Sumitomo (SHI) Demag Plastics Machinery GmbH, Schwaig, Germany, demonstrated a complex production unit for insert molding and decorating at Fakuma.
For the demonstration, a Systec Servo 210 injection molding machine molded a nutcracker. A Yaskawa six-axis robot with gripper system and hot-handling device automated the process.
The decoration was 0.5mm foil. A 3mm-thick reinforcing rib structure was also injection molded along with a corrugated strip for the tooth structure. The entire product weighs 3.2 ounces.
The decorative foil was made by Leonhard Kurz Stiftung & Co. KG, Fürth, Germany.
Sumitomo says the project demonstrates integration of lightweight engineering and decoration requirements, such as those needed for optical parts in automotive applications.
To make the part, the removal and insert gripper at the robot's head picked up the foil, inserts, corrugated strip and reinforcing tape, then moved into the open mold. There, it removed the finished part, then placed the foil, tape and metal insert into the empty cavity. The mold closed and the insert molding cycle began.
Other elements of the production station include a removal station for the metal inserts and decorative foil, heater and removal station for the reinforcing tapes, cutting station for sprue removal and a riveting station for connecting the nutcracker halves. The reinforcing tape was heated before molding to speed up cycle time.
The reinforcing tape contains continuous glass fibers in unidirectional orientation, which provides a significant tensile strength parallel to the fiber direction. Processors can reinforce their products by placing tapes where wear and loads are heaviest.
Sumitomo integrated the robot and other downstream equipment with the molding machine's NC5 plus control system.
The Systec Servo molding machine is equipped with an energy-saving "activeDrive" module that combines a frequency-controlled, high-performance motor with a hydraulic pump. This matches the required hydraulic pressure to the corresponding cycle sequence, allows parallel movements with only one hydraulic pump and reduces noise. Energy use is reduced by up to 50 percent compared with standard hydraulic systems, according to the company.
Sumitomo (SHI) Demag also showed the IntElect 100 to demonstrate several new features that were added to the IntElect line in mid-2015. The line is especially suited for molding electrical and electronics components, optics and automotive parts. Some of the standard enhancements include:
• A new reference run option for clamping units and enhanced purging functions.
• Injection units with screws in five different diameters.
• An adjustable tolerance band that allows better process control and protects the mold from overfilling.
• A display of the machine's energy consumption. The display also provides a selection of user-defined and pre-defined molding data screens to facilitate data processing.
Several new options are now available, including an ejector profile across the entire forward and backward stroke, integrated hydraulic unit with servo drive, Sumitomo's "activeFlowBalance" to balance multicavity molds and the "activeLock" adjustable nonreturn valve.
Ron Shinn, editor
Contact:
Sumitomo (SHI) Demag, 440-876-8960, www.sumitomo-shi-demag.eu
Ron Shinn | Editor
Editor Ron Shinn is a co-founder of Plastics Machinery & Manufacturing and has been covering the plastics industry for more than 35 years. He leads the editorial team, directs coverage and sets the editorial calendar. He also writes features, including the Talking Points column and On the Factory Floor, and covers recycling and sustainability for PMM and Plastics Recycling.
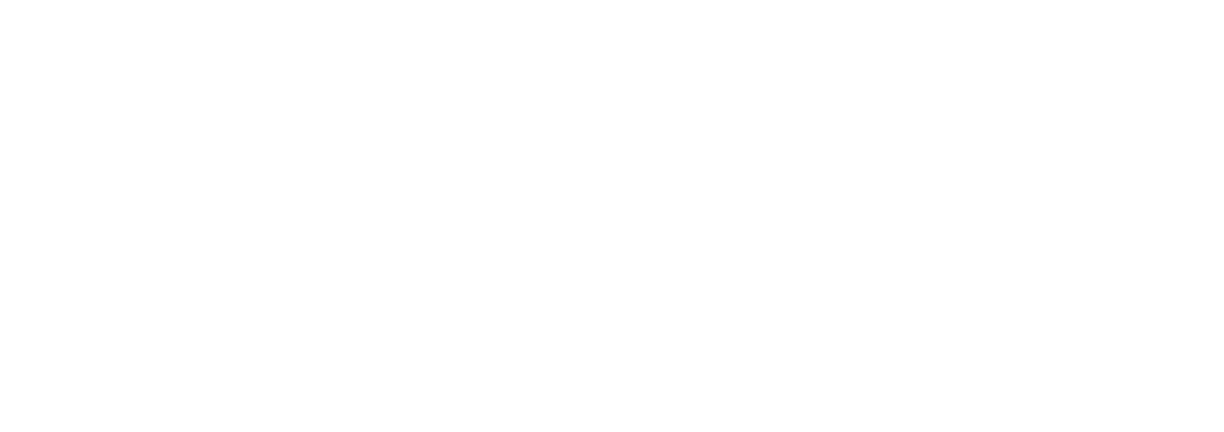