The technology behind collaborative robots, a new class of industrial automation designed to safely interact with humans without the presence of guarding, continues to expand.
Rethink Robotics, Boston, which says it is the first company to develop and commercialize robot automation that operates in a collaborative, interactive environment with people, has launched Sawyer. The single-arm collaborative unit is slimmer, more precise and handles heavier payloads than Baxter, its two-arm collaborative sibling introduced in 2012.
The two robots distinguish themselves from more traditional three- and six-axis industrial robots through their software, use of sensors and cameras, user interface and controls, which provide a high level of flexibility, adaptability and precision. The units also have a digital "face" — a screen with expressive, electronic eyes that adds a human element to the automation. These innovations allow machine operators and line workers with no expertise in engineering, software or robotics to train the robot for a new task in minutes, says Carl Palme, the company's product manager. In comparison, traditional automation requires highly skilled technicians to install and program.
HANDLING HARD-TO-AUTOMATE TASKS
Sawyer has a slight frame, standing approximately 53 inches high and weighing 42 pounds. The seven-axis single-arm robot has a reach of about 50 inches and handles payloads up to 8.8 pounds. Movements and positioning are repeatable and accurate to within 0.1mm. Baxter weighs 165 pounds, handles payloads up to 5 pounds per arm and has a reach of about 4 feet per arm. Its movement is accurate to within 0.25mm, says Palme.
The robots from Rethink Robotics are different in terms of design and application than six-axis collaborative robots developed by other automation suppliers (see Plastics Machinery Magazine story here).
"These collaborative robots handle the 90 percent of manufacturing tasks that have been impractical to automate with traditional industrial automation. They integrate seamlessly into an existing work cell and dynamically adapt to real-world conditions on the plant floor," says Palme.
The Rethink collaborative robots are ideal for lower-volume, higher-mix applications that call for frequent line changeovers. Traditional industrial automation is best suited to higher-volume, higher-speed, lower-mix applications where line changeover is infrequent and work spaces do not have people in the immediate surrounding area, says Palme. Generally speaking, collaborative robots have a lighter payload than their more traditional counterparts, yet they are an ideal fit for plastics applications producing lightweight parts, says Palme.
The seven-axis robots' targeted applications include machine tending, circuit board testing, loading and unloading, packing, materials handling and other repetitive tasks that require precise handling. "Users can tend to a CNC machine, reach into an injection press or handle a wide range of tasks with these robots," says Palme.
The design and updated drive system of Sawyer make it suitable to a range of applications that previously were difficult to automate, even with Baxter. Sawyer is a different type of robot rather than a different version of Baxter, says Palme.
HOW IT WORKS
Sawyer's ability to approach a part from various angles through tight windows of space is attributed to its seven axes of freedom. Its possible movements include up and down; forward and back; and right and left; the motions also include wrist yaw, wrist pitch, wrist roll and elbow rotation.
Its dexterity lets the robot deftly maneuver within a work cell and around different types of machines, says Palme.
Sawyer and Baxter operate on the Intera software platform and graphical user interface, designed to make programming intuitive and operation interactive. The newest iteration of the software, Version 3.3, allows Sawyer and Baxter to operate at an even higher level.
Sawyer also features embedded vision via a high-performance camera from Cognex Corp., Natick, Mass., that supports the collaborative nature of the robot. The camera facilitates a system using landmarks to ensure that Sawyer moves safely.
The vision system, located on the forearm for Sawyer (a slightly lower-resolution camera in Baxter is placed just above the gripper) is linked to a software technology and program dubbed the Robot Positioning System. QR-type codes designed for the robot are strategically placed throughout the workspace.
The location of each QR code becomes a landmark for the robot, forming a boundary that the robot will operate within. An operator moves the robot to the QR code landmark, takes an image, then assigns that landmark a number in order to map the location of markers to the robot.
Next, the operator uses the camera and a train-by-demonstration programming function to teach the robot where to find the part or parts it will handle in relation to the landmarks, says Palme. The operator also teaches Sawyer part recognition and its overall movement profile here. The programming allows the user to rely on context instead of coordinates to create the steps that form a task. The robot can then repeat the actions/movements in the task.
If an element, such as a conveyor, in a production cell experiences a shift through an inadvertent bump or movement, users of a Sawyer or Baxter robot can easily adjust by re-registering the element's position. The user takes the robot's arm, accesses the software, takes a picture of the new location of the landmark and applies it to the task.
