Kautex Maschinenbau GmbH is running like it is turbocharged, or to be more precise, because of turbochargers.
The German manufacturer of extrusion blow molding machines is benefitting from a shift by automakers worldwide to smaller engines. Those smaller engines need devices like turbochargers to boost horsepower, and turbochargers need plenty of pipes to bring in and push out air.
These air ducts — traditionally made of aluminum, rubber or a combination of the two connected by clamps and requiring seals — have to twist through crowded engine compartments to bring air from the intake to the filter, then to the turbocharger, then to the intercooler and finally to the combustion chamber. There can even be two or three turbochargers on an engine, multiplying the air-management requirements.
Kautex's suction blow molding process allows ducts with intricate shapes, evenly distributed wall thickness and no weld seams to be manufactured as a single plastic piece.
"By changing from this traditional combination of parts to a single, blow molded part, the auto manufacturer can reduce the total number of parts significantly," says Olaf Weiland, CEO and part owner of Kautex, during an interview at Kautex headquarters in Bonn, Germany. "It simplifies logistics and the chance for quality issues."
Kautex, which in the U.S. is represented by Kautex Machines Inc., North Branch, N.J., claims a world-leading role for machinery used to produce hollow plastic parts for the automotive industry. It has long held a dominant position in machinery for manufacturing plastic fuel tanks.
Kautex's suction blow molding process for air ducts is hot now, but it also has deep roots and strong market share in numerous other blow molding products. The company divides its business into four market segments — consumer packaging, industrial packaging, automotive and specialty applications.
"Kautex has machines covering all the 3-D blow molding methods known to the industry," Weiland says. "Everything is available and we can look at every case and make tailored recommendations to the customer, depending on the variety of parts he expects to manufacture."
Consumer packaging made with Kautex machines runs from small cosmetic containers or shampoo bottles to bottles with handles up to 4 liters. It developed the first machine for the extrusion of blow molded bottles in 1949 and its first coextrusion machine in the early 1980s. Today it offers coextrusion machines for bottles with up to seven layers. More than 20 machine models in four lines are tailored for consumer packaging.
Industrial packaging includes stackable containers up to 260 gallons, drums up to 55 gallons, fuel oil tanks, intermediate bulk containers and smaller canisters. Kautex machines use continuous extrusion, coextrusion and discontinuous extrusion for these products.
Kautex developed the machine for the first serial production of blow molded plastic automotive fuel tanks in 1973 and leads the market for fuel tank machinery. In addition to 3-D curved pipes, other major auto parts Kautex machines can produce include rear end spoilers, bumper enclosures and underbody coverings.
Specialty products include composite high- pressure vessels, toys, enclosures and carrying cases.
There is a heavy focus on engineering at Kautex. "One financial guy looked at our company and said we were an engineering company with a little bit of manufacturing," says Weiland.
At the top of the current list of engineering problems to solve is speeding up article changeover times.
"We have decided to make color change a solid, reliable feature at Kautex so that every customer looking to improve his change time will find us prepared to help," he says.
"No one solution fits all. For the past four to five years, we have been continuously working on reducing color change time, mostly with our customers, taking into account their individual requirements and conditions," Weiland says. "One of the blow molding machines in our technical center has been mainly used for color change trials.
"Useful measures include optimization of screw and melt flow channel design, surface treatment to reduce deposition, change of type of masterbatch, replacement of masterbatch by liquid color, enhancement of purge effectiveness and re-sequencing the color in the production plan in order to minimize the occurrence of need for heavy-duty purging," Weiland says.
This is necessary, as packaging manufacturers need quick-change capability. A bottle manufacturer might have one bottle in several colors, and there might be different layers with different color requirements to achieve a desired optical effect on the shelf, Weiland says.
Like color change, quick mold change plays an important role for packaging manufacturers. "Each mold can be changed in 15 minutes on our all-electric KBB machines," says Christian Kirchbaumer, team leader for communications and marketing. "This [is] compared with up to one hour on competitors' comparable machines, which makes our newest line very economical."
Packaging will once more be a focus for Kautex at the K Show later this year. The company will extend its range of KBB machines specifically designed for stackable, blow molded containers with hollow handles used for everything from milk to oil.
"There will be no hydraulics, so it will be a very clean machine, which is especially interesting for the food sector," says Kirchbaumer.
The new models will have a higher clamping force, among other improvements.
"With the KBB series, customers can achieve up to 40 percent energy savings, depending on cycle time and clamping force," Kirchbaumer says. "This is significant. It can, for example, be achieved by braking energy from the clamping unit being brought back into the machine or the plant's network."
Kautex has seen strong growth in China, its biggest market. "The growth is slowing down, but the market is still growing," Weiland says.
