Mold breathing — when inflowing melt pushes the halves of a mold apart — can cause flash or burn marks and result in parts being rejected. Engel thinks the best way to control mold breathing is with software it debuted at Fakuma called iQ clamp control.
This software joins Engel's iQ family, which includes iQ weight-control software that optimizes the injection process.
The melt can push mold halves apart by a fraction of a millimeter. If the clamping force is too high, the mold undergoes unnecessary stress and excess energy is consumed. Using a gauge to manually measure mold breathing can be imprecise. This frequently results in injection molders using the maximum clamping force available instead of figuring out the best amount of force for the job.
Engel Austria GmbH, Schwertberg, Austria, says iQ clamp control automatically determines and adopts the optimal clamping force. This, according to Engel, means its CC300 control unit is the first unit that is capable of autonomously determining the correct force.
The software monitors cavity pressure in the mold and, since it uses the existing sensor system on the molding machine, it does not need extra sensors or hardware.
The trick Engel engineers figured out is that the entire clamping system, including the mold, can be considered a spring. The stiffness of the spring is determined during clamping force buildup.
During injection, the tension of the spring increases slightly when the mold breathes, so the clamping force automatically increases just enough to compensate. By continuously adapting the clamping force, the software minimizes the mold breathing despite fluctuating process conditions.
To determine precisely how much force is needed, dry cycles are performed at the start of production and the changes in clamping force are stored as reference curves.
Engel says this results in significantly reduced risk of quality problems, ensures optimal mold ventilation, protects the mold against overfilling and improves energy efficiency.
Initially, Engel is offering iQ clamp control on its electric machines with up to 225 tons of clamping force.
IQ stands for "intelligent quality," which Engel defines as expert knowledge that is integrated into the injection molding machine's control unit. The iQ family of software is an important component of Engel's inject 4.0 smart factory program.
Ron Shinn, editor
Contact:
Engel Machinery Inc., 717-764-6818, www.engelglobal.com
Ron Shinn | Editor
Editor Ron Shinn is a co-founder of Plastics Machinery & Manufacturing and has been covering the plastics industry for more than 35 years. He leads the editorial team, directs coverage and sets the editorial calendar. He also writes features, including the Talking Points column and On the Factory Floor, and covers recycling and sustainability for PMM and Plastics Recycling.
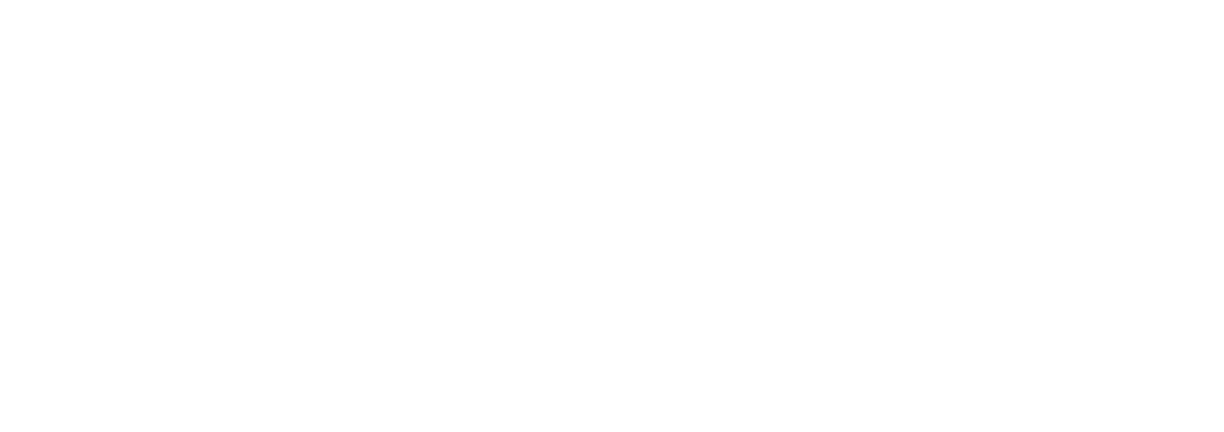