"The robot understands where the landmark is, and more importantly, knows where the parts are in relation to the landmarks. Robot retraining takes minutes," says Palme. In comparison, traditional automation operates in a known, fixed environment. If workplace elements were shifted, the line would likely be shut down for hours while workers retrain the industrial robot to the new position.
Likewise, the user moves the robot arm and takes images that are saved to the software to instruct Sawyer where to find the part, where to grasp it and where to move it. The software learns and remembers the dimensions and weight of the object when it initially contacts the part. "It understands the force required to grip the part and applies only as much force as is required to handle the object," says Palme. Users create part pick-up locations, then can customize a pick location profile for the robot. (For example, the robot can pick from Location 1, then Location 5, then Location 3; or select from an array of parts.) Once completed, the operation can be stored to memory, recalled, modified and deleted, and can be transferred between robots.
An innovative function incorporated into both Sawyer and Baxter is a force-sensing technology that uses sensors embedded at each joint on the arm. They allow the robot to "feel" its way into fixtures, parts or machines when the part or the position of the part varies. "Compliant motion control is a function that industrial automation does not have which can be used to grab a part when its orientation or positioning is off," says Palme. Compliant motion control is supported by the robot's high- resolution torque sensing, and it allows Sawyer and Baxter to achieve what Rethink Robotics calls adjustable precision. The force-sensing technology also halts the actions of the robot if it comes into contact with an object or person unexpectedly.
OTHER FEATURES
Rethink Robotics offers vacuum cup grippers and electric parallel grippers in a range of configurations for use with Sawyer and Baxter. The Sawyer robot has also incorporated an International Organization for Standardization (ISO) standard tool plate that will allow third-party grippers and other end-of-arm-tooling solutions to be used, says Palme.
An optional mobile pedestal with locking casters, available for both robots, allows users to roll the robot from one line to another.
Baxter is also offered in a version for research applications. In this nonmanufacturing configuration, the robot has an open-architecture operating system and a different camera setup.
Sawyer and Baxter cost less than $30,000 and come with hardware, software, user interface, sensors and safety programming. Sumitomo Heavy Industries Ltd., Tokyo, announced in November that it will market, service and sell Rethink's Sawyer robot to companies in Japan.
Massachusetts Institute of Technology roboticist Rodney Brooks founded Rethink Robotics in 2008. He's a founder of iRobot, Bedford, Mass., which makes the Roomba vacuuming robot, and the inventor of PackBot, a robot designed to dispose of roadside bombs.
Mikell Knights, senior correspondent
Contact:
Cognex Corp., 855-426-4639, www.cognex.com
Rethink Robotics, 617-500-2487, www.rethinkrobotics.com
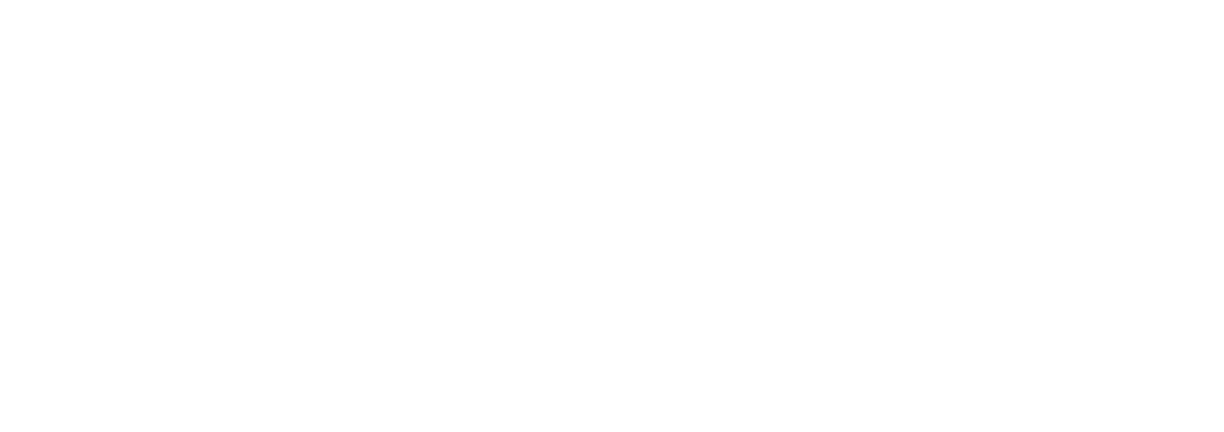