No matter the decorating or marking method, technologies are evolving rapidly, with greater sophistication, particularly for the plastics industry. Makers of these technologies reported that they are staying very busy as they come up with new designs and new ways to integrate existing technologies into manufacturing cells. Therefore, what was once viewed as a value-added, separate secondary operation now in some cases is becoming an essential part of molding and extrusion production.
As in other machinery and equipment sectors, energy efficiency, labor reduction and environmental considerations are top priorities. Finding ways to automate is another key trend.
Pad printing, for example, now can be viewed as an automated, industrial decoration method, says John Kaverman, owner of Pad Print Pros LLC, Onsted, Mich., an independent sales and consulting firm that specializes in pad printing and digital thermal transfer marking as well as several other processes.
"We're based in industrial applications where we are trying to integrate and automate as much as possible," Kaverman says. For example, pad printing can be combined in an injection molding cell with a multiaxis SCARA robot where parts are oriented by the robot and printed, using vision systems to perform quality control.
"We've gotten to the point now where we're taking so many material handling steps out of the process to cut down the cost of a part," he says. "We can integrate pre-treatment, post-treatment and vision inspection. We'll build an entire system and bolt it up to somebody's existing line and off we go."
Stepper motors in pad printing are taking over where pneumatics once were used. Kaverman works with Innovative Marking Systems, Lowell, Mass., which is the exclusive U.S. distributor of pad printing machines and related equipment made by Tosh srl, Milan, Italy. Its lines are marketed as Logica and Cartesio. The Logica 08, for example, is fully electric for applications using up to 10 colors. The Cartesio system would be used to handle really large, complex geometries like those used to produce sports equipment and toys.
Demand for pad printing is increasing in the medical industry, reports Scott Einsig, director of business development with Engineered Printing Solutions, East Dorset, Vt. To that end, EPS will introduce its KP08 fully servo printer for catheters at the Medical Design & Manufacturing (MD&M) West show Feb. 9-11 in Anaheim, Calif.
The KP08 can be configured in a number of ways (up to five colors for standard machines) to accept many substrates, Einsig says. It prints 1,000-1,200 cycles per hour with an available cup slide for images up to 800mm wide. The system can be fitted with a standard XYR fixture, linear shuttle and elliptical or linear conveyor. Users are able to print on two or more parts at a time or configure the printer to perform a 360-degree wrap on catheters. The machine that will be displayed at MD&M will be fully servo, meaning the cup slide and pad shuttle are fully programmable.
"Medical device printing is a huge market for pad printing, as this is one of the only options for product decoration," Einsig says. "The versatility of the servo KP08 saves time and money and gives production managers a process that can be set and qualified with very little adjustment from job to job."
At Cassco Machines - Cassco Automation, Toronto, owner and President Ken Thuro reports that the company is making a lot more servo-powered machines for hot stamping and heat staking/insertion due to their capacity for energy savings, precision, multiple program storage and reliability.
"We have just done a couple of large, under-the-hood automotive components," he says. "With that particular app, having the servo was invaluable. It is a very difficult plastic to decorate and being able to set all of the parameters on the control means that the fine-tuning is very precise, and it also takes the operators out of the equation."
It is very common to have the machines integrated into the cell with the molding machine, especially for larger parts, he says.
"A lot of our systems are fully automated," he says. "They also can be, for larger parts, loaded directly from the molding machine to the hot-stamping machine."
Controls have become much more sophisticated, he reports, and there have been upgrades through the software.
"You can store multiple recipes. If a machine is being used in a press-side application, you can select a recipe for running hot parts as they come out of the machine or you can select a recipe for decorating cold parts from inventory."
Demand definitely is increasing and people are becoming more confident with the more sophisticated machinery. Cassco now has software to calculate the energy savings for the electricity used to generate the compressed air versus the electricity used on a servo, especially now that companies are starting to do energy audits of factories.
"If we know the size of the machine, cycles per hour, for example, we can take the standard costs for compressed air and the electrical cost of the machine and we can do a complete printout of what the energy savings will be," he says.
Angie DeRosa, managing editor
Contact:
Cassco Machines - Cassco Automation, 416-445-6262, www.casscomachines.com
Engineered Printing Solutions, 802-362-0844, www.epsvt.com
Innovative Marking Systems, 978-459-6533, www.padprinters.com
Pad Print Pros LLC, 517-467-5340, www.padprintpros.com
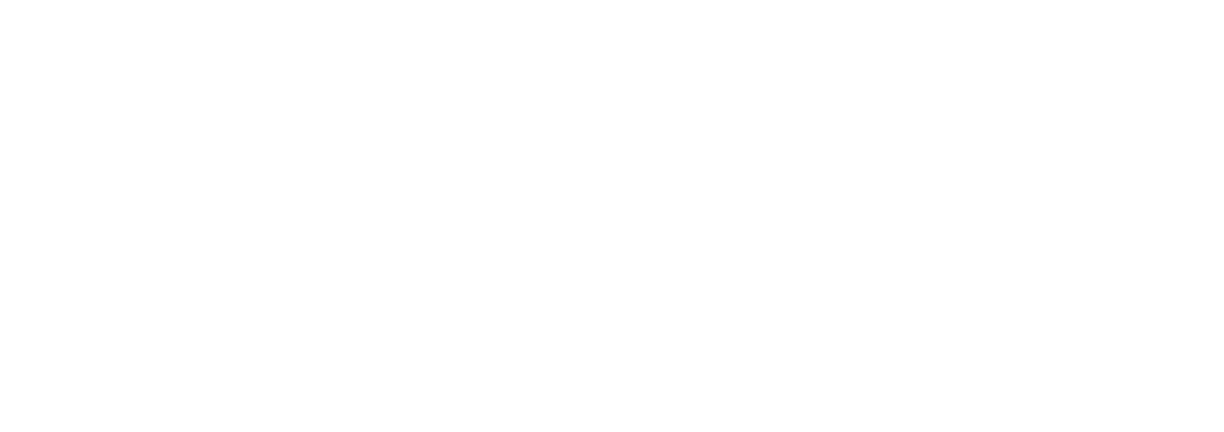