"The U.S. has traditionally been one of our most important markets and for the past five years the auto business, as well as packaging, has been strong," he says. "Specialty products are also strong in the U.S. That is machines for large blow molded parts in home and garden and leisure products." The U.S. is Kautex's second-biggest market. Kautex first shipped a machine to the U.S. in 1955.
The company has about 550 employees, including 410 at the Bonn headquarters and manufacturing plant; 110 at a plant in Shunde, China; 20 at a sales and service office in the U.S.; and all others elsewhere in the world.
Kautex sales were about $116 million in 2014, and the company expects to see a 4-5 percent increase for the past year, Weiland says.
The company employs a manufacturing system that is unique in the way it interfaces with customers. A dedicated assembly team works with the customer from initial discussion until the machine is built and tested in Bonn, then the same team delivers it to the customer's plant and completes setup and training.
The team remains the customer's point of contact for warranty work.
"The excellence of our blue-collar people is shown in the highly customized, one-piece final assembly of a complex system," Weiland says. "The team keeps responsibility for its own machine through the process."
Kautex celebrated 80 years in business last summer, and during a visit from Plastics Machinery Magazine, the production floor was packed with machines being assembled and tested. There is a healthy backlog of orders.
More than 6,100 active Kautex machines are currently installed around the world, including the first six-layer coextrusion machine for fuel tanks sold in 1992 to Walbro Automotive, which installed it in its Ossian, Ind., plant.
It was a first for the U.S. market, where plastic fuel tanks up to that time had been blow molded with a single layer of PE, then fluorinated on the inside to prevent vapors escaping through the walls. Using a barrier layer helped automakers meet more stringent emissions requirements.
That first KB250 machine produced 500,000 tanks a year for Ford, so the coextrusion fuel tank business took off for Walbro and Kautex. Walbro Automotive was acquired by TI Automotive Group in 1999 and that same machine was relocated to Great Britain, then in 2001 it was moved to the TI Automotive plant in Belgium, where it remains in operation.
Kautex claims an 85 percent worldwide market share for machines used to blow mold automotive fuel tanks.
Kautex is on the ground floor for another automotive evolution — high-pressure vessels for alternative automotive fuels such as compressed natural gas (CNG) and hydrogen.
Last year, the company installed a full production line in its technical center, and it has developed a pressure vessel for a hydrogen-powered car and is testing different raw materials. It is also developing blow molded natural gas containers for cars and trucks from composites that are 75 percent lighter than traditional steel tanks. One study predicts that CNG fuel tanks will be a $524 million market by 2019.
Ron Shinn, editor
Contact:
Kautex Machines Inc., 908-252-9350, www.kautex-group.com
Ron Shinn | Editor
Editor Ron Shinn is a co-founder of Plastics Machinery & Manufacturing and has been covering the plastics industry for more than 35 years. He leads the editorial team, directs coverage and sets the editorial calendar. He also writes features, including the Talking Points column and On the Factory Floor, and covers recycling and sustainability for PMM and Plastics Recycling.
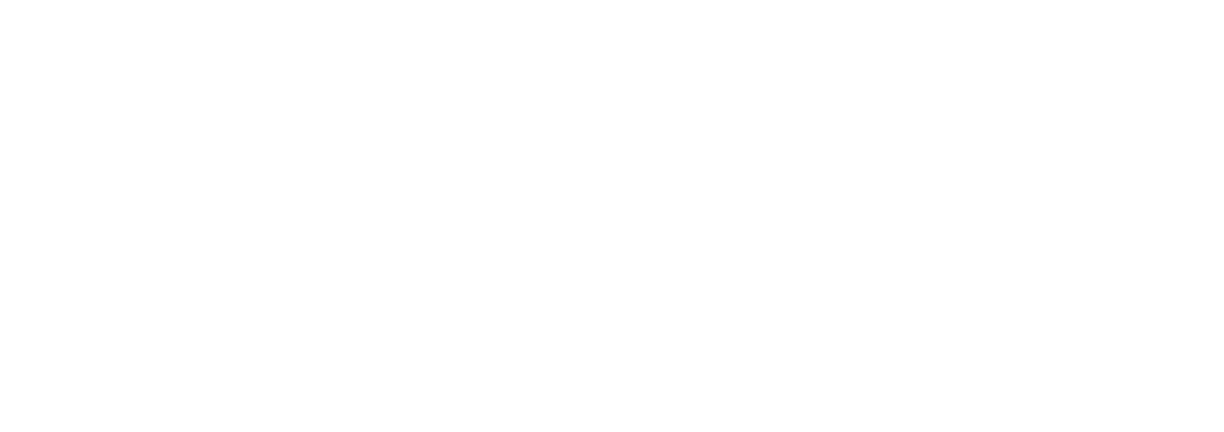