Ultrasonic welding equipment is being expected to deal with increasingly complex tasks. The need is not so much for a welder as for a system, and so, demand is growing for more sophisticated equipment that can operate with a degree of automation. Ultrasonic welding equipment suppliers are responding with a wide range of capabilities.
Branson Ultrasonics, a business of Emerson, in Danbury, Conn., has added the DCX F power supply to its DCX line of ultrasonic welding products. The DCX F, which can communicate with the welder via commercially available HTML interface protocols, provides advanced weld process control and real-time Ethernet/IP distributed control.
Bob Halbert, Branson product manager, says the DCX F allows users to set parameters from a programmable logic controller (PLC) or human-machine interface. "This will greatly help users reduce complexity, save cost and centralize the welder control," he says.
The DCX F power supply achieves consistent weld quality through continuous system monitoring and closed-loop control of the welding process, Halbert says. Users can choose from multiple weld modes, such as weld time, weld energy and peak power. It provides increased process and automation control using programmable reject limits and configurable input/output (I/O) options. Branson says a web page interface makes setup easy.
Branson offers a variety of mounting options, including horizontal, vertical and 19-inch rack-mount configurations. The flexibility of configurations means it's easy to integrate the system into work cells with automated systems, Branson says.
Herrmann Ultrasonics Inc., Bartlett, Ill., uses the term "functional integration" to describe production systems in which multiple functions and verification processes are combined into single, compact work cells. Its ultrasonic welding systems can be integrated easily with automation that incorporates and connects multiple auxiliary functions, for greater efficiency and reduced space requirements. Herrmann says this reduces unit costs and enhances production safety.
"Functional integration simplifies production monitoring and quality-assurance processes," says Uwe Peregi, Herrmann Ultrasonics executive VP and GM. "As the customer demand for it is growing, Herrmann Ultrasonics is going the extra mile and implementing further development of existing products to prepare them for Industry 4.0."
Herrmann cites the example of a multipart engine cover that is assembled and welded to the sound insulation mat. The work cell includes auxiliary functions. In a single work cell, rubber dampers are mechanically pressed in and scanned for correct fit, a bar code label is printed and the component is engraved. The company says it works with customers so they can integrate other auxiliary functions, such as marking or embossing, into the process.
Machine integration is also important to Sonics & Materials Inc., Newtown, Conn. It provides consultation, design and custom machining of horns and fixtures not only for its own ultrasonic welders, but also for competitors' equipment. It says welding users are becoming more sophisticated in their equipment choices, as they realize the importance tooling plays in the process. The company is carving out a niche for itself by emphasizing that an ultrasonic welder and horn need not come from the same supplier, especially as assembly jobs and specifications change.
Offering systems in frequencies of 40, 35, 30, 20 and 15 kilohertz, Sonics designs horns using a finite element analysis (FEA) simulation program that predicts the vibratory action of the horn prior to its actual manufacture.
Through color and line patterns, as well as numeric values, FEA simulations can illustrate a horn's amplitude and stresses during a weld. With this information, Sonics can design the horn that's best suited to a client's application. The same FEA technology can diagnose ineffective ultrasonic welds or cracked horns.
In addition, in an effort to help manufacturers better integrate welding into their processes, Sonics now offers Ethernet/IP connectivity on its benchtop welding presses. Brian Gourley, North American sales manager for the welding product line, says the feature makes performance monitoring easier. With it, "systems integrators [can] communicate directly with our I/O through a single Ethernet cable, greatly simplifying and streamlining installation of our welding equipment into automated systems and special machinery lines," Gourley says. "Subsequently, users can monitor welding data and direct operations through this connection, providing maximum versatility and responsiveness while eliminating complex wiring and operational commands."
Rinco Ultrasonics USA Inc., Danbury, Conn., has made several additions to its product line over about the last year. It developed the Hybrid PPS0145 film-sealing technology for creating the cosmetic portion of the seals on flexible pouch packaging. A benefit of the Hybrid PPS0145 seal geometry is that it eliminates the requirements for follow-up heat sealing and cooling stations.
Rinco also offers a clean-room version of its Dynamic 3000 series benchtop welder for medical applications. The Dynamic 3000CR series benchtop welder, which is certified for ISO 6/Class 1,000 clean-room environments, ensures that medical parts are manufactured and assembled in a repeatable manner. The launch comes amid strong demand for clean-room welders, according to Gordon Hull, managing director of Rinco.
The Dynamic press offers amplitude and force profiling with extensive graphing capabilities and detailed process set-up analysis through the use of peripheral software.
Rinco also now supplies the Ecoline ultrasonic generator. It is significantly smaller than many others, weighing in at only 7 pounds. The Ecoline generator comes with a line of hand-held units, including the hand wand, hand tacker and hand cutter.
The front panel of the generator has an ultrasonic test button to ensure the system is operating properly. It also allows the operator to change amplitude from 40 percent to 100 percent in 10 percent increments.
Merle R. Snyder, senior correspondent
Contact:
Branson Ultrasonics, 203-796-0400, www.emersonindustrial.com
Herrmann Ultrasonics, 630-626-1626, www.herrmannultrasonics.com
Rinco Ultrasonics USA Inc., 203-744-4500, www.rinco-usa.com
Sonics & Materials Inc., 203-270-4600, www.sonicsandmaterials.com
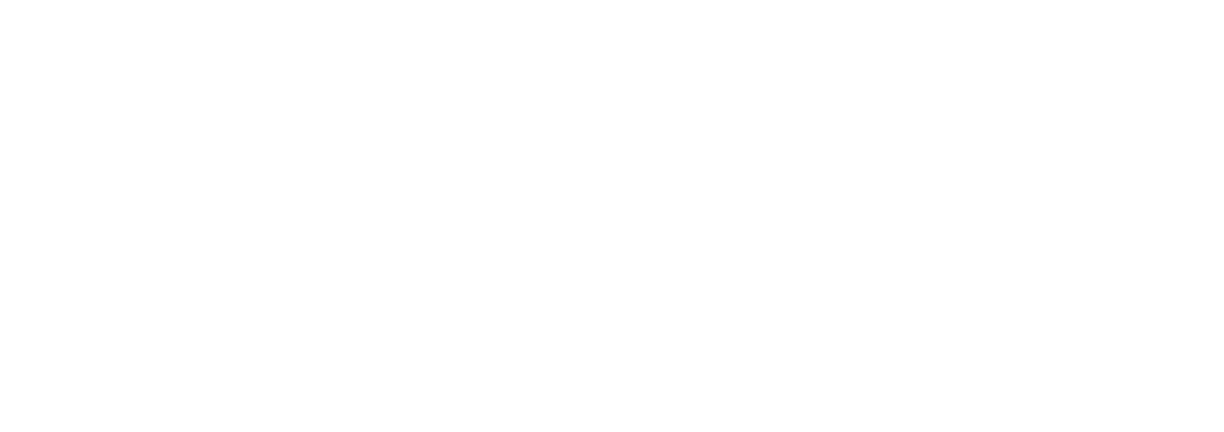