to a reasonable size for the granulator.
An example of a stacked two-stage system for Rotogran and Vecoplan is the Vecoplan VAZ 1100 U single-shaft rotary shredder with a Rotogran model 1442 granulator. The infeed of the granulator is bolted directly to the outfeed opening of the shredder. The granulator has industrial roller wheels so that it rides on a steel track that allows it to be unbolted and rolled out for quick and easy cleanouts, material changes and routine maintenance.
However, there also is no need to roll out the granulator from under the shredder to service the blades, says Cyr. Rotogran uses a low-profile design that fits the granulator under the shredder and allows the user to access, among other things, the screens or the blades.
Rotogran recently has equipped its granulators with innovative components, says Cyr. One of those components is for particularly abrasive materials such as plastics that are dirty or highly filled with glass. Rotogran has put in removable inserts that can be coated with tungsten carbide or made from exotic materials.
"When you replace the inserts, the chamber becomes new once again," he says. "We machined pockets into the granulator and put in removable, replaceable inserts. In half the time of changing knives, you can change the inserts. It is that simple to do."
Rotogran also now has the ability to add a pathway deflector into the cutting chamber itself. The removable deflector is offered as an optional upgrade to increase throughput.
"This deflects the material back directly into the cutting circle, which greatly improves the throughput," he says. "It is removable and replaceable."
The pathway deflector option can only be used in conjunction with a shredder. Rotogran has offered this on its granulators for rubber but recently began offering it on the stacked system granulators that are married with the Vecoplan shredders.
Industry officials say that metal is the nemesis of stacked systems; in materials where there would be a large amount of metal contamination, an in-line or horizontal setup should be used.
Angie DeRosa, managing editor
Contact:
Avian USA Machinery LLC, 630-687-9876, www.aviangranulator.us
Rotogran International Inc., 905-738-0101, www.rotogran.com
Weima America Inc., 803-802-7170, www.weima.com
Vecoplan LLC, 336-252-4462, www.vecoplanllc.com
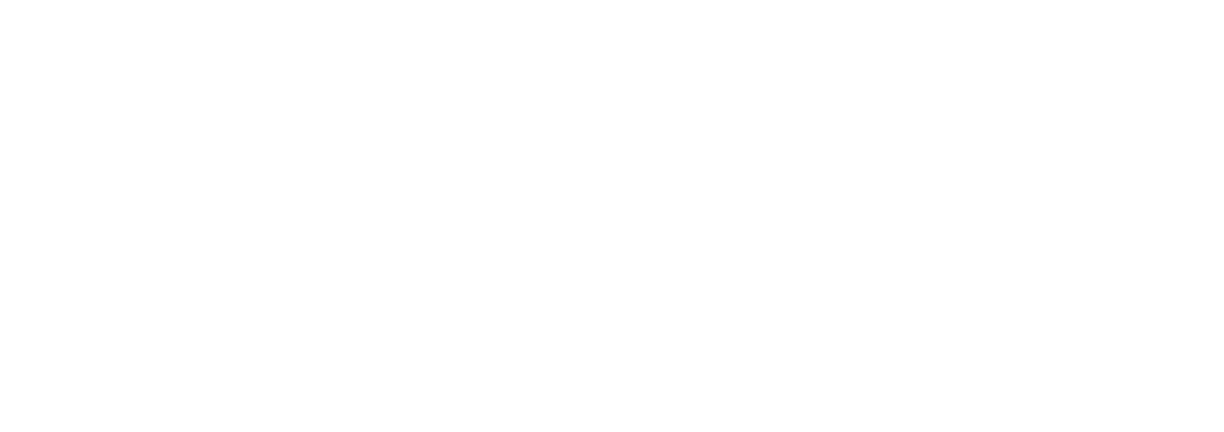